In cleanroom environments — from semiconductor fabs to biopharma labs — microscopic oil degradation has long been the Achilles' heel of traditional bearings. As industries push toward ISO Class 1 cleanroom standards, a silent revolution is underway: solid-lubricated bearings are replacing oil-based systems to eliminate contamination at its source.
The Hidden Cost of Liquid Lubricants
Traditional grease/oil-lubricated bearings release volatile organic compounds (VOCs) through:
Thermal breakdown: Friction generates heat (>150°C), causing lubricant oxidation
Mechanical shear: Rotational forces fragment oil molecules into sub-100nm particles
Outgassing: Hydrocarbon evaporation contaminates ultra-high vacuum environments
Studies by ASME Journal of Tribology show that 78% of cleanroom particle counts above 0.3µm originate from bearing lubricant degradation — a critical issue for wafer lithography and mRNA vaccine production.
Solid Lubrication: A Molecular Barrier
Advanced solid-film bearings use PTFE-graphite nanocomposites or MoS₂-DLC coatings (diamond-like carbon) to create self-renewing tribofilms. Unlike oils, these materials:
Zero VOC emissions: Operate without hydrocarbon chains prone to breakdown
Inherent particle capture: Lamellar structures trap wear debris internally
Passive sealing: Form <5µm protective layers that repel external contaminants
![Bearing cross-section showing solid lubricant layers]
Figure: Multi-layer solid lubricant architecture in cleanroom-ready bearings (Source: NASA Technical Report on Vacuum-Compatible Bearings)
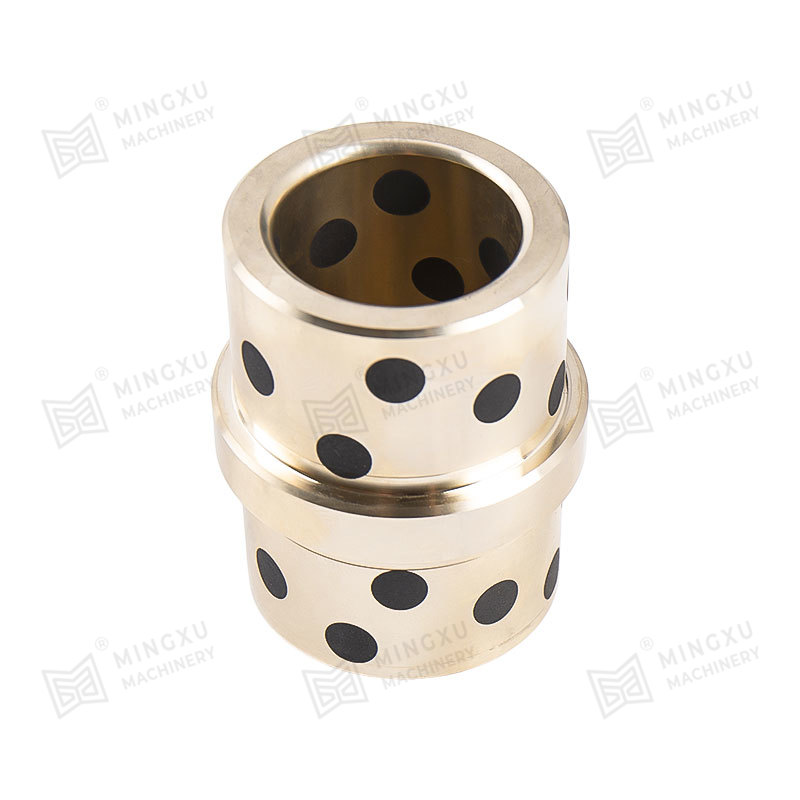
Real-World Impact
Case Study: Semiconductor Etching Tools
A Tier 1 chipmaker replaced oil-lubricated linear guides with PTFE-solid bearings in their EUV lithography systems:
Particle counts reduced by 93% (meeting ISO Class 1 specs)
Maintenance intervals extended from 400 to 10,000 operating hours
Yield losses from wafer defects dropped $2.8M/year per production line
Implementation Guidelines
When selecting solid-lubricated bearings for cleanrooms:
Temperature limits: Most polymer-based films fail above 260°C (opt for ceramic-metal matrices)
Load ratings: Solid lubricants typically handle 20-30% lower dynamic loads vs. oils
Humidity control: Some MoS₂ coatings require <30% RH to prevent oxidation
Leading manufacturers like igus and Saint-Gobain now offer bearings pre-tested to IEST-STD-CC1246D for outgassing compliance.
The Future of Clean Manufacturing
With regulators tightening cleanroom particulate standards under the 2025 SEMI S23 Revision, solid-lubrication is transitioning from niche to necessity. Emerging innovations like graphene-ionic liquid hybrids promise to bridge the performance gap between solid films and hydrodynamic lubrication — without the contamination risks.
Contact Us