In the field of automobile manufacturing, the stamping process is known as the "skeleton engineering of body forming", and its precision and efficiency directly determine the appearance quality and production cost of the whole vehicle. With the popularization of lightweight materials such as high-strength steel and aluminum alloy, traditional stamping dies face three core pain points: lubrication failure, thermal damage, and frequent maintenance. Conventional oil-based lubrication is prone to oil film rupture during high-speed stamping, causing the surface roughness defect rate of parts to rise to 5%-8%; the material softening phenomenon caused by the local temperature rise of the mold makes the rebound control of high-strength steel plates more difficult.
The emergence of copper-based inlaid self-lubricating wear plates provides a breakthrough solution to this industry problem. This technology achieves the coordinated optimization of the triple performance of "structure-lubrication-heat dissipation" through the deep combination of material science and tribology principles. Unlike passive external lubrication, its innovative self-replenishment mechanism enables the mold to maintain a stable friction interface under high pressure and high temperature conditions, while reducing lubrication maintenance costs by more than 90%. At present, this technology has been verified on a large scale in the production lines of the world's leading automakers, with the comprehensive efficiency of a single set of molds increased by more than 40%, and has opened up a new path for the low-carbon manufacturing of new energy vehicles.
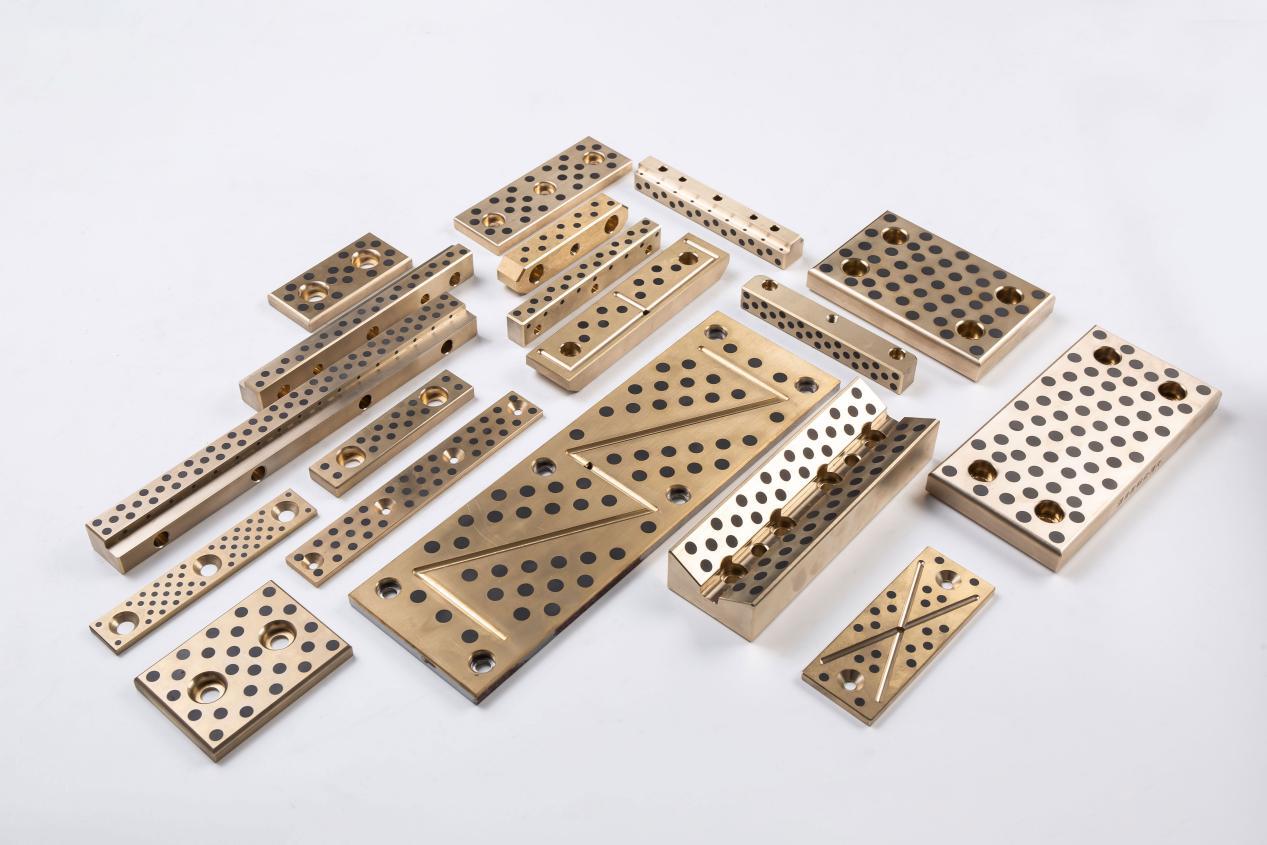
1. Innovative material structure design
The core competitiveness of the copper-based inlaid self-lubricating skateboard comes from its unique material composite structure and physical properties. From the microstructural observation, this material uses gradient sintering technology to construct a three-dimensional interpenetrating network-a high-purity copper alloy matrix (CuSn10Ni3) forms a continuous metal phase, and its porosity is precisely controlled between 12%-15%, and graphite/PTFE composite lubricating particles with a particle size of 5-20μm are evenly distributed inside. This design enables the material to have both the load-bearing capacity of metals and the friction reduction characteristics of non-metals. When subjected to a dynamic load of 300-800MPa, the pore structure can effectively buffer stress concentration and avoid the brittle peeling problem common in traditional copper-based composite materials.
