Self-lubricating copper sleeves, as a new type of lubricating bearing that combines the advantages of metal and self-lubricating materials, have been widely used in many industrial fields, such as metallurgy, mining, ships, steam turbines, injection molding machines, etc., due to their high load capacity, impact resistance, high temperature resistance and excellent self-lubricating ability. For copper sleeve buyers, it is very important to understand their casting process. The casting process of self-lubricating copper sleeves is a complex and delicate technology. When choosing copper sleeves, buyers should comprehensively consider factors such as materials, processes, performance and use environment. By understanding the principles and characteristics of the casting process, buyers can better choose copper sleeves that suit their needs to ensure the stable operation and long-term benefits of mechanical equipment.
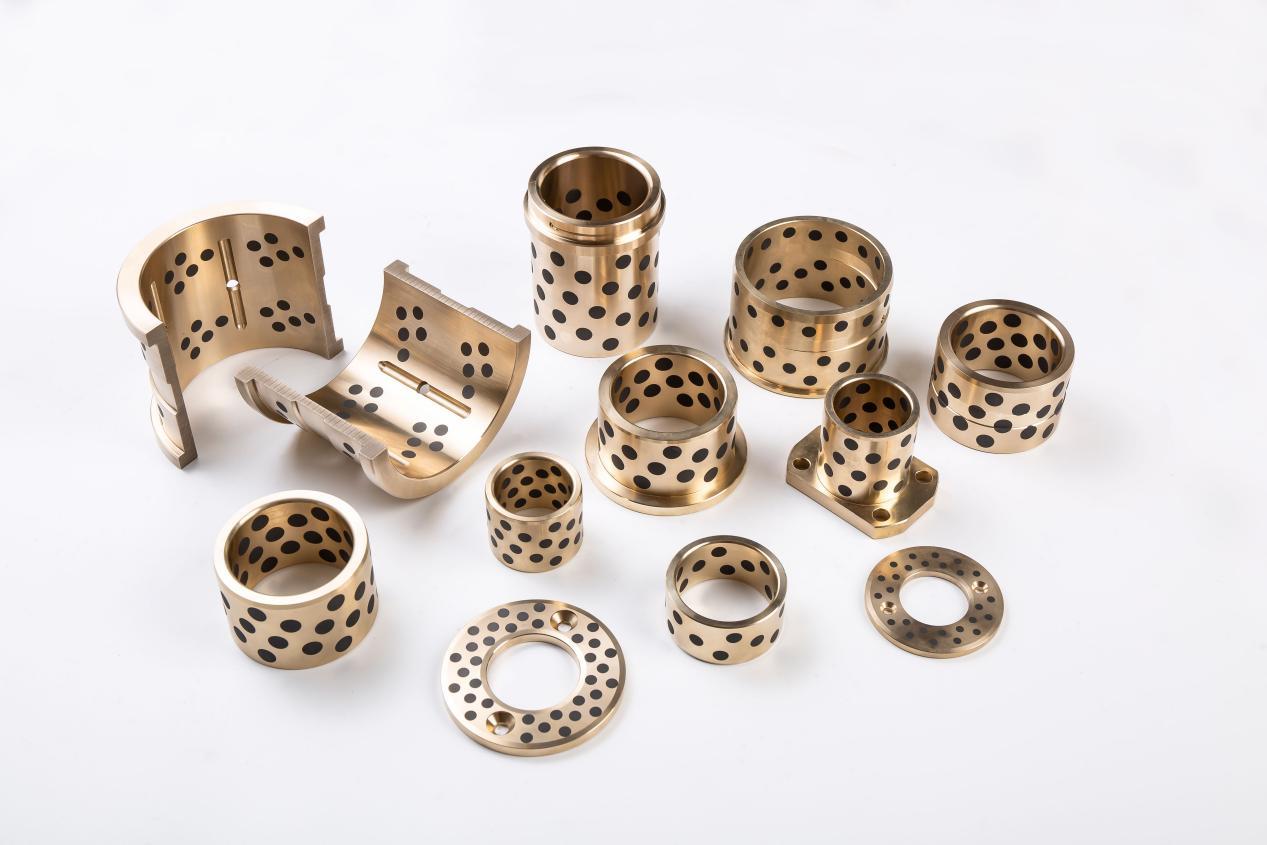
1. Overview of casting process
Copper sleeve casting is to melt the copper alloy into a liquid that meets the requirements, pour it into the casting mold, and obtain a casting with a predetermined shape, size and performance after cooling, solidification and cleaning. According to the characteristics of the casting process and the degree of development of use, the casting methods of copper sleeves are mainly divided into two categories: sand casting and special casting.
