Linear motion ball bearings are widely used in various industrial applications, but their performance can be significantly affected by extreme temperatures, whether high or low. The materials and coatings used in the construction of these bearings play a crucial role in ensuring their reliability and longevity under such conditions. Here’s how linear motion ball bearings perform in both high and low temperatures, and which materials or coatings are most suitable for each environment:
1. Performance in High Temperatures:
High temperatures can cause various issues in linear motion ball bearings, such as increased friction, wear, and lubricant breakdown. Materials and designs that offer thermal stability and heat resistance are essential for maintaining the bearing’s performance in these environments.
Challenges at High Temperatures:
Thermal Expansion: As the temperature increases, materials expand. This can lead to misalignment or increased friction in the bearing, affecting its performance.
Lubricant Breakdown: At high temperatures, lubricants such as oil or grease can degrade or evaporate, leading to insufficient lubrication and increased friction and wear.
Material Degradation: Some materials, such as steel, may lose their hardness or strength at elevated temperatures, causing deformation or reduced load capacity.
Suitable Materials and Coatings for High Temperatures:
Ceramic Balls (e.g., Silicon Nitride): Ceramic balls are highly resistant to high temperatures (up to 1000°C or more) and offer superior wear resistance. They also have low thermal expansion, making them ideal for high-speed and high-temperature applications.
Advantages: Ceramic materials are excellent at maintaining their mechanical properties and hardness even at elevated temperatures.
Applications: Used in aerospace, high-performance motors, and CNC machines operating at elevated temperatures.
Stainless Steel Raceways: Stainless steel, particularly AISI 440C or AISI 316, can withstand high temperatures (up to 300°C) without significant degradation. It is also corrosion-resistant, making it suitable for high-temperature environments with exposure to moisture or chemicals.
Advantages: Stainless steel offers corrosion resistance and maintains its strength at higher temperatures better than regular steel.
High-Temperature Lubricants: Specialized high-temperature lubricants (e.g., synthetic oils, graphite-based lubricants) are used to ensure proper lubrication at elevated temperatures. These lubricants can withstand higher temperatures without breaking down, reducing friction and wear.
Advantages: These lubricants provide better heat resistance and maintain a thin film between bearing components, reducing the risk of direct contact between surfaces.
Coatings: Coatings such as Nickel-plating, Hard Chrome, or PTFE coatings can provide extra protection against corrosion and wear, helping maintain the bearing’s functionality at high temperatures.
Advantages: Coatings help to improve wear resistance, lubricant retention, and corrosion resistance under heat stress.
Applications in High-Temperature Environments:
Aerospace: Components subjected to high-speed and high-temperature conditions.
Turbines and engines: Where components are exposed to high heat.
Automotive: In high-performance vehicles where bearings are exposed to high temperatures during operation.
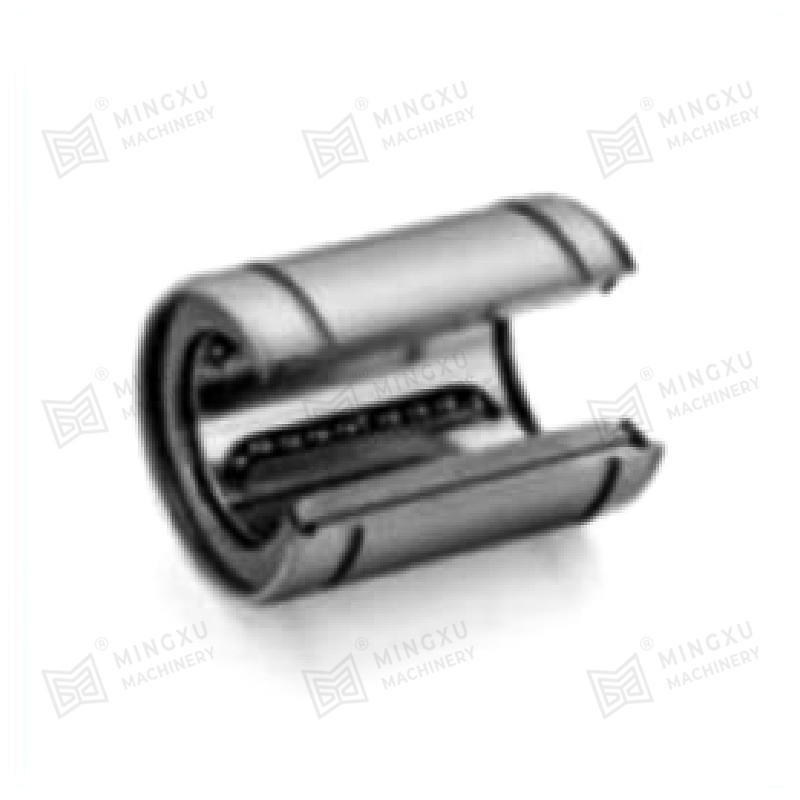
2. Performance in Low Temperatures:
At low temperatures, linear motion ball bearings face challenges like increased friction, reduced lubricant efficiency, and potential brittleness in materials. Materials and bearing designs that resist freezing and shrinkage are critical for maintaining performance in cold environments.
