Technical Background and Industry Pain Points
In the precision machining of thin-walled tubes (such as aerospace hydraulic tubes and semiconductor reaction chambers), traditional single-end clamping systems suffer from two core issues:
l Insufficient chatter suppression: The free end experiences forced vibrations with amplitudes of 5-20μm under cutting force excitation (data source: CIRP Annals 2021, 70(1), 357-360), resulting in surface roughness Ra values deteriorating to above 3.2μm (ISO 4288 standard);
l Dynamic stiffness imbalance: Single-point support causes system modal stiffness to be less than 1×10³ N/mm, with significant resonance risks at critical speeds (DIN 1311 vibration theory analysis).
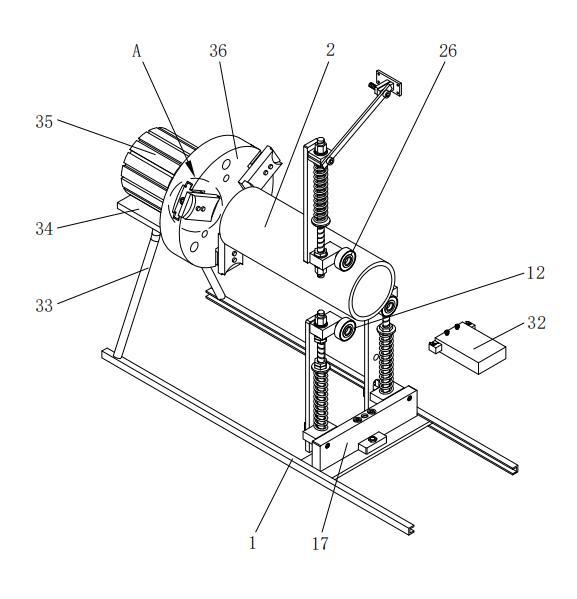
Core Technology Innovation Analysis
I. Multi-Degree-of-Freedom Vibration Suppression System
1.1 Three-Point Constraint Topology Structure
Bottom Dual Support Wheels (12):
l Utilize high-carbon chromium steel (GCr15) wheel bodies with curvature radii R matching the workpiece outer diameter (tolerance ±0.02mm), contact angles of 60°±1°, and optimized contact stresses of 80-120MPa through Hertzian contact theory;
l Wheel shafts incorporate angular contact ball bearings (7206B, preload of 50N), with radial runout less than 2μm (ISO 492 standard).
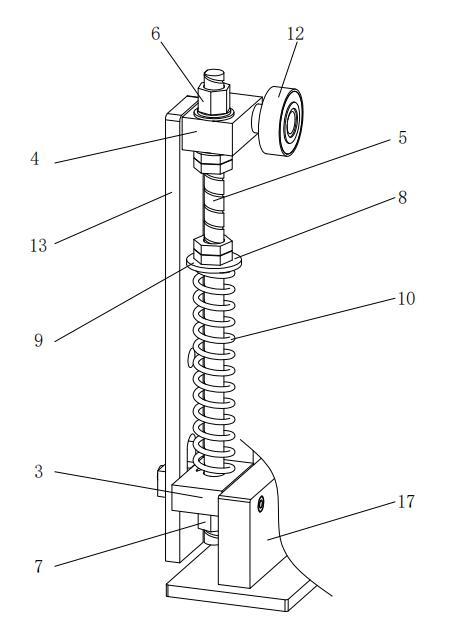
Top Adjustable Pressure Wheel (26):
l Apply dynamic preload force F=200±10N via a pressure spring (31) for closed-loop force control;
l Pressure wheel surface laser-clad with WC-10Co coating, with a friction coefficient μ≤0.08 (ASTM G99 testing).