Sand casting:
Advantages: strong adaptability and simple production preparation.
Disadvantages: low dimensional accuracy and surface quality of castings, complex production process, and large investment in mechanized and automated production.
Special casting: including investment casting, metal mold casting, pressure casting, lost foam casting, centrifugal casting, continuous casting, extrusion and liquid stamping casting. These methods can improve the dimensional accuracy and surface quality of castings and are suitable for the production of high-precision and high-performance copper sleeves.
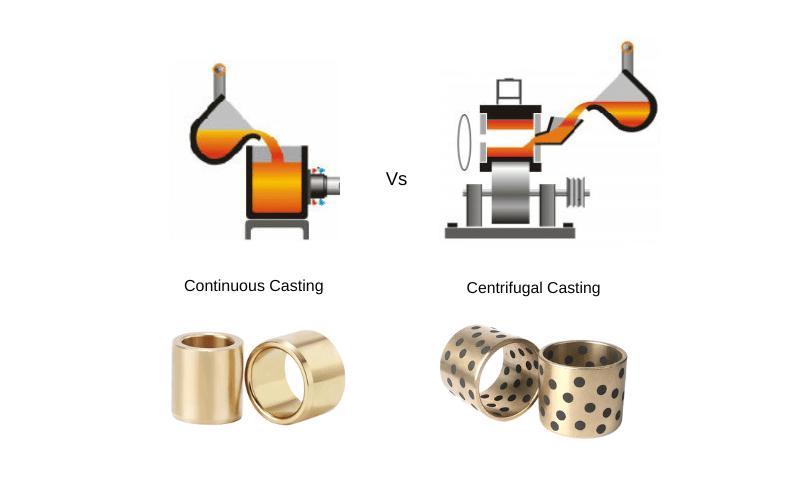
2. Casting process characteristics of self-lubricating copper sleeves
In the casting process of self-lubricating copper sleeves, the key is how to form a layer of material with self-lubricating properties on the surface or inside of the copper material. Common processes include:
Graphite powder die-casting process:
Principle: Spray a layer of graphite powder on the surface of the copper material, and then die-cast under high temperature and high pressure conditions to allow the graphite powder to penetrate into the copper material to form a uniform self-lubricating ink layer.
Advantages: Reduce wear and friction, increase service life; save energy; low production cost.
Metal-based inlay process:
Principle: Inlay graphite and other solid lubricants into the base material of the copper sleeve to form a metal-based inlay solid self-lubricating bearing.
Features: high load-bearing capacity, impact resistance, high temperature resistance, especially suitable for heavy load, low speed, reciprocating or swinging, etc., which are difficult to lubricate and form oil film.
3. Technical parameters of common self-lubricating copper sleeves
Graphite copper sleeves:
Base material: CuZn24Al6 high-strength brass or CuSn6Zn6Pb3 (6-6-3 tin bronze).
Base hardness: Hb230 (high hardness Hb270) or HB 90.
Friction coefficient: <0.16 or <0.15s.
Maximum operating temperature: 300℃ or 350℃.
Ultimate dynamic load: 100 N/mm² or 60 N/mm².
Maximum sliding speed: dry 0.40 m/s, oil 5 m/s.
Other self-lubricating copper sleeves:
Cast iron-based graphite self-lubricating plate: The base material is Steel+CuSn6Zn6Pb3 (45# steel + 663 tin bronze), the friction coefficient is <0.14, and the maximum operating temperature is 300℃.
Bowl-shaped graphite support seat: The base material is HT-250 (gray cast iron), the friction coefficient is <0.17, and the maximum operating temperature is 400℃.
Self-lubricating graphite copper slide plate: The base material is GCr15 (bearing steel), the friction coefficient is <0.17, and the maximum operating temperature is 350℃.
4. The influence of casting process on the performance of copper sleeves
Material selection: High-strength brass, aluminum bronze and tin bronze can all be used to make self-lubricating copper sleeves, but tin bronze and aluminum bronze have better performance and higher prices. The selection and arrangement of graphite also affect the lubrication effect.
