Solid-lubricating bearings are essential components in various mechanical systems, offering unique advantages such as reduced friction and enhanced durability. However, their performance and load distribution are heavily influenced by their design and geometry. Understanding these factors can lead to improved efficiency and longevity in applications ranging from automotive to industrial machinery.
Bearing Shape and Functionality
The shape of a solid-lubricating bearing fundamentally affects its ability to support different types of loads. Radial bearings, designed to handle loads perpendicular to the shaft, and thrust bearings, which manage axial loads, are tailored for specific applications. Each design optimizes load distribution across the bearing surface, minimizing localized stress that could lead to premature wear or failure.
Surface Area and Contact Geometry
The surface area of a bearing plays a critical role in its load-bearing capacity. A larger surface area allows the bearing to distribute weight more evenly, supporting heavier loads without excessive wear. Additionally, the geometry of the contact surfaces—such as curvature and finish—significantly impacts friction levels. Smooth surfaces are crucial for reducing friction, while thoughtfully optimized geometries enhance load-carrying efficiency, ensuring reliable operation even under stress.
Clearance and Fit
Clearance between the bearing and shaft is another vital design consideration. Adequate clearance facilitates the distribution of solid lubricants and promotes effective heat dissipation, both of which are essential for reducing wear. Conversely, an interference fit can enhance load distribution, ensuring consistent contact between the bearing and shaft during operation, which is critical for maintaining performance.
Material Distribution and Thickness
The distribution of materials within a solid-lubricating bearing also influences its performance. Variations in thickness can impact both strength and flexibility; thicker sections may be better suited for handling higher loads, while thinner areas can allow for increased flexibility. In composite bearings, the arrangement and thickness of different layers can enhance wear resistance and lubrication, improving overall functionality.
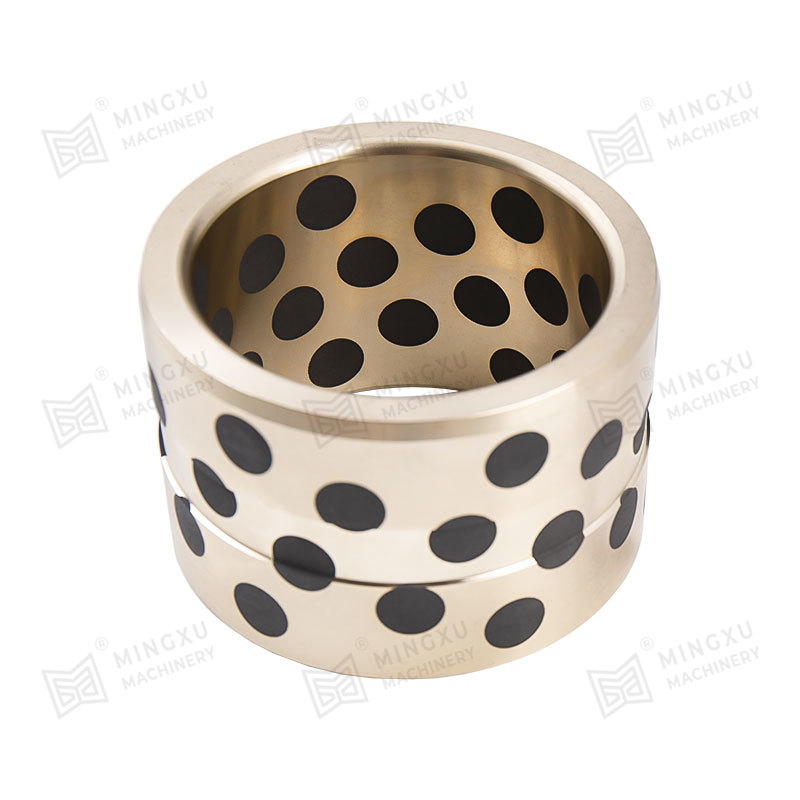
Cooling Features
Effective cooling mechanisms are essential for maintaining the integrity of solid-lubricating bearings. Some designs incorporate features such as channels or fins to promote heat dissipation, reducing thermal stress during operation. This not only enhances performance but also extends the lifespan of the bearing, making it suitable for more demanding applications.
Load Path Alignment and Dynamic Considerations
The alignment of the bearing concerning the load path is crucial. Proper alignment minimizes misalignment-induced stress, which can lead to increased wear. Additionally, bearings designed to accommodate dynamic loads must consider variations in force during operation. Custom geometries that account for these dynamics can optimize performance, ensuring that the bearing operates efficiently under varying conditions.
Specialized Designs
Innovative designs, including profiled bearings with grooves or patterns, enhance lubricant retention and further reduce friction. Custom geometries tailored to specific applications can significantly improve the bearing’s performance, making them invaluable in specialized fields.
The design and geometry of solid-lubricating bearings play a pivotal role in their overall performance and load distribution. Factors such as shape, surface area, clearance, and material distribution all contribute to the efficiency and reliability of these bearings. By optimizing these design elements, manufacturers can create solid-lubricating bearings that not only excel in performance but also enhance the durability and longevity of mechanical systems across various industries. Understanding these dynamics is key to advancing the effectiveness of solid-lubricating bearings in the modern world.
Contact Us