Challenges at Low Temperatures:
Increased Friction: Low temperatures can cause the bearing lubricant to become viscous, resulting in increased friction and resistance to motion. The bearing may become stiff, leading to increased wear and heat buildup.
Lubricant Thickening: Many lubricants, including greases and oils, become thicker and less effective at low temperatures. This can prevent proper lubrication, resulting in metal-to-metal contact and bearing failure.
Material Brittle Failure: Some materials become brittle at low temperatures, which can lead to cracks, fractures, or the deformation of bearing components.
Contraction: Materials contract in the cold, potentially causing the bearing to shrink or misalign, which can interfere with smooth motion.
Suitable Materials and Coatings for Low Temperatures:
Ceramic Balls (e.g., Silicon Nitride): Ceramic bearings perform well in low-temperature environments. Unlike metals, ceramics do not become brittle in extreme cold. They maintain their hardness and wear resistance at low temperatures, ensuring smooth and reliable performance.
Advantages: Ceramics do not experience thermal expansion or contraction issues and retain their structural integrity even at extremely low temperatures (down to -200°C or lower).
Applications: Used in cryogenic systems, space applications, and refrigeration systems.
Stainless Steel (Martensitic Grades): Martensitic stainless steels (e.g., AISI 440C) have good low-temperature toughness and perform better than austenitic steels in cold environments. They maintain their strength without becoming brittle and have relatively low thermal expansion.
Advantages: Stainless steel retains its strength and impact resistance at low temperatures better than many other metals.
Low-Temperature Lubricants: Synthetic oils or fluorinated oils designed for low-temperature environments are used to prevent the bearing from freezing or becoming stiff. These lubricants remain effective in temperatures as low as -100°C.
Advantages: They maintain a low viscosity at low temperatures, ensuring the bearing remains lubricated even under freezing conditions.
Applications: Used in refrigeration systems, cryogenic equipment, and polar operations.
Polymer Bearings: Plastic or polymer bearings, such as those made from PEEK (Polyetheretherketone) or PTFE (Polytetrafluoroethylene), are suitable for low-temperature environments because they are naturally resistant to freezing and do not become brittle like metals.
Advantages: Polymer bearings maintain their flexibility and resilience at very low temperatures, making them suitable for use in cryogenic systems and low-temperature manufacturing processes.
Coatings: Special coatings such as PTFE (Teflon) or perfluoropolyether lubricants can help reduce friction in cold environments by providing a slippery surface that minimizes wear and ensures smooth movement even when the lubricant is thickened due to the cold.
Advantages: Coatings help reduce friction and wear while providing an additional layer of protection against moisture and contaminants in cold environments.
Applications in Low-Temperature Environments:
Cryogenics: Systems operating in extremely low temperatures, such as liquefied natural gas (LNG) plants, cryogenic storage, or space exploration.
Cold Storage: Refrigeration systems and freezer units.
Arctic and Antarctic Operations: Machinery used in polar regions or in exploration.
Contact Us