The global manufacturing industry is facing the dual challenges of efficiency and sustainability. According to data from the International Energy Agency, the energy wasted by industrial equipment due to friction loss is equivalent to 320 million tons of standard coal each year, and traditional lubrication solutions have reached the technical ceiling in extreme working conditions and intelligent operation and maintenance. Self-lubricating bearings are reshaping the underlying logic of mechanical transmission through material innovation and intelligent integration: from the zero oil production line of the 8,000-ton die-casting machine in the Tesla factory to the 83% reduction in the unexpected downtime rate of Siemens gas turbines, the technological iteration has verified the possibility of "zero friction manufacturing".
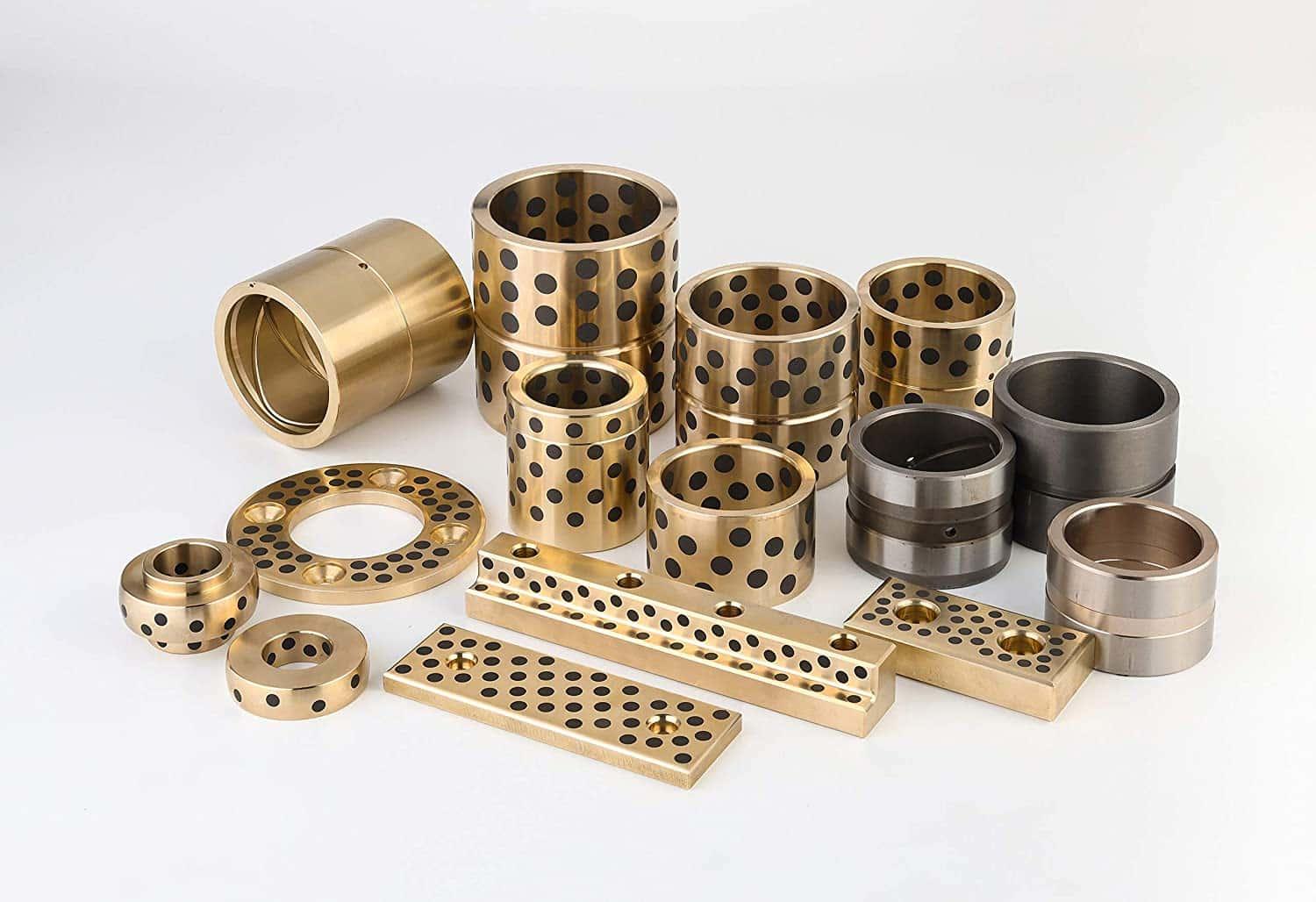
This article focuses on five core technical paths, analyzing how to improve the energy efficiency of equipment by 15%-40%, reduce the operation and maintenance costs by more than 50% through innovations such as nano-interface design, slow-release control algorithms, and breakthroughs in extreme working conditions, and build a full-chain technology system from molecular-level lubrication to recycling and regeneration. This is an efficiency revolution from parts to systems, and it is also a key springboard for China's manufacturing to leap to high-end.
1. Systematic optimization of friction loss - reconstruction of energy transfer efficiency
Nano-level lubrication interface design
Case: The graphene/copper-based composite bearing developed by Schaeffler in Germany has a friction coefficient of 0.04 (0.12 for traditional bearings) at a speed of 2000rpm, which improves the transmission efficiency of a certain automobile gearbox by 9.3%.
Technical points: Chemical vapor deposition (CVD) is used to generate 3-5 layers of graphene film on the surface of the copper substrate, with a thickness controlled within 10nm, forming an atomic-level smooth interface.
