With the characteristics of maintenance-free, low friction, high temperature resistance and long life, self-lubricating bearings are gradually expanding from traditional industrial fields (such as machinery manufacturing, automobiles, etc.) to emerging fields. With the advancement of science and technology and the upgrading of market demand, the application attempts of self-lubricating bearings in new energy, robots, aerospace, medical equipment and other fields are increasing, showing great development potential.
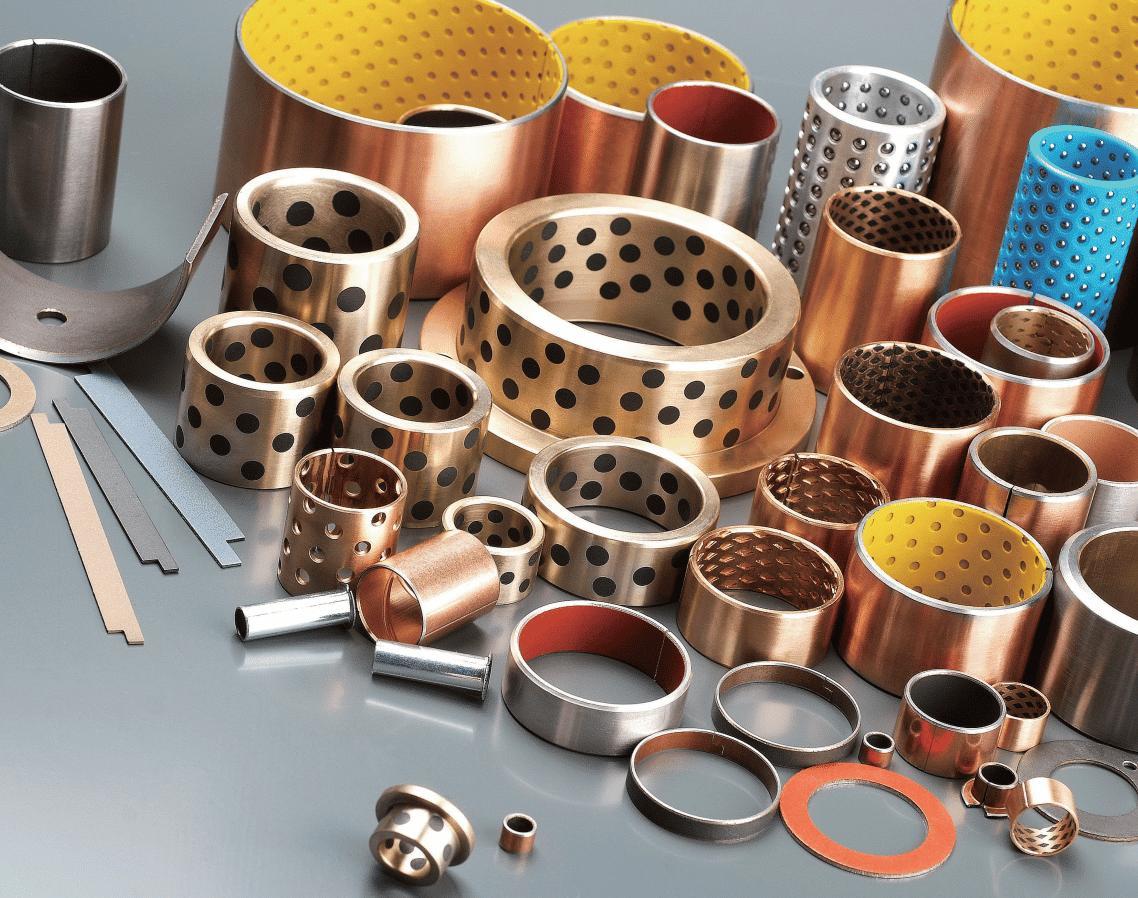
I. Application attempts in emerging fields
1. New energy vehicle field
Application scenarios:
-Electric drive system: used in key parts such as motor bearings and reducer gear shafts, which need to withstand high speeds (up to 20,000 rpm) and frequent starts and stops.