2. Intelligent self-lubricating response mechanism
The realization of self-lubricating performance depends on the intelligent response mechanism: when the temperature of the contact surface between the mold and the sheet reaches 80-120℃ (common in high-speed stamping conditions), the embedded lubricating particles expand due to heat and migrate along the pore channels to the friction interface. Through thermogravimetric analysis (TGA) testing, it was found that the lubricant release rate was stable at 0.15mg/stroke in 5000 consecutive stamping cycles, ensuring that a solid lubricating film with a thickness of 0.5-1μm was always maintained. This self-replenishing characteristic reduces the friction coefficient from 0.18-0.25 in the traditional process to 0.08-0.12, effectively suppressing the common zinc layer adhesion phenomenon during the stamping of galvanized steel sheets.
3. Efficient thermal management performance
The thermal management ability of the material is also outstanding. The high thermal conductivity of the copper matrix (≥180W/m·K) combined with the micro-groove heat dissipation structure designed on the surface can reduce the peak temperature of the contact surface by 60-80℃. When stamping high-strength dual-phase steel (DP980) in a certain automobile factory, the temperature of the mold insert dropped from 210℃ before the transformation to 135℃, avoiding the strength loss caused by local annealing of the material. According to metallographic testing, the microhardness of the mold working surface using the copper-based slide plate was maintained at HV320-350, which was more than 20% higher than that of the area where this technology was not used.
4. Multi-scale wear-resistant strengthening mechanism
The improvement in wear resistance is due to the multi-scale strengthening mechanism: the nickel element in the matrix forms an intermetallic compound with tin, and the material hardness reaches HB120-140 through dispersion strengthening; nano-alumina particles (addition amount 3wt%) form a transfer film during friction to reduce abrasive wear; and the honeycomb porous structure physically isolates the lubricant reservoir from the load-bearing area through mechanical bite action to ensure structural integrity. The bench test shows that after simulating 300,000 stamping cycles, the wear of the slide plate is only 0.12mm, which is 1/5 of the bronze graphite material under the same working conditions.
5. Green environmental protection and economic benefits
In terms of environmental benefits, this technology reduces the use of lubricating oil in the stamping process by more than 90%, and the emission concentration of volatile organic compounds (VOC) is ≤10mg/m³, which fully meets the requirements of ISO 14001 environmental management system. After a new energy vehicle company adopted this skateboard, the concentration of particulate matter in the workshop air dropped from 2.1mg/m³ to 0.3mg/m³, and the cost of mold cleaning waste liquid treatment was reduced by 75%. This green feature makes it particularly suitable for the production of special vehicles with high cleanliness requirements such as medical vehicles and food transport vehicles. From an economic point of view, a single set of molds can reduce 3-4 overhauls in its entire life cycle, and the comprehensive cost savings can reach 18-22%.
6. Industry application and technical prospects
At present, the material has passed the automotive industry standard certification such as Volkswagen VW50065 and General GMW16362, and the penetration rate in the cover molds of mainstream domestic car companies exceeds 35%. With the popularization of large presses above 8,000 tons, its high pressure resistance and long life are rewriting the economic model of automotive mold maintenance. In the future, this technology is expected to be further expanded to fields such as aerospace, rail transit, etc. that have higher demand for self-lubricating materials, and promote the continuous upgrading of the manufacturing industry towards high efficiency, energy saving, and environmental protection.
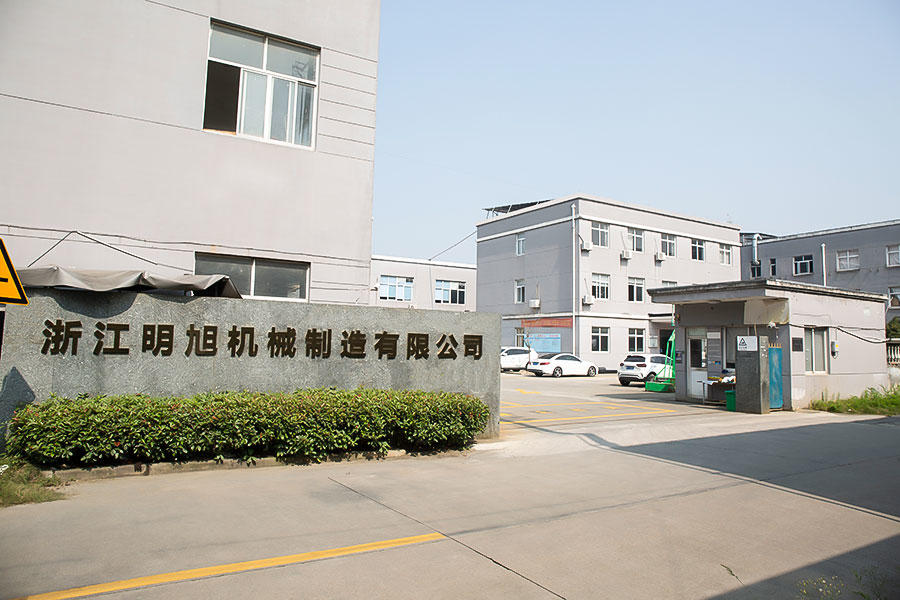
Zhejiang Mingxu Machinery Manufacturing Co., Ltd. has been focusing on the production of copper-based wear plates for more than ten years. We are your reliable cooperation choice. If you have purchasing needs, please contact us: [email protected]
Contact Us