Several machining processes are commonly used to achieve the required tolerances for graphite sliding bearings. These processes are chosen based on factors such as the complexity of the bearing design, the desired surface finish, and the level of precision needed. Here are some of the most common machining processes:
Milling:Milling involves removing material from a workpiece using rotary cutters. It can be performed on vertical or horizontal milling machines.Milling is used to create features such as grooves, slots, and flat surfaces on graphite sliding bearings.Versatile, suitable for various geometries, and can achieve tight tolerances.Graphite dust generated during milling requires proper ventilation and dust control measures to prevent health hazards and machine contamination.
Turning:Turning involves rotating a workpiece against a stationary cutting tool to remove material and create cylindrical shapes.
Application: Turning is used to create cylindrical bearing surfaces and achieve concentricity.High precision, fast cycle times, and excellent surface finish.Tool wear and heat generation should be managed to prevent surface defects on graphite.
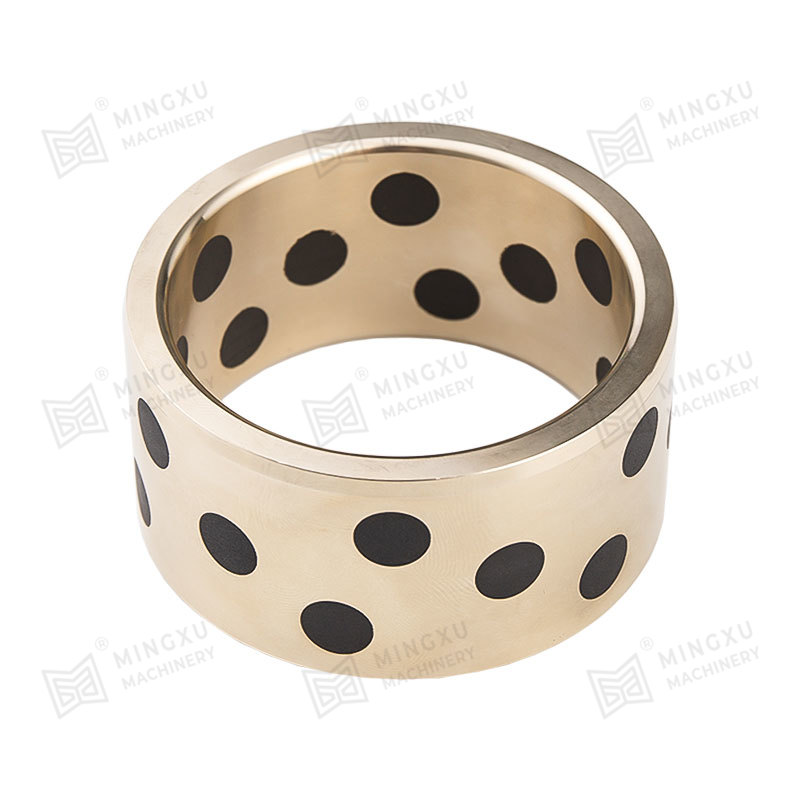
Grinding:Grinding uses abrasive wheels to remove material and achieve precise dimensions and surface finish.Grinding is used for finishing operations to achieve tight tolerances and smooth surface texture on graphite sliding bearings.Excellent precision, surface finish, and dimensional control.Graphite is abrasive and can cause rapid wear on grinding tools, necessitating frequent tool changes and proper dust control.
Drilling:Drilling creates round holes in a workpiece using rotary cutting tools.Drilling is used to create holes for mounting or assembly purposes in graphite sliding bearings.ast and efficient for creating simple holes with accurate dimensions.Graphite dust management is crucial to prevent contamination and maintain machining accuracy.
Electrical Discharge Machining (EDM):EDM uses electrical discharges to erode material from a workpiece, producing intricate shapes with high precision.EDM is used for intricate features or profiles on graphite sliding bearings where conventional machining methods are impractical.Capable of producing complex shapes with high precision and without mechanical force.EDM is slower than traditional machining methods and may require multiple passes for achieving desired dimensions.
These machining processes can be used individually or in combination to achieve the required tolerances and surface finishes for graphite sliding bearings, depending on the specific requirements of the application and the capabilities of the machining equipment available. Proper tool selection, machining parameters, and process control are essential for achieving consistent quality and dimensional accuracy in graphite bearing production.
Contact Us