-Battery cooling system: Cooling pump bearings working in high temperature environments (80-120℃) need to be maintenance-free for a long time.
Technical breakthroughs:
-Lightweight design: Self-lubricating copper-based bearings containing graphite or PTFE are manufactured through powder metallurgy process, which reduces weight by 30% while maintaining high load capacity (static load up to 200 MPa).
-High temperature resistance: Using new composite materials (such as copper-graphene), the friction coefficient is stable at 0.08-0.12 at 120°C, and the service life is extended to twice that of traditional bearings.
Case:
The motor bearings of Tesla Model 3 use self-lubricating copper sleeves to reduce the risk of lubricant contamination and improve motor efficiency (efficiency of more than 95%).
2. Robotics and intelligent manufacturing
Application scenarios:
-Collaborative robot joints: require high precision (repeat positioning accuracy ±0.02mm), low friction (friction coefficient ≤0.1) and silent operation.
-Industrial robot guide rails: long-term maintenance-free in dusty and high-humidity environments.
Technological breakthroughs:
-Compound lubrication layer: A lubrication layer containing MoS₂ is formed on the bearing surface through laser cladding technology, and the friction coefficient is reduced to 0.05 and the noise is ≤45 dB.
-Intelligent integration: embedded sensors monitor the wear status of bearings to achieve predictive maintenance (failure rate reduced by 40%).
Case:
ABB's collaborative robot YuMi uses self-lubricating spherical bearings, which do not require external lubricants and are suitable for clean workshop environments.
3. Aerospace field
Application scenarios:
-Satellite deployment mechanism: Bearings working in vacuum and extreme temperature differences (-150℃ to +120℃) require zero volatile pollution.
-Aircraft landing gear: long-term lubrication under high impact loads (dynamic load ≥500 kN).
Technological breakthrough:
-Space-grade materials: copper-tungsten disulfide composite materials are used, and the friction coefficient is stable below 0.1 in a vacuum environment, and the volatile content is <1 ppm.
-Fatigue-resistant design: gradient material bearings are manufactured through centrifugal casting process, and the fatigue life is increased to 3 times that of traditional bearings.
Case:
The solar panel deployment mechanism of SpaceX Starlink satellite uses self-lubricating bearings to ensure reliable operation in the space environment.
4. Medical device field
Application scenarios:
-Surgical robot drive shaft: biocompatible materials (such as titanium alloy-based self-lubricating bearings) and ultra-low friction (friction coefficient ≤ 0.08) are required.
-MRI equipment bearings: no metal interference in strong magnetic field environment, ceramic-based self-lubricating materials are used.
Technological breakthroughs:
-Biocompatible coating: The lubricating layer containing DLC (diamond-like carbon) is prepared by PVD (physical vapor deposition) technology, and the friction coefficient is as low as 0.06.
-Non-magnetic materials: The magnetic susceptibility of zirconia ceramic bearings is less than 1×10⁻⁶, which is fully compatible with MRI environment.
Case:
The robotic arm joints of the da Vinci surgical robot use titanium-based self-lubricating bearings to meet medical-grade cleanliness and precision requirements.
5. Renewable energy field
Application scenarios:
-Wind turbine pitch system: long-term maintenance-free in salt spray and high humidity environments (humidity> 90%).
- Wave energy generation device: underwater bearings need to be corrosion-resistant (salt spray test ≥ 1000 hours) and resistant to biological attachment.
Technological breakthroughs:
- Corrosion-resistant coating: Plasma spraying Al₂O₃-TiO₂ composite coating is used to improve salt spray resistance to more than 2000 hours.
- Self-cleaning design: The microstructure bionic design of the bearing surface (such as shark skin texture) reduces the attachment rate of marine organisms by more than 50%.
Case:
The variable pitch bearing of Siemens Gamesa offshore wind turbine adopts self-lubricating copper sleeves with a design life of 25 years and a maintenance cost reduction of 60%.
