Self-lubricating bearings often have a service life of several years to tens of thousands of hours, with the specific duration influenced by factors such as bearing type, operating environment, and workload. To ensure their stable operation, it is necessary to regularly inspect the working condition of self-lubricating bearings during the production process. If the following situations occur, it may be time to replace the bearings:
Noise and vibration: If the bearing produces sharp friction sounds, buzzing, or significantly increased vibration during operation, it may be a sign of wear or damage. Using a sound level meter to monitor the rolling sound of the bearing, abnormal or irregular sounds often indicate bearing damage.
Temperature and lubrication status: Abnormal temperature rise or poor lubrication, such as degraded or dried-out grease, are also considerations for bearing replacement.
Visual inspection: Manually rotate the outer ring of the bearing to check if it rotates smoothly without radial play. Carefully inspect the inner and outer raceways, rolling elements, and cage of the bearing to confirm the absence of cracks, peeling, severe wear, or looseness. If there is obvious wear, cracks, peeling, or deformation on the bearing surface, replacement is necessary.
Performance evaluation: If the operating efficiency of the equipment decreases or becomes unstable, such as abnormal axial and radial displacement, it may be a manifestation of bearing issues. The gap between the inner and outer rings and the rolling elements can be measured; under normal circumstances, this gap should be within the range of 0.005 to 0.010mm, and there should be no significant sound during axial vibration.
Maintenance records and life assessment: Based on the rated life of the bearing, operating conditions, and maintenance records, comprehensively assess whether the bearing needs to be replaced.
In addition, to extend the service life of the bearing, it is necessary to regularly clean and replace the lubricant, avoid overload operation, pay attention to the working conditions of the bearing, and select the appropriate bearing model. Once any abnormal signs are detected, immediate thorough inspection should be conducted, and necessary maintenance or replacement measures should be taken.
So, what are the key points to consider when selecting self-lubricating bearings?
Clear understanding of requirements: First, it is necessary to have a clear understanding of the working conditions and requirements of the mechanical equipment, including load size, rotational speed, and operating temperature.
Type selection: According to the needs of the mechanical equipment, precisely select the suitable type of self-lubricating bearing.
Life consideration: Based on the rated life of the bearing and operating conditions, reasonably estimate the replacement cycle of the bearing.
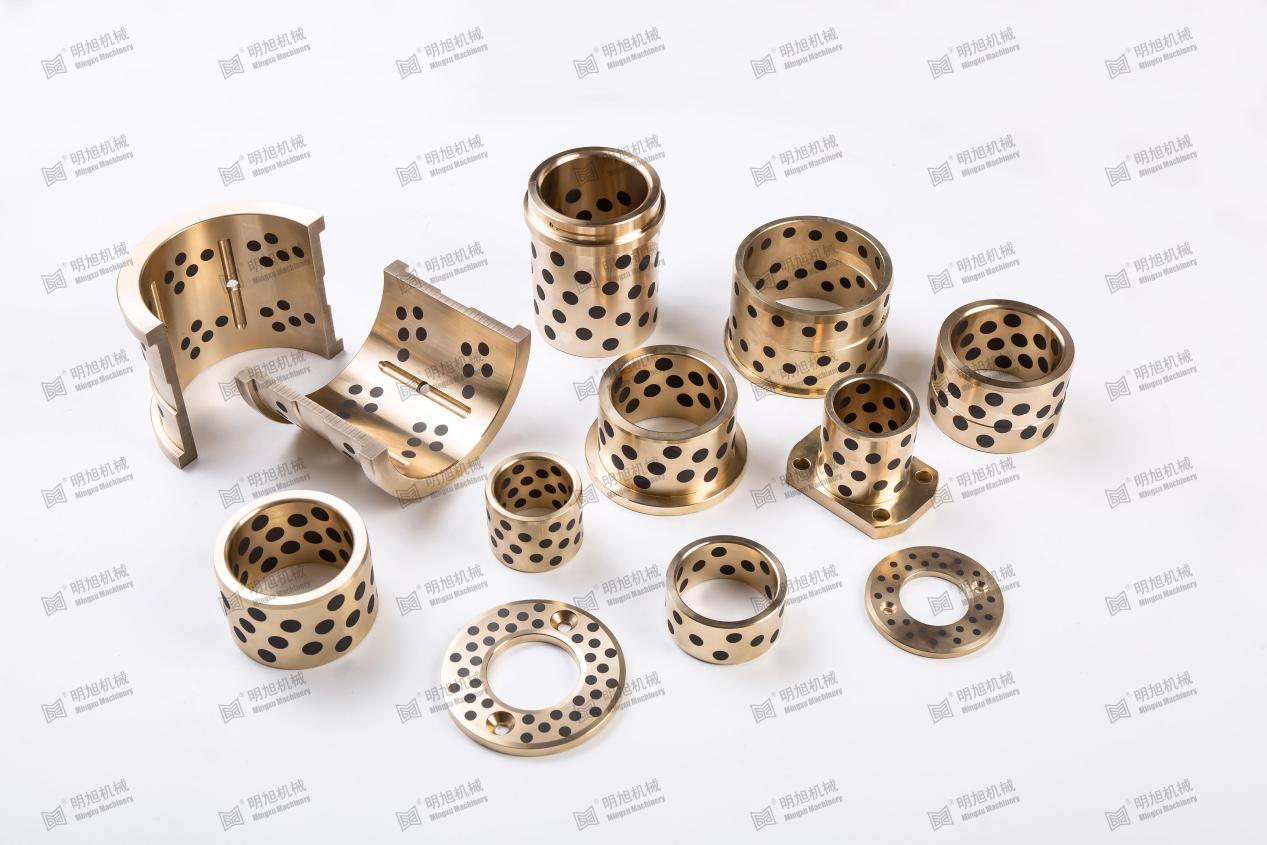
Professional consultation: If there are any questions during the selection process, you can contact the sales team of Mingxu Machinery (email: [email protected]) at any time to ensure accurate selection.
