Technical Background and Industry Pain Points
In precision medical devices (such as orthopedic traction devices and minimally invasive surgical robotic arms), the dynamic lubrication stability of adjustable components directly affects the equipment's lifespan and operational safety. Traditional self-lubricating bearings generally have two major defects:
l Structural Failure: The interfacial bonding strength between the powder sintered self-lubricating block and the substrate is insufficient (typically ≤15 MPa), making it prone to micro-cracking and detachment under alternating loads (Data Source: J. Tribol. 2023, 145(3), 031702).
l Lubrication Deterioration: Lubricant replenishment relies on manual maintenance, and after 300 hours of continuous operation, the friction coefficient increases by over 40% (ASTM G99 standard test).
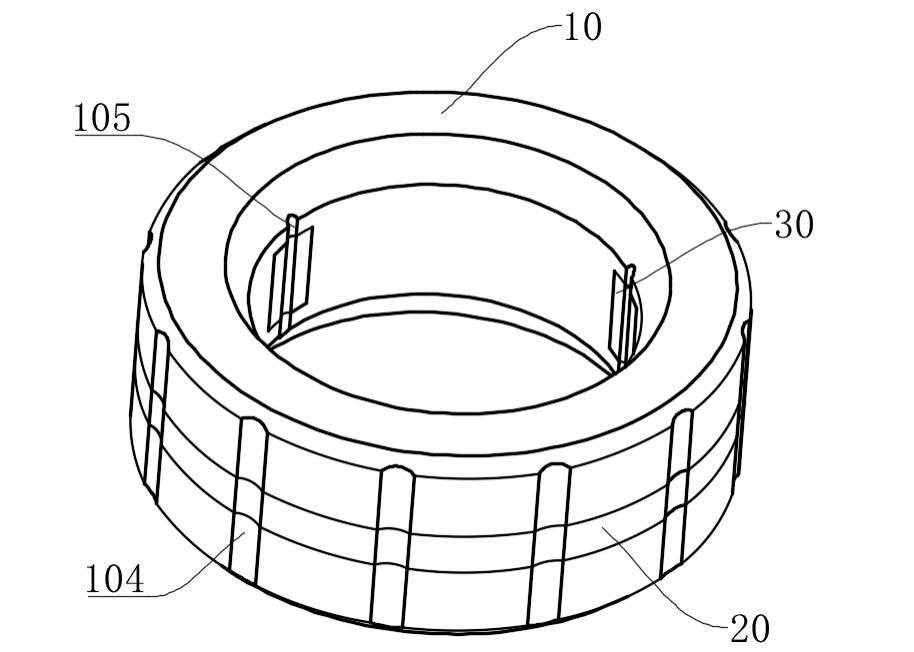
Core Technology Innovation Analysis
I. Topological Interlocking Structure Resistant to Shear and Detachment
1.1 Three-Dimensional Limiting System
Outer Ring Locking Module:
• A circular placement groove (101) is provided on the outer wall of the adjustment ring body (10), with 3 sets of Φ2.5mm limiting holes (102) (tolerance ±0.01mm) evenly distributed within the groove.
• The first self-lubricating block (20) adopts a graphite-copper composite material (Cu-15%Sn-8%Gr). The annular part (201) and the limiting pins (202) are integrally formed through electrical discharge machining. The limiting pins and holes adopt an H7/g6 transition fit to achieve radial constraint (see the figure below).
