DU bearing is a sliding bearing rolled with a steel plate as the base, sintered spherical bronze powder in the middle, and a mixture of polytetrafluoroethylene (PTFE) and additives rolled on the surface. It is suitable for working parts that cannot be refueled or are difficult to refuel, and has a variety of excellent features.
The friction layer of the DU bearing is a mixture of PTFE and fiber with a thickness of 0.01~0.03mm. This mixture can form a good transfer film to protect the dual parts and provide the bearing with self-lubricating properties. The copper powder layer in the middle, with a thickness between 0.20~0.35mm, not only has good load-bearing capacity and wear resistance, but its good thermal conductivity can also timely transfer the heat generated during the operation of the bearing. In addition, the composite material penetrates into the pores of the spherical copper powder, further improving the bonding strength.
In practical applications, DU bearings show the advantages of good wear resistance, low friction factor, good running-in performance, low noise, no pollution, and good corrosion resistance. The transfer film formed during operation can protect the grinding shaft and avoid shaft seizure. At the same time, the processing requirements for the paired parts are also reduced, thereby reducing the user's processing costs.
DU bearings are widely used in general industrial fields, especially where high wear resistance and self-lubricating properties are required. Please note that although DU bearings have many advantages, in specific applications, it is still necessary to select the appropriate model and specification according to the actual working environment and conditions, and follow the correct installation and use methods to ensure its performance and life.
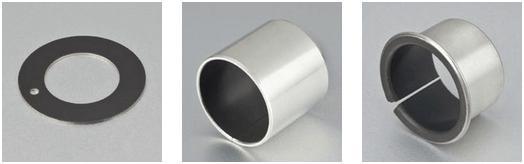
As a special sliding bearing, DU bearings have a series of significant advantages, but there are also some possible disadvantages. The following is a detailed analysis of the advantages and disadvantages of DU bearings:
advantage:
Self-lubricating properties: DU bearings are
self-lubricating bearings with excellent self-lubricating properties and can operate without external lubrication. This feature makes DU bearings particularly suitable for working areas where oiling is impossible or difficult.
Good wear resistance: DU bearings are made of special materials, which have low friction coefficient and excellent wear resistance. This helps extend the service life of the bearings and reduces downtime due to wear.
Strong corrosion resistance: DU bearings have high resistance to corrosive media and can work in various corrosive environments, thus expanding their application scope.
Similar static and dynamic friction coefficients: This feature helps eliminate crawling at low speeds and ensures the working accuracy and stability of the machinery.
Low noise: DU bearings produce lower noise during operation, which helps improve the working environment and reduce noise pollution.
Low processing requirements: The processing accuracy requirements for the paired parts are relatively low, which helps reduce the user's processing costs.
shortcoming:
Limitations on applicable scenarios: Although DU bearings have many advantages, their applicable scenarios still have certain limitations. Under certain extreme working conditions, such as high temperature, high pressure or high-speed operation, the performance of DU bearings may be affected to a certain extent.
Higher price: Because DU bearings use special materials and manufacturing processes, their prices are relatively high. This may increase the overall cost of the device and may be a consideration for some users on a budget.
Maintenance requirements: Although DU bearings have self-lubricating properties, they still require proper maintenance during long-term use. If worn parts are not cleaned and replaced in time, the performance and life of the bearing may be affected.
Contact Us