Self-lubricating bearings are widely used in the aerospace field, mainly due to their characteristics of self-lubricating and reducing friction loss without the need for manual lubrication.
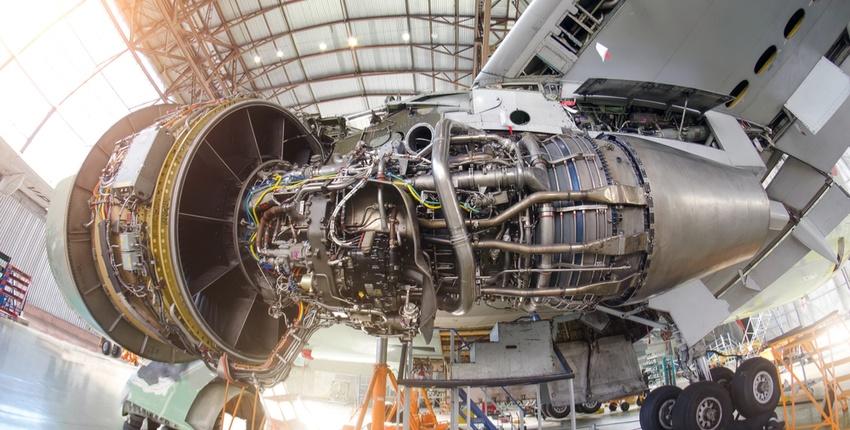
Advantages of self-lubricating bearings in the aerospace field
- No need for additional lubrication: Self-lubricating bearings use special materials and can automatically form a lubricating film, without the need for manual lubrication, which reduces maintenance costs.
- Adapt to extreme environments: They can operate stably in environments from -200°C to high temperatures, meeting the adaptability requirements of aerospace equipment to extreme temperatures.
- Improve reliability: Self-lubricating bearings reduce failures caused by insufficient or excessive lubricants, improve the overall reliability of equipment, and are crucial to the aerospace field.
- Reduce maintenance costs: Due to the self-lubricating performance, the consumption of lubricants and related maintenance work is reduced, reducing the long-term use cost.
- Lightweight design: It meets the strict weight requirements of aerospace equipment and helps improve overall performance.
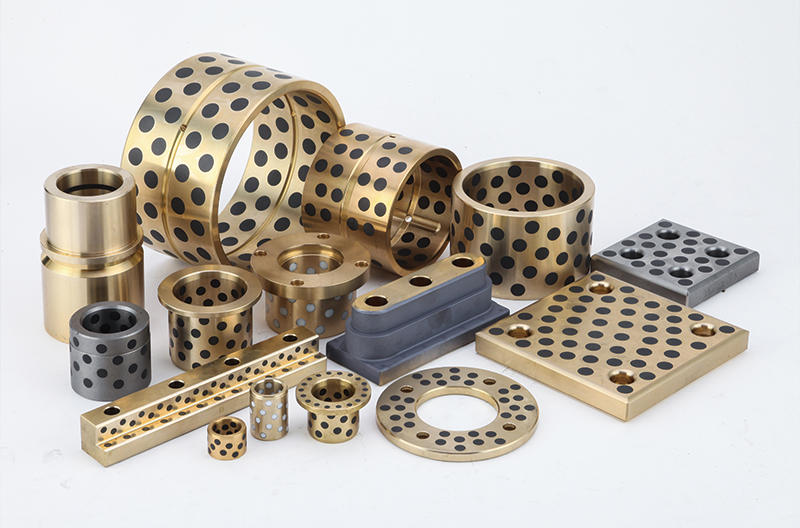
Application Areas:
- Aircraft Key Parts: Self-lubricating bearings are widely used in aircraft wing systems (such as flaps, spoilers and slats), flight controls, cockpit controls, auxiliary power units, landing gear and door systems, ensuring the smooth operation and long-term reliability of these key parts.
- Aircraft Interior Applications: Self-lubricating bearings are also often used in aircraft interiors, such as seats, storage boxes, latches and hinge points, to provide stable support and lubrication effects, improving passenger comfort and safety.
Extreme Environment Performance: In extreme temperature environments such as Mars rovers, self-lubricating bearings also show their unique advantages, and can operate stably at temperatures from -200°C to +280°C, providing reliable support for extreme environment applications of aerospace equipment.
Material Type: There are mainly two types: metal polymer and fiber reinforced composite.
Metal polymer self-lubricating bearings consist of an external metal backing, a porous bronze internal structure and a polymer resin lining; fiber reinforced composite bearings are supported by self-lubricating linings and high-strength glass fibers. In particular, metal polymer self-lubricating bearings are used in aircraft wings and seats. They combine the strength of metals and the lubricity of polymers, making them very suitable for the needs of the aerospace field.
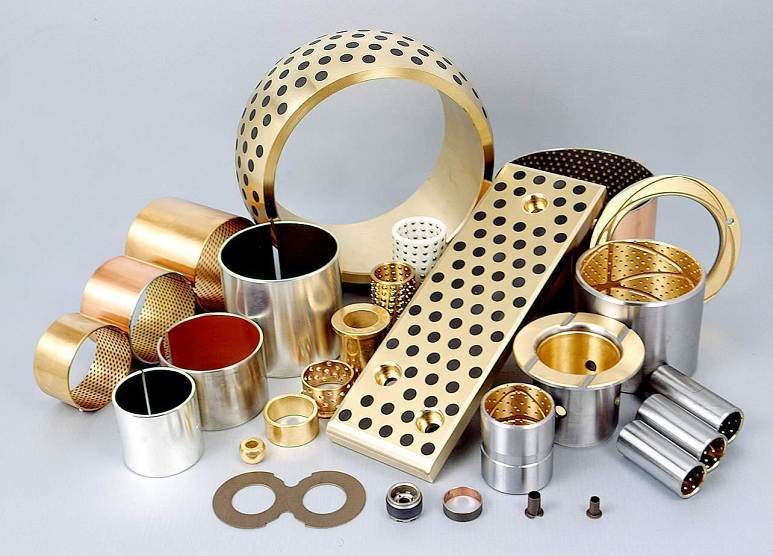
Special requirements for self-lubricating bearings in the aerospace field mainly include the following:
- High reliability and high precision: Bearings must withstand harsh working conditions such as high temperature, high load, high speed, and strong vibration. Failure of any component may lead to catastrophic consequences. At the same time, extremely high precision is required to ensure equipment performance.
- High temperature and high speed performance: Bearings must be able to operate stably in high temperature and high speed environments without performance degradation or damage.
- Long life and low noise: Bearings are required to have a long life to reduce maintenance costs, and low noise to avoid affecting equipment performance.
- Lightweight and corrosion resistance: Bearings must be lightweight to meet the strict weight requirements of aerospace equipment, and must be corrosion-resistant to prevent rust and damage.
- Excellent lubrication performance: When lubricants cannot be added manually, bearings must have self-lubricating capabilities to ensure long-term stable operation.
Contact Us