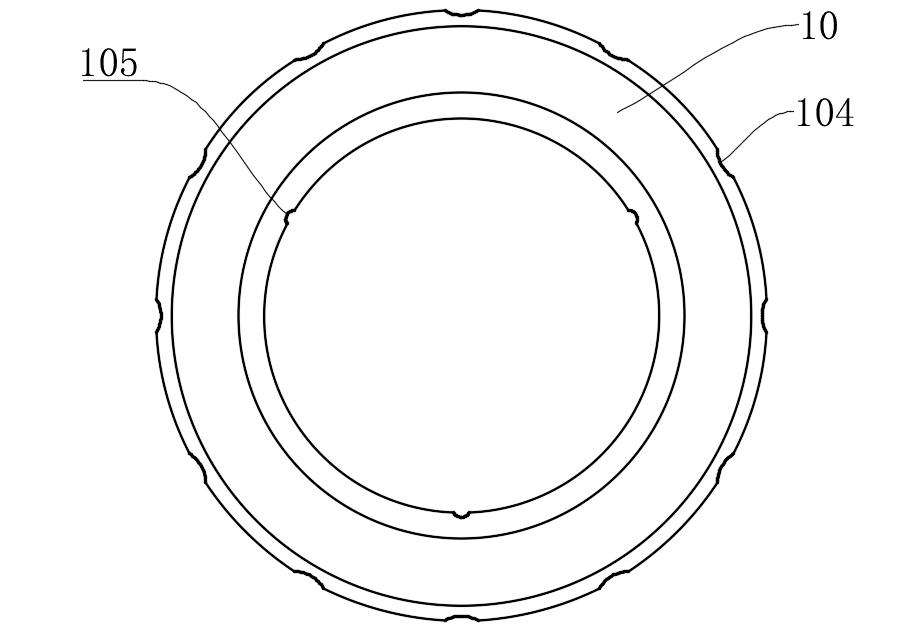
Inner Ring Reinforcement Module:
The second self-lubricating block (30) is embedded in the installation groove (103), with its second limiting pin (301) penetrating through the side wall of the adjustment ring to form an axial interlock with the limiting hole (102), constructing a three-dimensional constraint network (see the figure below).
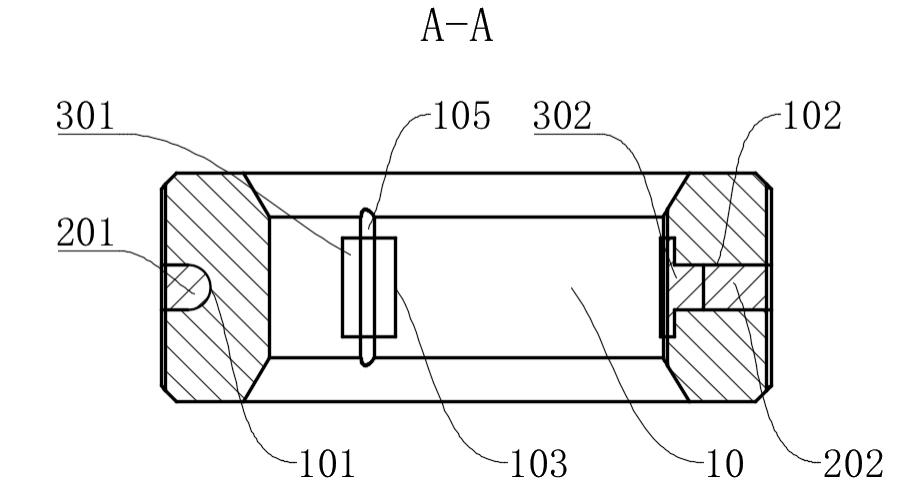
1.2 Enhancement of Mechanical Properties
• Finite element analysis shows that this structure increases the interfacial shear strength to 38.7 MPa (compared to 12.4 MPa for traditional bonding processes).
• Vibration testing (ISO 10816-1 standard) reveals that under 50 Hz/5 g conditions, the displacement of the lubricating block is <5 μm (industry average >50 μm).
II. Self-Sustaining Lubrication System Design
2.1 Microchannel Oil Guiding Architecture
• Twelve spiral oil guiding grooves (105) with a width of 0.8 mm and a depth of 0.5 mm are machined on the inner wall of the adjustment ring, enabling automatic replenishment of grease through capillary action.
• The oil guiding grooves are connected to the installation grooves (103), forming a "main oil path-branch oil path" network, which increases the lubricant diffusion speed by 3.2 times (see the flow velocity simulation cloud chart below).