As for the precautions when replacing self-lubricating bearings, they include:
Installation preparation: Thoroughly clean the installation surface, remove all impurities and oil contamination; clearly distinguish between the friction surface and the installation surface.
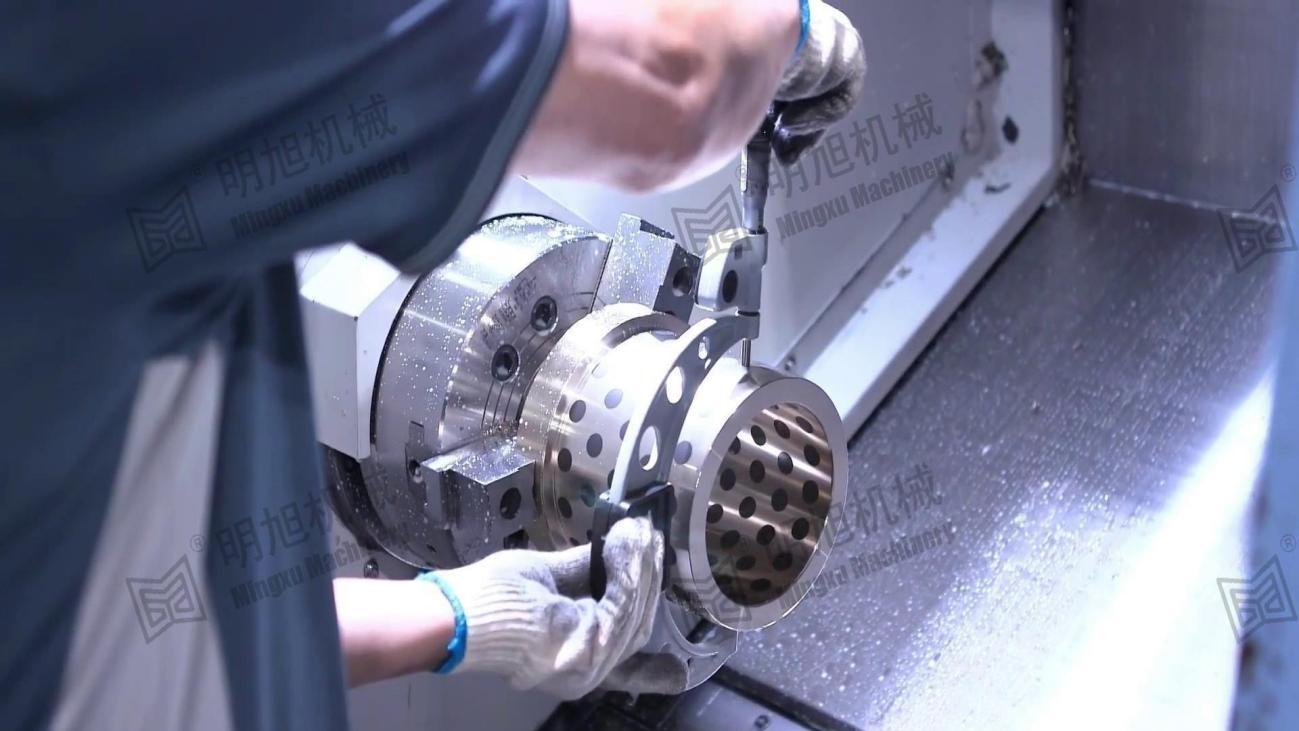
Proper installation: Use the correct installation tools and methods to ensure that the bearing is installed in place without deviation; fasteners need to be glued and tightened appropriately.
Damage prevention measures: During installation and disassembly, avoid excessive force to prevent mechanical damage to the bearing.
Contamination prevention: Keep the working environment of the bearing clean to prevent foreign objects from entering the bearing.
Contact Us