Technology level: Advanced casting technology can ensure uniform distribution of materials and improve product performance. For example, investment casting and metal mold casting can produce high-precision and high-performance copper sleeves.
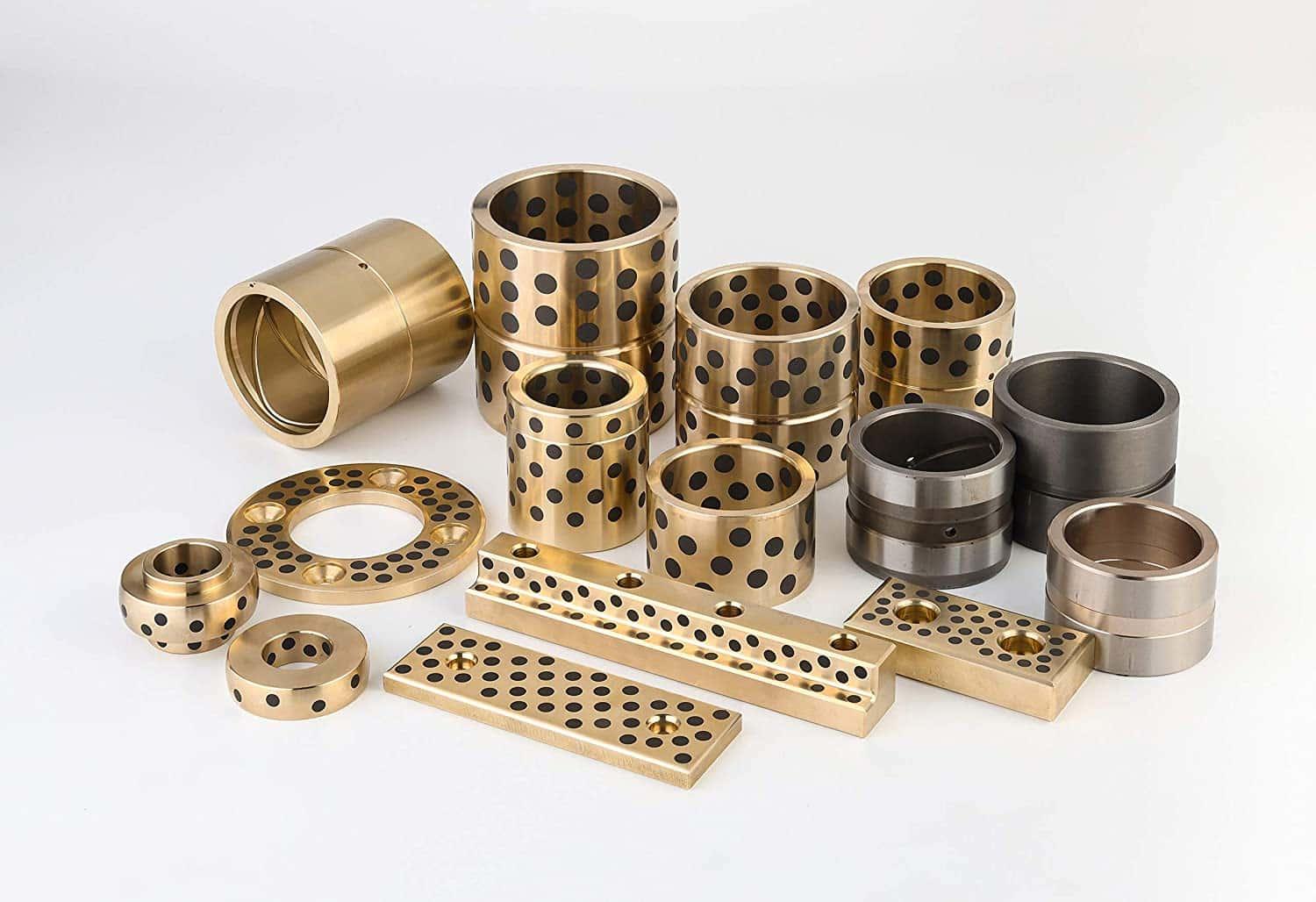
Zhejiang Mingxu Machinery Manufacturing Co., Ltd. has been focusing on the production of self-lubricating bearings for more than ten years. We are your reliable cooperation choice. If you have purchasing needs, please contact us: [email protected]
Contact Us