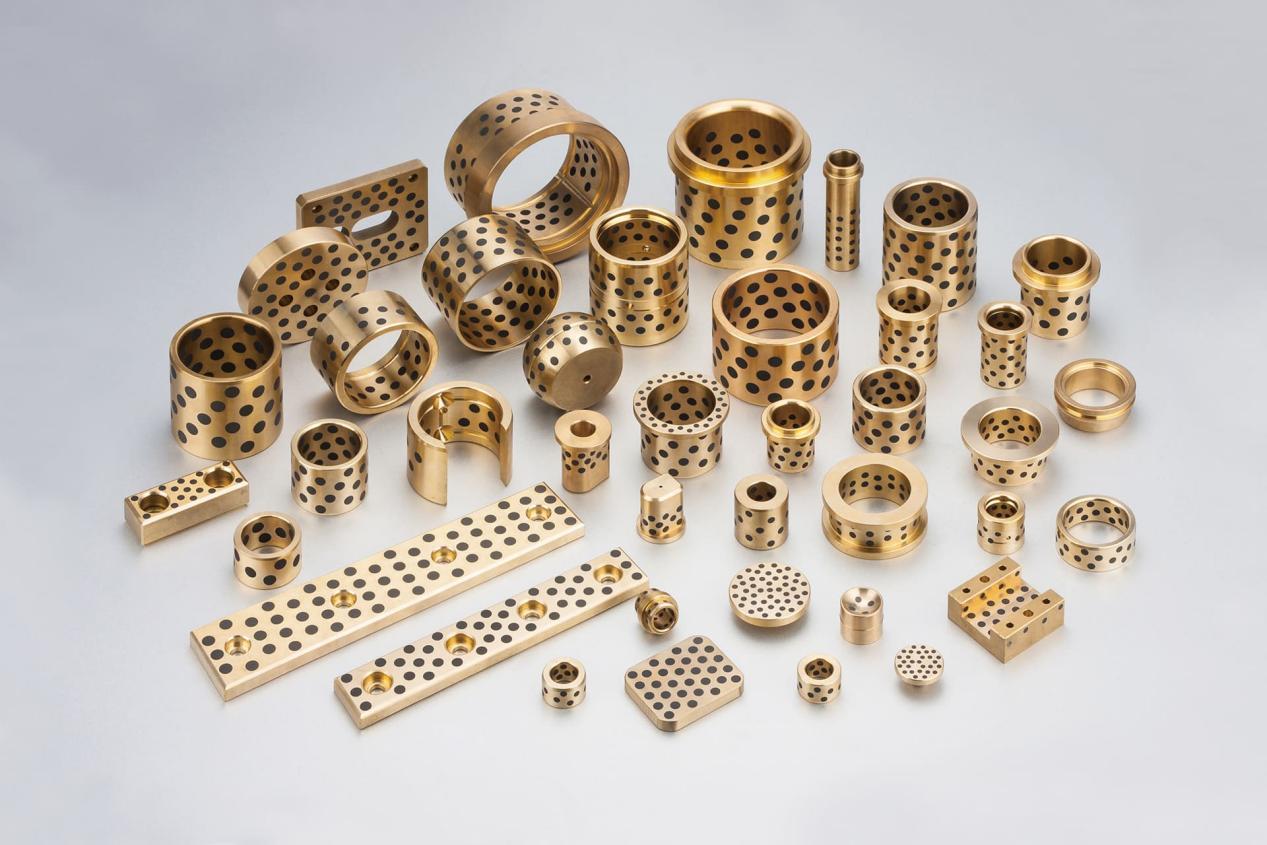
II. Future prospects and trends
1. Technology development trends
- Material innovation: The application of new lubricating materials such as graphene and nano-molybdenum disulfide is expected to reduce the friction coefficient to below 0.03.
- Intelligence: Integrate IoT sensors to monitor bearing temperature, vibration and wear status in real time to achieve "intelligent self-lubrication".