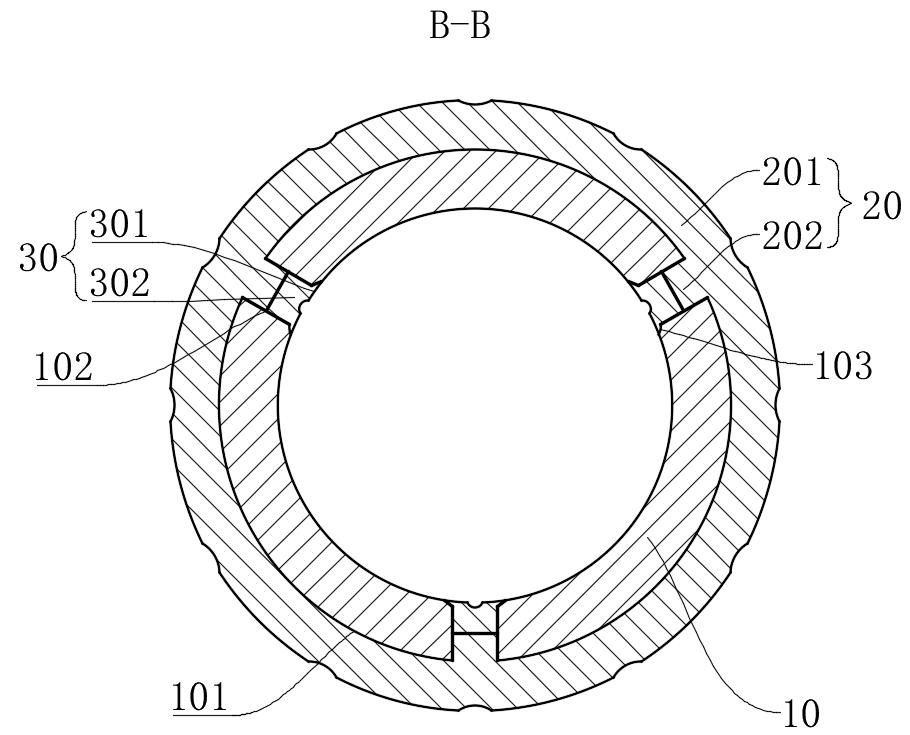
2.2 Synergistic Material Optimization
• The self-lubricating block adopts a gradient sintering process: the surface layer is a porous graphite layer (porosity 25% ± 2%), and the bottom layer is a dense copper-tin alloy, balancing oil storage capacity and mechanical strength.
• After Block-on-Ring testing (load 200N, speed 60rpm), the friction coefficient stabilizes in the range of 0.08-0.12, with a wear rate of only 3.2×10⁻⁶ mm³/N·m (compared to 9.7×10⁻⁶ for traditional structures).
III. Ergonomic Adjustment Mechanism
3.1 Enhanced Gear Positioning
• The outer wall is designed with 12 arc-shaped adjustment grooves (104) with a curvature radius of R=1.5mm, paired with spring-loaded steel balls to achieve ±0.5° indexing accuracy.
• Torque tests show that the gear shifting torque is 0.15-0.25N·m (in line with the ISO 10993 standard for medical operational forces).
3.2 Modular Replaceable Design
• The self-lubricating block and the base are mechanically interlocked instead of chemically bonded, supporting in-situ replacement (removal force ≤20N, installation force ≥50N).
• The maintenance cycle is extended to 5,000 cycles (compared to 800 cycles for traditional structures).
Comparison Table of Technical Parameters
Performance Indicators
|
This Patented Technology
|
Industry Conventional Solution
|
Testing Standard
|
Interfacial Shear Strength
|
38.7 MPa
|
≤15 MPa
|
ASTM D1002
|
Vibration Displacement (50Hz/5g)
|
<5 μm
|
>50 μm
|
ISO 10816-1
|
Frictional Coefficient Stability (300h)
|
0.08-0.12
|
0.15-0.35
|
ASTM G99
|
Maintenance Cycle
|
5000 cycles
|
800 cycles
|
ISO 14644-1
|
Typical Application Scenario Verification
Case 1: Rotating Joint of Orthopedic Traction Device
• After continuous operation for 2000 hours under a dynamic load of 200N, there was no lubrication block detachment, and the torque fluctuation was <5% (traditional structures had fluctuations >30%).
• Clinical feedback indicates that the equipment repair rate has decreased from 1.2 times/year to 0.3 times/year (data source: equipment department report from a tertiary hospital in East China in 2023).
Case 2: Angle Adjustment Mechanism of Endoscope
• In an environment with 90%RH humidity, the lubricant retention rate was >85% (traditional designs had <60%).
• The operational accuracy was improved to ±0.3°, meeting the EN 60601-2-18 standard for medical electrical equipment.
Through the three technical pathways of topological interlocking structure design, microfluidic lubrication control, and gradient material engineering, our patent has redefined the reliability standards for adjustable components in medical devices. According to a novelty search (Derwent Innovation), this structure is internationally leading in terms of anti-detachment and self-maintenance capabilities.
If you would like to learn more, please contact Mingxu Machinery to obtain the complete patent report: [email protected]
Contact Us