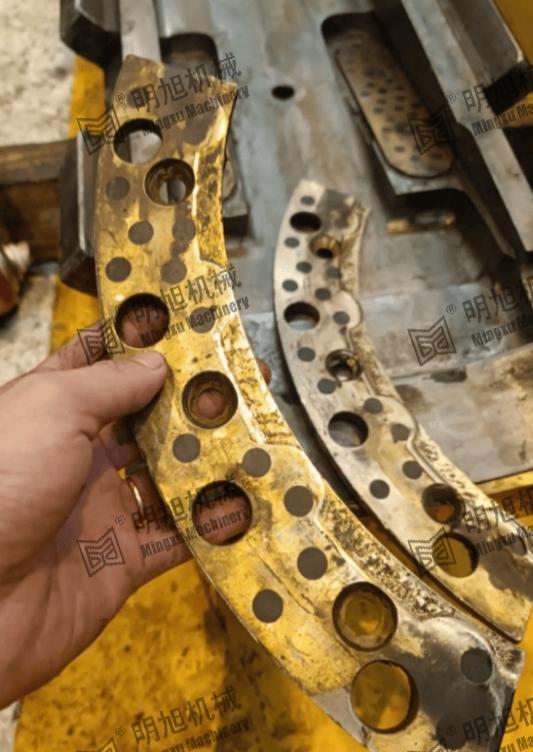
Zhejiang Mingxu Machinery Manufacturing Co., Ltd. has been engaged in the research and development and production of copper alloy parts and self-lubricating bearings for more than ten years, and has rich production experience and technical accumulation. In the process of customer feedback, we learned that copper-based self-lubricating products are prone to lubrication failure when encountering friction and wear, high temperature, load, material aging, arc erosion, and chemical reactions. For reference, we hope that you will purchase self-lubricating products suitable for your working conditions during use, make advance predictions, and effectively avoid production risks:
- Friction and wear: During mechanical movement, the solid lubricating film at the friction contact interface is constantly consumed and worn. If the formation rate of the lubricating film cannot keep up with the wear rate, it will cause lubrication failure, thereby aggravating wear. For example, in self-lubricating spherical bearings, the relative sliding of the liner and the inner and outer rings will cause failure forms such as liner shedding, tearing or extrusion, resulting in the bearing not being able to work properly.
- High temperature effect: The increase in temperature will reduce the adhesion of grease and make it easy to lose, while increasing evaporation loss and oxidation rate, further deteriorating the lubrication effect. In addition, the wear rate of some materials such as tin bronze-based self-lubricating composite materials at high temperatures (such as 450°C) is not reduced by the addition of solid lubricants. Instead, the friction factor may increase rapidly due to the reduction of sulfide solid lubricants.
- Load influence: Under high load conditions, the solid lubricant in the self-lubricating layer will be continuously squeezed out, resulting in a decrease in the self-lubricating function and ultimately causing wear and cracking of the material. For example, the self-lubricating spherical bearing of PTFE copper mesh composite material will have varying degrees of cracks and liner shedding under large loads.
- Material aging: With the extension of time, the lubricating material may age, manifested as hardening, softening, cracking or leakage, which will lead to a decrease in lubrication ability and cause equipment failure.
- Arc ablation: Under certain specific conditions, such as the application of surface textured nanocomposites, the relatively small number of texture grooves cannot effectively store lubricants, and a uniform lubricating film cannot be formed on the sliding contact surface, resulting in direct contact between the pair and the substrate, destroying the texture stripes, which is the main reason for the failure of the coating.
- Chemical reaction: Metal elements (such as copper) have a catalytic effect on lubricating oil, especially in the presence of water, which will cause the lubricating oil to oxidize and deteriorate, further affecting the lubrication effect.
If you have any product and technical questions, please feel free to contact us: [email protected].
Contact Us