A self-lubricating copper bush is a bearing component with self-lubricating properties, typically achieved by machining holes on the working surface of the copper bush and filling them with solid lubricants. During the sliding friction process between the shaft and the bearing, these solid lubricants gradually transfer to the friction surface, forming a relatively stable solid lubricating film. This lubricating film prevents direct adhesive wear between the shaft and the bearing, thereby reducing the friction coefficient and improving wear resistance. So, apart from the common graphite particles, what other solid lubricants can be considered?
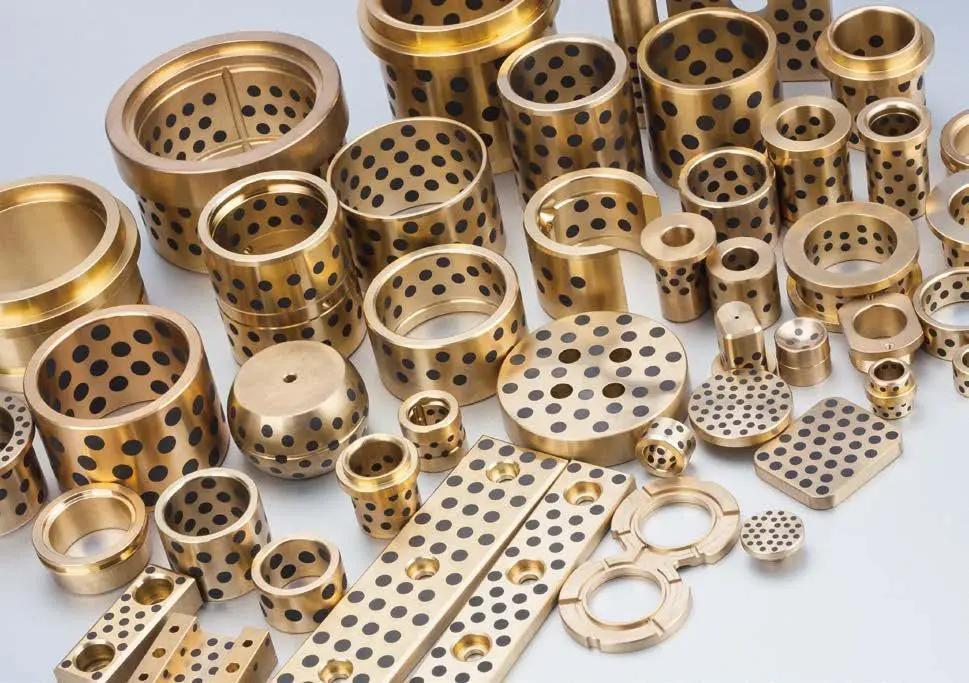
Molybdenum disulfide (MoS2) is a commonly used solid lubricant, widely applied in various lubrication scenarios due to its excellent lubrication and anti-wear properties. In self-lubricating copper bushes, molybdenum disulfide can be embedded in the holes as a solid lubricant, forming a lubricating film when rubbed against the shaft, which reduces the friction coefficient and enhances wear resistance.
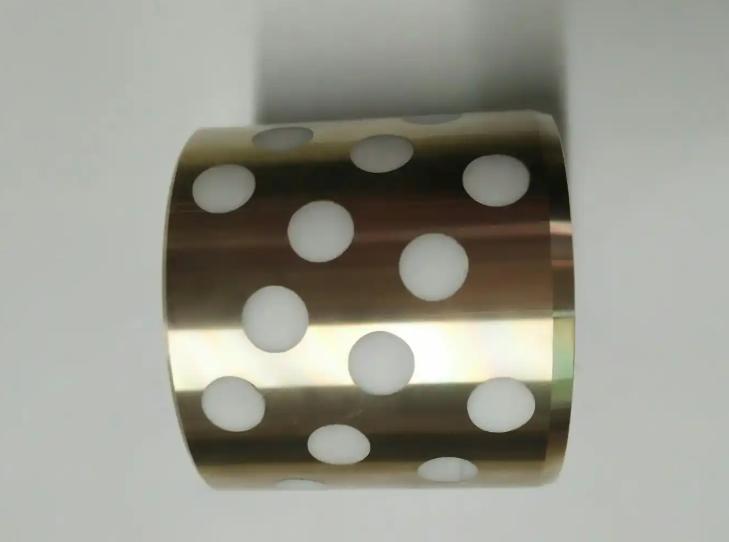
Other possible solid lubricants: Besides graphite and molybdenum disulfide, there are other solid lubricants that can be considered for use in self-lubricating copper bushes, such as:
l Polytetrafluoroethylene (PTFE): PTFE has an extremely low friction coefficient and good wear resistance, making it suitable as a solid lubricant.
l Boron nitride (BN): Boron nitride exhibits excellent lubrication performance and chemical stability at high temperatures, making it suitable for lubrication in high-temperature environments.
l Zinc sulfide (ZnS): Zinc sulfide also demonstrates good lubrication properties under certain specific conditions.
However, it should be noted that different solid lubricants have varying performance characteristics and application environments. Therefore, factors such as usage conditions, lubrication requirements, and cost need to be comprehensively considered when making a selection. When choosing a solid lubricant, in addition to considering factors such as friction coefficient, wear resistance, chemical stability, and cost, it is also necessary to conduct a detailed assessment based on the specific application scenario and equipment requirements. Only through comprehensive consideration and careful selection can we ensure that the chosen solid lubricant fully exerts its lubrication effect, enhancing the overall performance and operational efficiency of the equipment.
l Friction coefficient: Choosing a solid lubricant with a low friction coefficient can reduce frictional resistance and improve the operational efficiency of the equipment.
l Wear resistance: The solid lubricant should have good wear resistance to extend the service life of the equipment.
l Chemical stability: The solid lubricant should maintain chemical stability in the working environment to avoid chemical reactions with the medium that could lead to performance degradation.
l Cost: The cost of the solid lubricant is also a factor to consider when making a selection, and it should be chosen based on actual needs and budget.
Zhejiang Mingxu Machinery Manufacturing Co., Ltd., as a professional manufacturer of self-lubricating bearings, has in-depth research and application experience in self-lubricating bearings and their solid lubricants. We are committed to providing customers with high-quality self-lubricating copper alloy products and professional technical support to meet the needs of different industries and application scenarios. For purchasing inquiries or technical exchanges, please contact us at: [email protected].
Contact Us