- Green manufacturing: Development of lead-free and cadmium-free environmentally friendly materials (such as bismuth-based alloys) in compliance with RoHS and REACH regulations.
2. Market prospects
- Market size: According to Grand View Research, the global self-lubricating bearing market will have a compound annual growth rate (CAGR) of 6.5% from 2023 to 2030, and the market size will exceed US$5 billion in 2030.
- Key areas: New energy vehicles (30%), robots (25%), and renewable energy (20%) will become the main growth points.
3. Challenges and responses
- Extreme environment adaptation: Further material breakthroughs are required for scenarios such as nuclear reactors (radiation resistance) and deep space exploration (ultra-low temperature).
- Cost control: Reduce costs by 20-30% through large-scale production (such as continuous casting process).
The application of self-lubricating bearings in emerging fields is not only a reflection of technological upgrading, but also the result of the deep integration of industrial demand and materials science. With the breakthrough of new materials and new processes, its application scenarios will be further expanded, becoming the "hidden champion" of high-end equipment manufacturing. For buyers, choosing technology-leading suppliers (such as Mingxu Machinery) will directly enhance product competitiveness and market response speed.
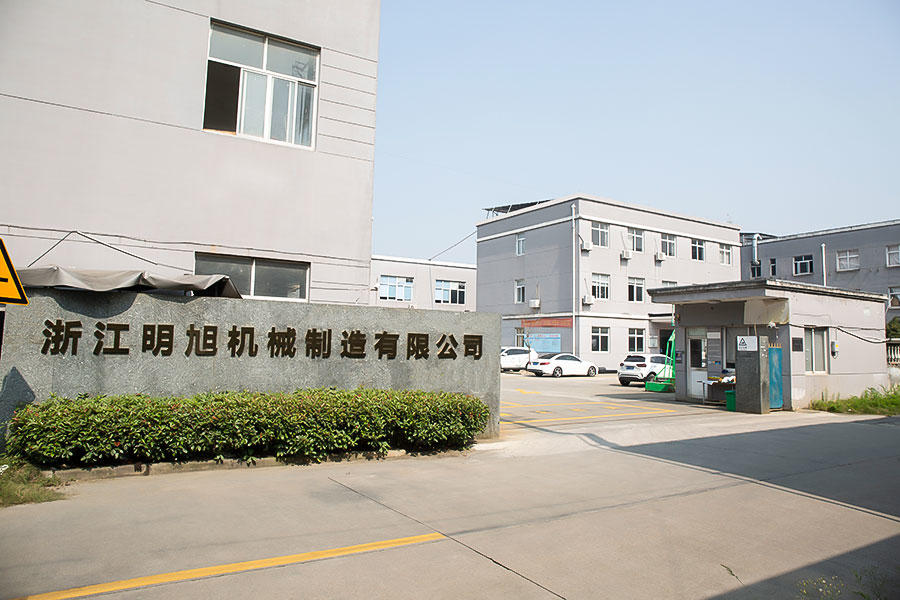
About Zhejiang Mingxu Machinery Manufacturing Co., Ltd.
Zhejiang Mingxu Machinery Manufacturing Co., Ltd. is a leading company in the field of self-lubricating bearings, focusing on the research and development and production of high-performance copper-based self-lubricating bearings. The company's products have been successfully applied to emerging fields such as new energy vehicle motors, industrial robot joints, and offshore wind power variable pitch systems, and have passed ISO 9001 certification.
Core advantages:
-Customized solutions: We can provide material formula optimization (such as adding graphene) and special coating processes according to customer needs, and accurately produce products according to customer drawings.
-Technical reserves: Passed ISO certification and has more than 10 patents.
-Delivery time: 15~20 working days from the date of order.
-Successful case: Provide motor bearings for a leading new energy vehicle company to help its electric drive system efficiency increase to 96.5%.
In the future, Mingxu Machinery will continue to deepen its roots in emerging fields and promote the development of self-lubricating bearing technology in a more efficient and intelligent direction.
Contact Us