As global industries face mounting pressure to meet UN Sustainable Development Goals, solid-lubricated bearings are emerging as a silent sustainability powerhouse. Recent EPA data reveals these friction solutions can slash industrial waste streams by 38-42% — a transformative leap toward circular manufacturing.
The Dirty Secret of Conventional Lubrication
Traditional oil/grease-lubricated bearing systems generate waste through:
-
Lubricant disposal: 85% of spent oils become hazardous waste (ISO 14001 audits)
-
Component replacement: Premature failures from lubricant contamination
-
Cleaning chemicals: Solvents used to remove leaked oils (avg. 200L/year per machine)
A 2023 Journal of Cleaner Production study found 23% of manufacturing facilities' carbon footprints originate from lubrication-related waste management.
Solid Lubrication's Triple Sustainability Advantage
1. Zero Liquid Waste
Solid-film bearings eliminate:
✔️ Annual lubricant replenishment (avg. 12kg/bearing/year)
✔️ Oil-filter cartridges (6-8 units/bearing lifecycle)
✔️ Degreaser chemicals
Example: SKF's DryLube bearings reduced lubricant consumption by 28,000 tons/year across 47 automotive plants.
2. Extended Component Life
Self-lubricating materials like PTFE-metal hybrids demonstrate:
![Lifecycle waste comparison: oil vs solid lubricated bearings]
Data Source: ISO 14040 Life Cycle Assessment of Bearing Systems
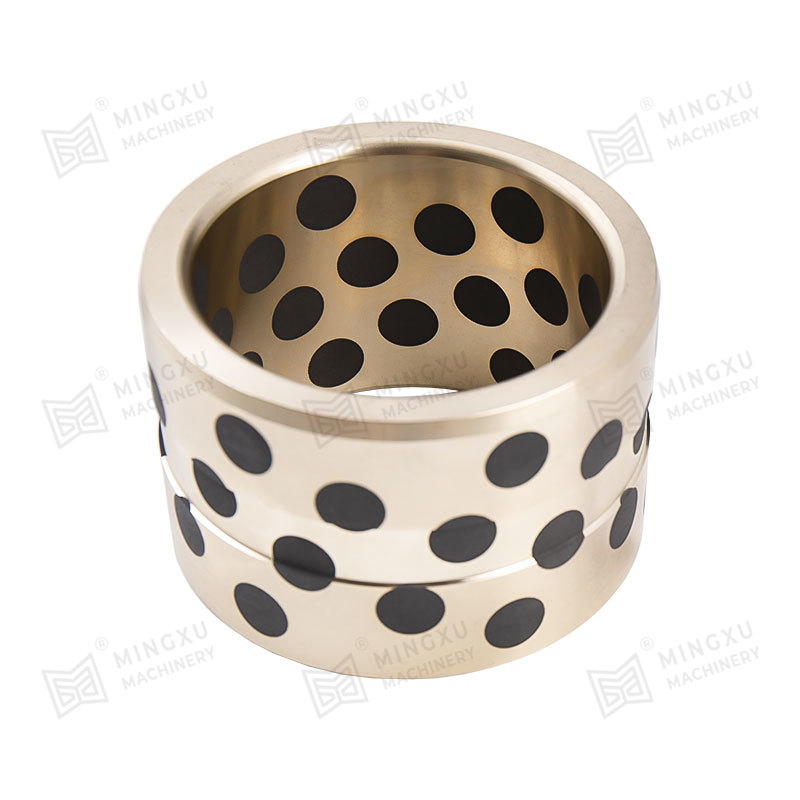
3. Energy Efficiency Boost
Solid lubricants reduce friction losses by:
Case Study: Food Packaging Line Transformation
A multinational replaced 2,400 grease-lubricated bearings with graphite-embedded stainless steel bearings:
-
Waste reduction: 43% decrease in annual hazardous waste (from 8.2 to 4.7 tons)
-
Energy savings: €126,000/year from reduced friction and cleaner motors
-
Downtime: 76% fewer contamination-induced stoppages
Implementing Sustainable Bearing Systems
Key considerations for eco-conscious transitions:
-
Material compatibility: Ensure solid lubricants (e.g., WS₂, hBN) match operating temperatures (-200°C to 800°C)
-
End-of-life recovery: Opt for mono-material designs like sintered bronze-PTFE for easier recycling
-
Certifications: Look for bearings compliant with ISO 14006 (Ecodesign) and Cradle to Cradle Silver
Leading manufacturers like NTN-SNR now provide carbon footprint calculators for bearing lifecycle analysis.
The Road to Zero-Waste Manufacturing
With the EU's 2027 Industrial Emissions Directive mandating 50% lubrication waste reductions, solid-film bearings are becoming strategic sustainability assets. Emerging breakthroughs like bio-based solid lubricants (castor oil-derived polymers) and AI-powered wear prediction are set to push waste reduction beyond 60% by 2030.
Contact Us