As a high-quality solid lubricant, graphite has excellent self-lubricating properties. When the copper sleeve moves relative to the shaft or other mating parts, graphite particles can be transferred to the friction interface to form a stable solid lubricating film, which greatly reduces the friction coefficient between the two and reduces wear caused by direct contact between metals. , a certain degree of lubrication effect can be guaranteed even when liquid lubricant is lacking or lubricating oil cannot be replenished.
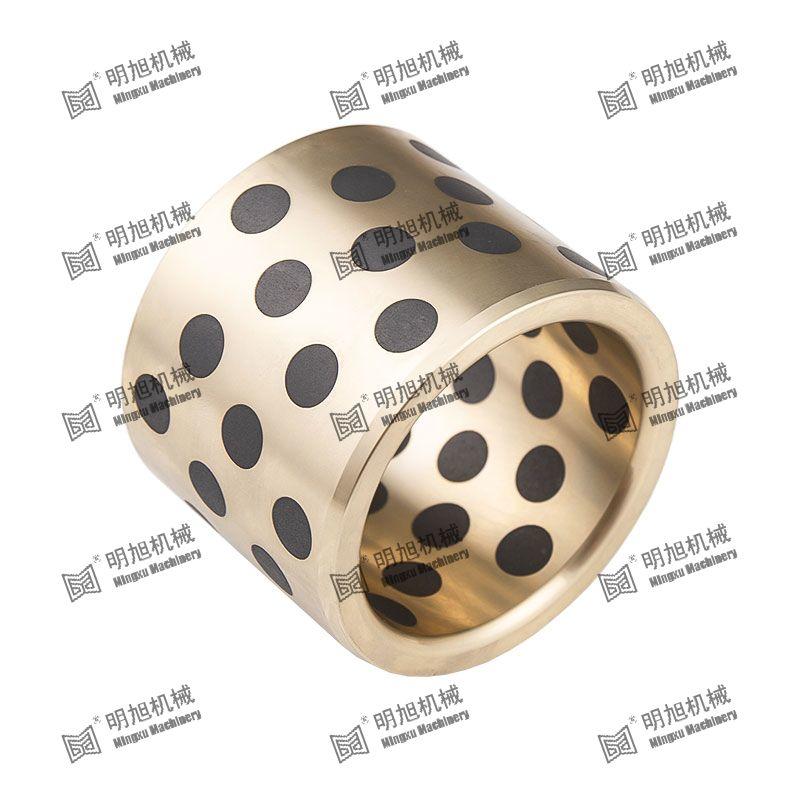
How is the graphite on the graphite copper sleeve installed? In fact, the graphite on the graphite copper sleeve is usually embedded through a specific process. This process can include the following steps:
1. Prefabricated holes or grooves: Before manufacturing the graphite copper sleeve, a series of regularly arranged holes or grooves will be prefabricated on the inner wall of the copper sleeve or the parts that need lubrication. These holes or grooves are designed to accommodate the solid lubricant - graphite.
2. Graphite preparation: Graphite will be processed into particles or blocks of specific shapes and sizes, usually cylindrical, so that they can be embedded in preset holes.
The graphite copper sleeves produced by Mingxu Bearing are generally inlaid on the copper sleeves using the following three methods:
- Hot mounting method: At a certain temperature, graphite is melted or softened with a certain resin mixture (such as a specially formulated glue), and then poured into the pre-processed holes. After cooling and hardening, the graphite is firmly fixed on the copper. Put it on.
- Cold mounting method: Use high-strength adhesive to stick graphite particles into the holes of the copper sleeve, and ensure the firm adhesion of the graphite through pressure and curing.
- Centrifugal casting method: In the process of casting the copper sleeve, a mixture containing graphite powder is injected into the rotating mold, and the graphite is evenly distributed inside the copper sleeve with the help of centrifugal force, and then cools and solidifies to form a single body.
- Curing and post-processing: After inlaying, the product may need to be placed in an oven or other heating device for curing treatment to ensure sufficient bonding strength and stability between the inlaid graphite and the copper sleeve.