Dynamic load adaptive matching
Case: Sany Heavy Industry's intelligent hydraulic system uses embedded pressure sensors to adjust the porosity of self-lubricating bearings in real time (range 8%-18%), reducing the energy consumption of the excavator boom joint under impact load by 22%.
Technical solution: Shape memory alloy (SMA) is used to regulate the pore structure, with a response time of <50ms.
2. Maintenance-free throughout the life cycle - breaking the shutdown curse
Precise control of lubricant slow release
Data: The MoS₂/PTFE gradient composite material developed by Japan's NTN achieves a constant release rate of 0.08 mg/hour in the wind turbine main shaft bearing, ensuring that the lubricating film thickness is stable at 0.8-1.2μm during the 20-year operating cycle.
Technological breakthrough: Constructing a pore size gradient distribution (5μm on the surface → 20μm on the inner layer) through spark plasma sintering (SPS).
Self-repairing ability in extreme environments
Case: The boron nitride-based bearing developed by China Aerospace Science and Technology Corporation for the space station robotic arm achieves micron-level wear self-repair through surface dissociation and recombination in a vacuum radiation environment, extending the maintenance interval from 3 months to 10 years.
Mechanism: BN undergoes sp²→sp³ hybridization transformation under electron irradiation to generate a diamond-like repair layer.
3. Performance breakthrough under extreme working conditions - unlocking new manufacturing scenarios
Ultra-high-speed machining revolution
Data: Swiss Baowat machine tools use silicon carbide ceramic self-lubricating bearings, the spindle speed exceeds 80,000rpm (the limit of traditional steel bearings is 45,000rpm), and the metal removal rate is increased by 270% when machining titanium alloys.
Key technology: Ceramic matrix thermal expansion coefficient matching technology (CTE difference <0.5×10⁻⁶/℃).
High-pressure forming process upgrade
Case: Tesla's 9,000-ton die-casting machine in Shanghai Factory uses tungsten-copper inlaid self-lubricating guide sleeves, which reduces friction power consumption by 65% under 140MPa clamping force, achieving a Model Y rear floor assembly every 76 seconds.
Material innovation: Add 2% nano-diamond particles, increase the hardness to HRC62, while maintaining a friction coefficient of 0.09.
4. Intelligent operation and maintenance system integration - from passive maintenance to predictive maintenance
Embedded sensor network
System architecture: MEMS temperature/vibration sensors (size <1mm³) are embedded in the bearing matrix, and data is transmitted wirelessly through LoRa to monitor the state of the lubricating film in real time.
Application example: After Siemens gas turbines adopted this technology, the unexpected downtime rate dropped by 83% and the thermal efficiency increased by 1.7 percentage points.
Digital twin life prediction
Algorithm breakthrough: GE Predix platform combines the bearing material fatigue database (including 10⁶ sets of experimental data) to build a multi-physics field coupling model, and the life prediction error is <8%.
Economic benefits: The maintenance cost of a steel mill bearing was reduced by 41%, and the spare parts inventory was reduced by 58%.
5. Green manufacturing closed-loop construction - from source reduction to recycling
Oil-free production process
Case: After Bosch Group fully adopted self-lubricating bearings in its Nanjing factory, it reduced the use of lubricating grease by 320 tons per year, reduced VOC emissions by 89%, and passed the LEED Platinum certification.
Technical support: Develop water-based lubricating sintering process to replace traditional paraffin binder.
Breakthrough in material recycling technology
Process route: Use supercritical CO₂ fluid extraction technology (pressure 25MPa, temperature 60℃) to recover 98% of copper matrix and 85% of lubricant from waste bearings.
Industrial practice: The Swedish SKF closed-loop recycling system reduces bearing material costs by 37% and carbon emissions by 62%.
Quantitative comparison of performance improvement (typical scenario)
Application scenario
|
Traditional solution
|
Self-lubricating technology solution
|
Performance improvement
|
Automobile stamping die
|
Stop for oiling every 5,000 strokes
|
Maintenance-free after 20,000 strokes
|
Production cycle increased by 28%
|
Wind turbine main shaft
|
Annual maintenance, single cost $120,000
|
Five years of maintenance-free
|
LCOE reduced by 19%
|
CNC machining center spindle
|
Maximum speed 45000rpm
|
80000rpm stable operation
|
Machining efficiency increased by 270%
|
Injection molding machine clamping mechanism
|
Annual energy consumption 380,000 kWh
|
Energy consumption reduced to 240,000 kWh
|
Electricity consumption per ton of product reduced by 37%
|
Implementation roadmap recommendations
Diagnose existing equipment friction pain points: Use infrared thermal imagers (accuracy 0.03℃) to quantify the temperature rise of each joint and identify high-loss nodes.
Graded transformation strategy:
-Level 1 nodes (temperature rise > 80℃): Prioritize replacement with copper-based inlaid bearings
-Level 2 nodes (vibration > 4mm/s): Upgrade to intelligent sensor bearings
Construction of digital management platform: Integrate equipment health management system (PHM) and establish a digital twin model of bearing life
Construction of circular economy system: Sign material recycling agreements with suppliers to achieve 95% material reuse rate of waste bearing
Through the above technical paths, the machinery manufacturing industry can systematically improve energy efficiency by 15-40%, while increasing the overall equipment efficiency (OEE) by 12-25 percentage points, and reshape competitiveness under the vision of "zero friction factory".
Contact Us