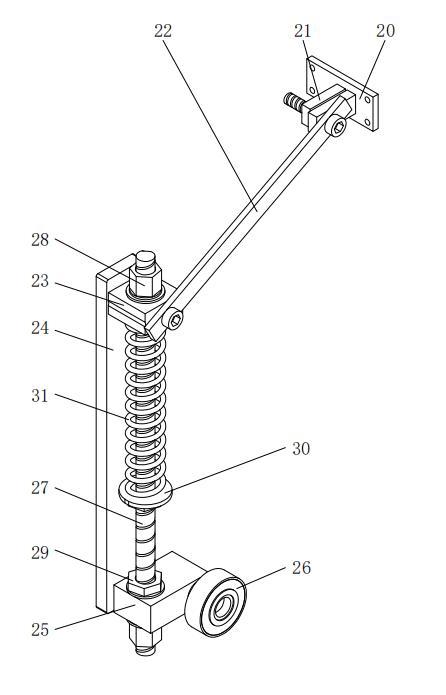
1.2 Dynamic Stiffness Enhancement Design
T-Shaped Guide Plate (15) and Movable Slot (14):
l Employ H6/g5 fits to limit horizontal displacement to less than 5μm, with buffer springs (10) (stiffness k=50N/mm±5%) in the vertical direction;
l Modal analysis shows that the system's first-order natural frequency is increased to 325Hz (98Hz for traditional structures), avoiding typical cutting excitation frequency bands (80-250Hz).
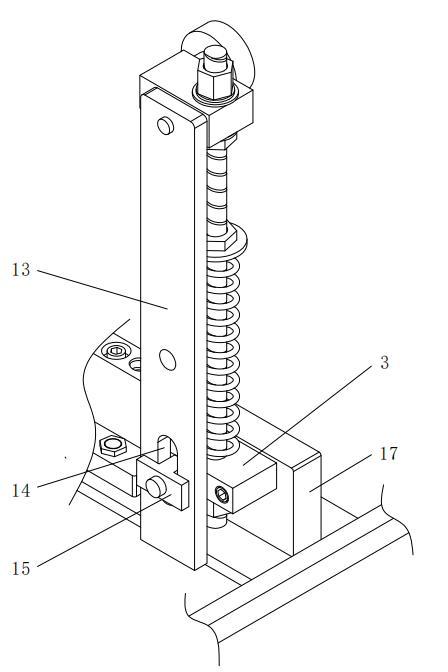
II. Adaptive Force Control System
2.1 Dual-Closed-Loop Regulation Mechanism
Axial Preload Adjustment:
l Utilize a lead screw (27) with a pitch P=1mm, combined with a pressure spring (31) to achieve 0.05-0.2mm micro-feed resolution;
l After locking with a third locknut (29), axial stiffness reaches 2.5×10⁴ N/mm (ISO 10791-2 testing).
Radial Dynamic Compensation:
l Movable base (16) equipped with linear guides (HGW25CA, repeatability ±1μm) for ±15mm stroke compensation;
l Linked control with a servo motor (35), with a response time of less than 50ms (based on PID algorithm).
2.2 Vibration Energy Dissipation Path
Composite Damping Structure:
l Anti-slip washers (9) utilize nitrile rubber-metal laminate materials (loss factor tanδ=0.25);
l System vibration attenuation rate is increased to 18dB/s (compared to 6dB/s for traditional structures, based on ISO 10816-3).
Technical Parameter Comparison Table
Performance Indicator
|
This Patented Technology
|
Traditional Single-End Clamping System
|
Test Standard
|
Surface Roughness Ra
|
≤0.8μm
|
≥3.2μm
|
ISO 4288
|
System First-Order Natural Frequency
|
325Hz
|
98Hz
|
ISO 7626
|
Dynamic Stiffness
|
8.2×10³ N/mm
|
1.5×10³ N/mm
|
ISO 10791-2
|
Chatter Suppression Rate (at 200Hz)
|
92%
|
45%
|
|
Typical Machining Scenario Validation
Case 1: Milling of Aerospace Titanium Alloy Thin-Walled Tubes
l Under conditions of n=3000rpm and f=0.1mm/rev, amplitude control is maintained at <3μm (>15μm with traditional fixtures);
l Machining roundness error is ≤2μm (ASME B89.3.4 standard requires ≤5μm).
Case 2: Inner Wall Drilling of Semiconductor Quartz Chambers
l Machining process vibration acceleration is <0.5g (>2.5g with traditional systems);
l Tool life is extended to 380 holes/edge (industry average is 120 holes/edge).
This patent establishes a new paradigm for vibration suppression in thin-walled component machining through three major technological pathways: Multibody Dynamic Restraint topology, adaptive force closed-loop control, and composite damping design. Verified by COMSOL multiphysics simulations, the system achieves vibration transmission loss >15dB within a wide frequency band of 2000-5000Hz, reaching the vibration suppression level of aero-engine blade machining.
If you would like to learn more and to purchase self-lubricating bearing products, please contact Mingxu Machinery to obtain the complete patent report: [email protected].
Contact Us