- Finishing: Finally, the graphite copper sleeve after the inlay process will undergo subsequent mechanical processing, such as grinding, polishing, etc., to meet the dimensional accuracy and surface quality requirements of the final product.
In summary, inlaying graphite into a copper sleeve is a process that combines physical and chemical means, aiming to make full use of the excellent self-lubricating properties of graphite while maintaining the structural strength and stability of the copper sleeve.
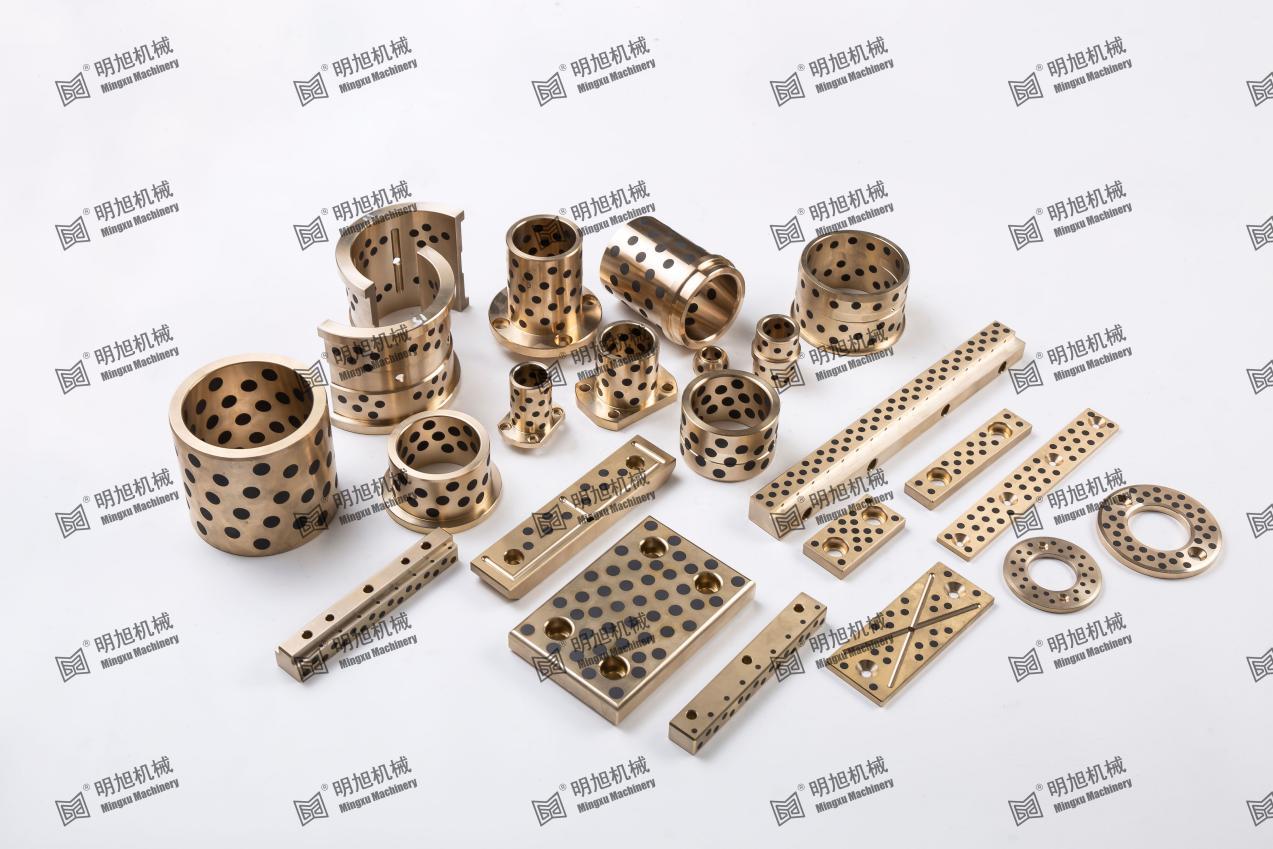
Contact Us