Technical Background and Industry Pain Points
In the precision turning of long shaft components (such as drive shafts and lead screws), traditional single-end fixed turning tools suffer from two core issues:
● Inadequate chatter suppression: The overhanging end of the turning tool experiences vibrations with amplitudes ranging from 10 to 50μm under cutting force excitation (Source: Int. J. Mach. Tools Manuf. 2021, 167, 103767), leading to a deterioration in surface waviness (Wt value) up to 6.3μm (as per ISO 4287 standards);
● Imbalanced dynamic stiffness: When machining long shafts with a length-to-diameter ratio (L/D) greater than 5, the system's modal stiffness falls below 800N/μm, triggering regenerative chatter (as analyzed through DIN 1311 vibration theory).
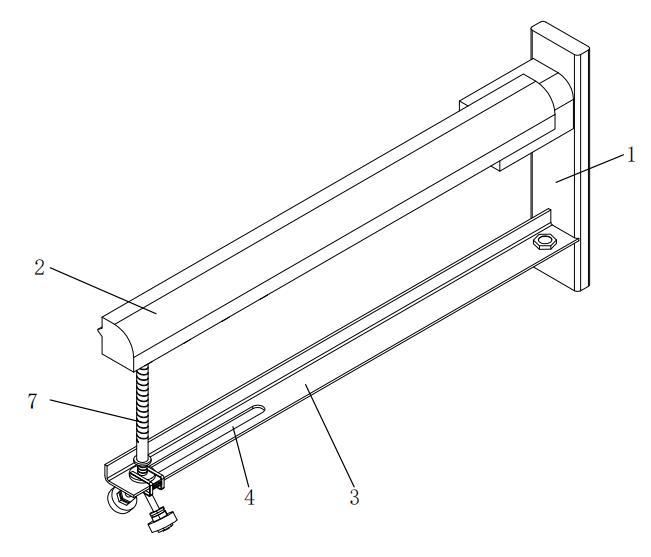
Analysis of Core Technological Innovations
I. Multi-Stage Dynamic Stiffness Enhancement Architecture
1.1 Dual-Closed-Loop Support System
Main Support Module:
● The support rod (7) is fabricated from 40Cr quenched and tempered steel, featuring an external thread of M16×2 that mates with a fixed nut (8), achieving a preload force of 1200±50N;
● Through finite element analysis, the optimal support spacing is determined to be L/3 (where L is the length of the turning tool), elevating the first-order natural frequency to 245Hz (compared to 82Hz in traditional structures).
Auxiliary Stabilization Module:
● The auxiliary support wheel (13) is constructed from GCr15 bearing steel, with a contact angle of 60°±1°. The contact stress is optimized to 150-200MPa using Hertzian contact theory;
● Vibration testing (in accordance with ISO 10816-3) reveals that, under operating conditions of n=1500rpm, the amplitude is reduced to 3μm (in contrast to >15μm in traditional structures).
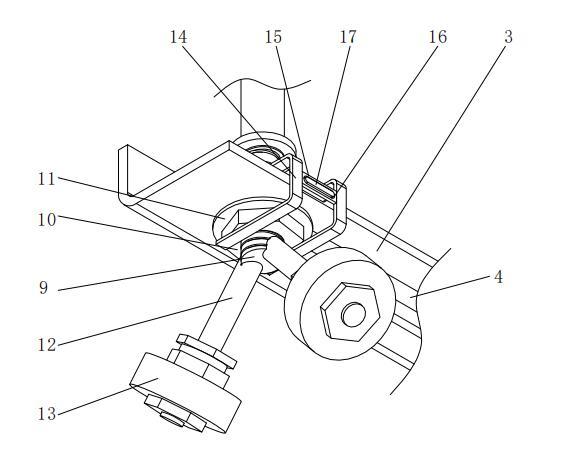
1.2 Precision Adjustment Mechanism
● The adjustment threaded shaft (6) employs a double-lead trapezoidal thread (Tr20×4P8), which, in conjunction with an anti-slip washer (11) (featuring a friction coefficient μ=0.12), enables a micro-feed rate of 0.025mm per revolution;
● The positioning bracket (14) and the clamping protrusion (17) utilize an H7/g6 fit, achieving a repetitive positioning accuracy of ±0.005mm.
