When designing and manufacturing graphite sliding bearings, multiple key factors need to be considered to ensure their performance and quality. Here is a more detailed explanation of these factors:
Load Capacity: This involves determining the maximum load that the bearing can withstand, including radial, axial, and combined loads. Considering both dynamic and static loads under working conditions ensures that the bearing does not overload during use, thus ensuring its lifespan and performance.
Self-lubricating Performance: Graphite sliding bearings possess self-lubricating properties, meaning they don't require additional lubricants to reduce friction and wear. Therefore, in the design and manufacturing process, appropriate graphite materials need to be selected, and the surface finish and precision of the bearing need to be ensured to maximize its self-lubricating performance.
Thermal Stability: Considering the possibility of high-temperature working conditions, it's necessary to choose graphite materials with good thermal stability and adopt appropriate manufacturing processes to ensure the bearing's stability performance under high-temperature environments. This may include material performance testing and process optimization under high temperatures.
Dimensions and Geometric Shapes: Ensuring that the bearing's dimensions and geometric shapes meet design requirements is crucial. This includes precise control of parameters such as inner diameter, outer diameter, length, cylindricity, and concentricity to ensure the bearing's stable fit and operation with other components.
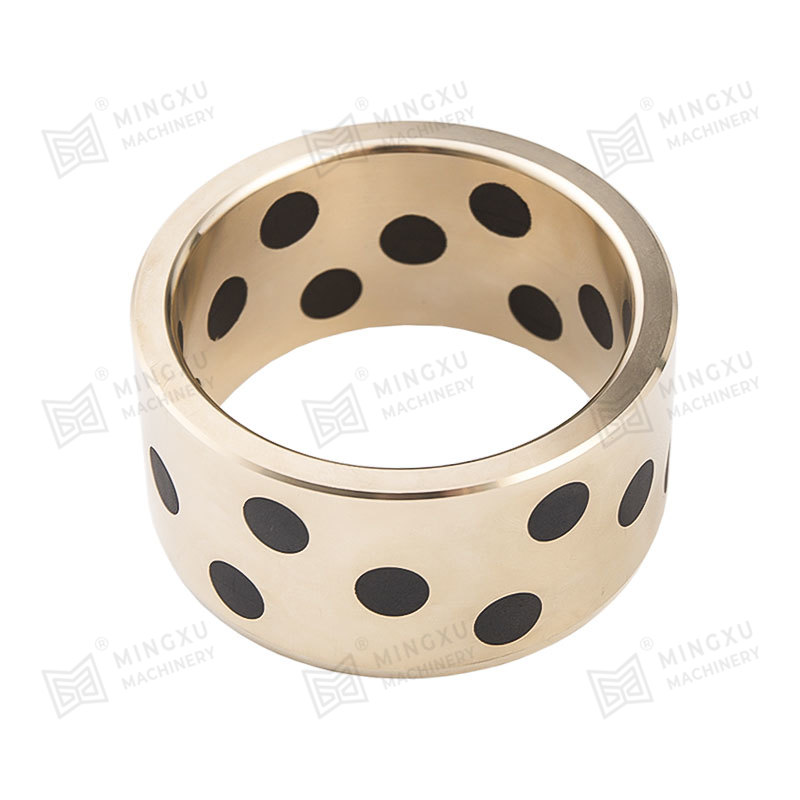
Surface Finish and Precision: The surface finish and precision of graphite sliding bearings are crucial for their performance and friction characteristics. Through appropriate machining processes and surface treatments, control of surface roughness and flatness can be achieved to reduce friction losses and improve operational efficiency.
Wear Resistance and Friction Characteristics: Considering the impact of friction and wear during operation, it's necessary to choose graphite materials with good wear resistance and friction characteristics. Surface treatments and lubrication schemes can further improve their wear resistance and friction characteristics.
Chemical Stability and Corrosion Resistance: Depending on the specific environment and working conditions of the bearing, graphite materials with good chemical stability and corrosion resistance need to be selected. Appropriate corrosion protection measures should be taken to ensure the bearing's reliability and durability in harsh environments.
Environmental Performance: Selecting environmentally friendly materials and manufacturing processes is essential to minimize the environmental impact of bearing production and use. This may involve material selection, waste treatment and recycling, and reducing energy consumption and waste emissions during the manufacturing process.
Manufacturing Cost and Scalability: While ensuring the quality of bearings, efforts should be made to reduce manufacturing costs as much as possible and consider the scalability of future production. This may involve process optimization, equipment selection and investment, and comprehensive considerations of human resources management.
Application Environment and Operating Conditions: Considering the specific environment and operating conditions in which the bearing will be used, the most suitable materials, designs, and manufacturing processes need to be selected. Factors such as temperature, humidity, chemical media, load types and sizes, operating speeds, etc., should be considered to ensure the bearing meets expected performance and lifespan in real working environments.
By considering these factors comprehensively, the designed and manufactured graphite sliding bearings can possess good performance, stability, and reliability to meet the requirements of various applications.
Contact Us