Composite materials offer several advantages over traditional metallic options when used for thrust washers. These advantages can significantly impact performance, durability, and overall system efficiency. Here’s a detailed look at the benefits:
1. Enhanced Wear Resistance
Composite Advantage: Composite thrust washers typically incorporate materials such as PTFE (polytetrafluoroethylene), graphite, or carbon fibers that are highly resistant to wear and abrasion. These materials provide excellent surface properties that reduce friction and wear, especially in dry or marginally lubricated conditions.
Traditional Metallic Limitation: Metal thrust washers, such as those made from bronze or steel, can experience higher rates of wear, especially under high-load conditions or in abrasive environments. They often require more frequent maintenance or replacement compared to composite materials.
2. Superior Friction Reduction
Composite Advantage: Many composites have self-lubricating properties that reduce the need for additional lubrication. Materials like PTFE in composite washers provide a low coefficient of friction, which minimizes energy loss and heat generation during operation. This leads to smoother operation and reduced wear on both the washer and the mating surfaces.
Traditional Metallic Limitation: Metallic washers typically require external lubrication to reduce friction. Without proper lubrication, metal washers can experience increased friction, leading to higher wear rates and potential heat buildup.
3. Corrosion Resistance
Composite Advantage: Composite materials are inherently resistant to corrosion and chemical degradation. This makes them ideal for use in environments where exposure to moisture, chemicals, or other corrosive substances is a concern. The longevity and reliability of composite thrust washers in such conditions are significantly higher compared to metal options.
Traditional Metallic Limitation: Metal thrust washers, even those made from corrosion-resistant alloys, can still be susceptible to corrosion over time, especially in harsh or chemically aggressive environments. This can lead to degradation and eventual failure.
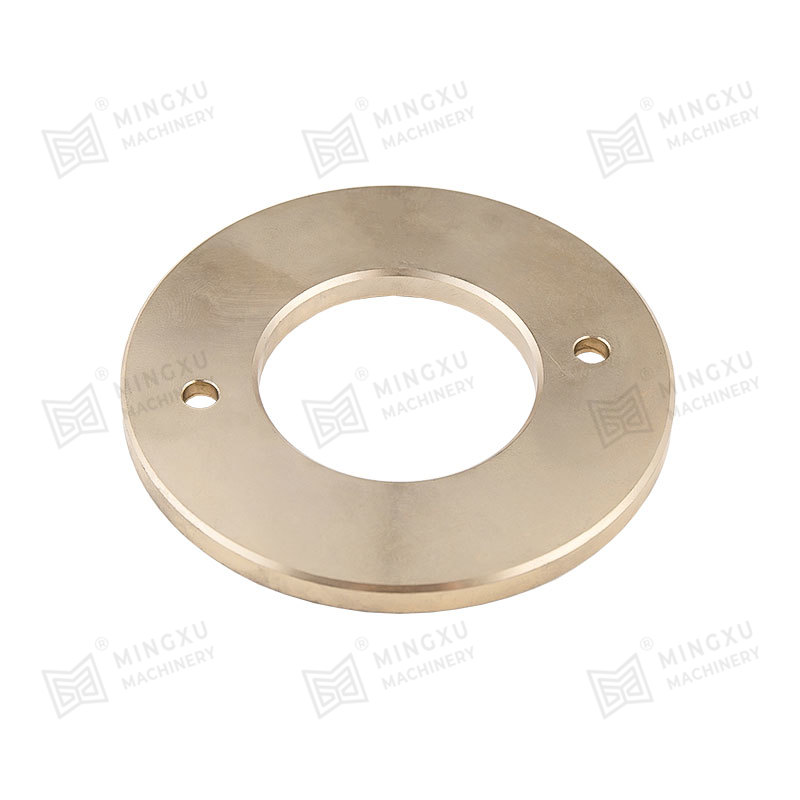
4. Lightweight
Composite Advantage: Composite materials are generally lighter than metals, which reduces the overall weight of the machinery or equipment in which they are used. This is particularly beneficial in applications where weight savings are crucial, such as in automotive, aerospace, and portable equipment, where every gram matters for performance and fuel efficiency.
Traditional Metallic Limitation: Metallic washers, especially those made from dense materials like steel or bronze, add to the overall weight of the assembly. This can be a disadvantage in applications where minimizing weight is essential for performance or energy efficiency.
5. High Load Capacity and Flexibility
Composite Advantage: Advanced composite materials are designed to handle high loads while offering flexibility and resilience. They can absorb shock and distribute loads more evenly across the surface, reducing the likelihood of localized stress and failure.
Traditional Metallic Limitation: While metals can handle high loads, they may not offer the same level of flexibility and shock absorption as composites. Under extreme conditions, metals can experience fatigue and failure due to repeated stress.
6. Dimensional Stability
Composite Advantage: Composites can maintain their shape and dimensions over a wide range of temperatures and environmental conditions. This stability ensures consistent performance and reduces the need for frequent adjustments or replacements due to dimensional changes.
Traditional Metallic Limitation: Metals can expand or contract with temperature fluctuations, which can affect their fit and performance in critical applications. This dimensional instability can lead to maintenance issues and reduced efficiency.
7. Noise Reduction
Composite Advantage: Composites often provide better damping properties, which helps in reducing noise and vibration in mechanical systems. This is particularly beneficial in applications where quiet operation is desired, such as in automotive interiors or household appliances.
Traditional Metallic Limitation: Metallic washers can contribute to higher noise levels due to their harder surfaces and higher friction coefficients, leading to increased vibration and noise during operation.
In summary, composite materials offer significant advantages over traditional metallic options for thrust washers, including enhanced wear resistance, reduced friction, corrosion resistance, lightweight properties, high load capacity, dimensional stability, customizability, noise reduction, environmental resistance, and overall cost efficiency. These benefits make composite thrust washers ideal for a wide range of demanding applications where traditional metal washers may fall short.
Contact Us