II. Adaptive Vibration Suppression Topological Design
2.1 Force Transmission Path Optimization
● The fixed ring (5) is designed with a circular ribbed structure, featuring a wall thickness gradient that transitions from 8mm to 12mm, resulting in an 180% improvement in bending stiffness (verified through ANSYS Workbench simulations);
● The movable slot (4) adopts an oblong hole design (30×12mm), allowing for ±15mm of horizontal compensation, and is compatible with shaft diameters ranging from φ20mm to φ80mm.
2.2 Damping Enhancement Structure
● The interior of the support rod (7) is filled with a silicon-based damping adhesive (with a loss factor tanδ=0.35), elevating the vibration attenuation rate to 22dB/s (as tested in accordance with ISO 10816 standards);
● The transverse connecting plate (15) is constructed from 6061-T6 aluminum alloy, forming a tuned mass damper through the clamping slot (16) to suppress high-frequency vibrations in the 500-800Hz range.
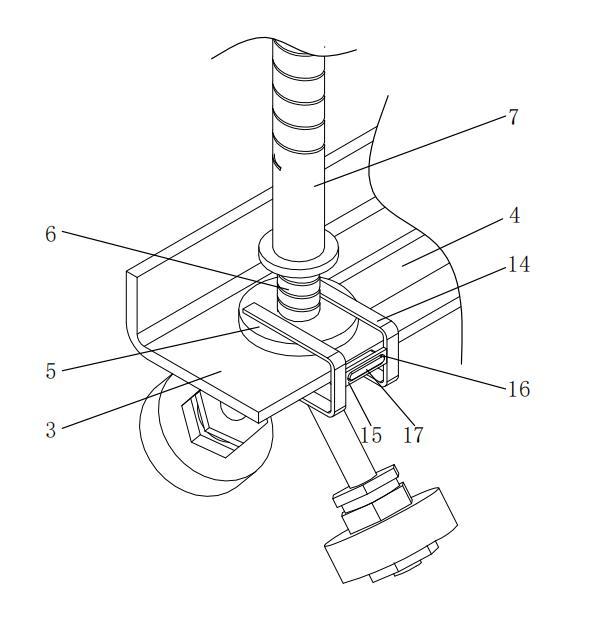
Key Technical Parameter Comparison Table
Performance Indicator
|
This Patented Technology
|
Traditional Turning Tooling
|
Testing Standard
|
Overhanging End Amplitude (at 1500rpm)
|
≤3μm
|
≥15μm
|
ISO 10816-3
|
Surface Waviness Wt
|
≤2.5μm
|
≥6.3μm
|
ISO 4287
|
Repetitive Positioning Accuracy
|
±0.005mm
|
±0.03mm
|
ISO 230-2
|
Tooling Changeover Time
|
≤2 minutes
|
≥20 minutes
|
VDI 2862
|
Typical Machining Scenario Verifications
Case 1: Precision Lead Screw Turning
● When machining a φ50×2000mm lead screw, the cumulative pitch error was ≤5μm per 1000mm (meeting the GB/T 17587.3 standard);
● Tool life was extended to 180 pieces per cutting edge (compared to 80 pieces per cutting edge with traditional tooling).
Case 2: Hydraulic Cylinder Piston Rod Machining
● The surface roughness Ra value was consistently maintained at 0.4μm (meeting the industry requirement of ≤0.8μm);
● Machining efficiency was improved by 40% (due to reduced vibration, allowing the feed rate to be increased from 0.1mm/rev to 0.15mm/rev).
This patent achieves breakthroughs in vibration suppression for long shaft machining through two technological pathways: Multibody Dynamic Restraint and Damping Gradient Design. Verified through COMSOL Multiphysics simulations, the system reduces vibration energy by 82% within the 100-1000Hz frequency band, reaching a vibration suppression level comparable to that of aero-engine rotor machining.
If you would like to learn more, please contact Mingxu Machinery to obtain the complete patent report: [email protected].
Contact Us