Copper sleeve casting is a process in which copper alloy is smelted into a liquid that meets certain requirements and poured into a mold. After cooling, solidification, and cleaning, a casting with a predetermined shape, size, and performance is obtained.
According to the characteristics and development level of the casting copper sleeve technology, the casting method can generally be divided into two types: sand casting copper sleeve and special casting copper sleeve. Commonly used casting methods in the field of copper sleeve casting include centrifugal casting, continuous casting and sand casting.
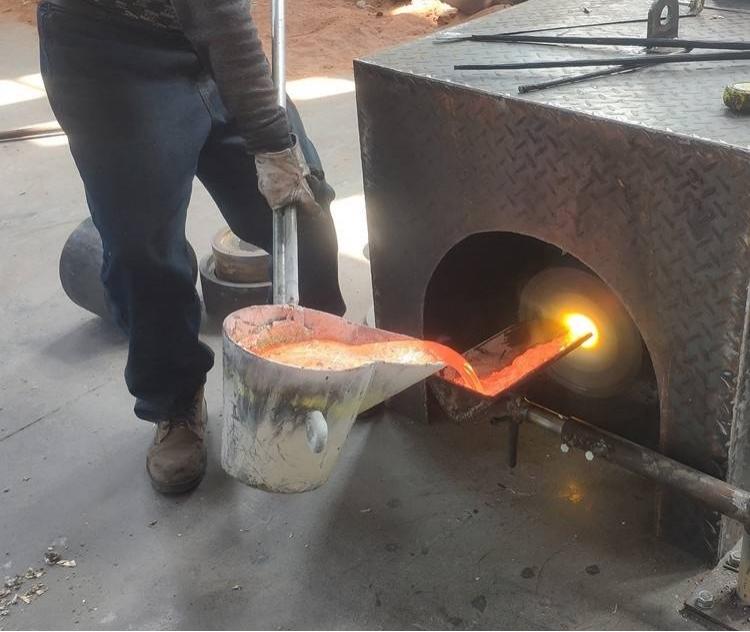
1.Centrifugal casting of copper sleeves
It is a method of casting rings, tubes, barrels, sleeves and other special castings by changing the filling mold and solidification conditions of liquid alloy and using the action of centrifugal force. The characteristics of centrifugal casting are that the molten metal fills and solidifies under the action of centrifugal force, the metal feeding effect is good, the outer layer of the casting is dense, there are few non-metallic inclusions, and the mechanical properties are good; no molding or core making is required, which saves related materials and equipment Invest. Centrifugal casting is the main casting method used by Mingxu to produce medium-sized copper sleeve products.
Casting hollow castings does not require pouring risers, and the metal utilization rate can be greatly improved. Therefore, for certain castings of specific shapes, centrifugal casting is a material-saving, energy-saving, and highly efficient process, but special attention must be paid to effective safety measures.
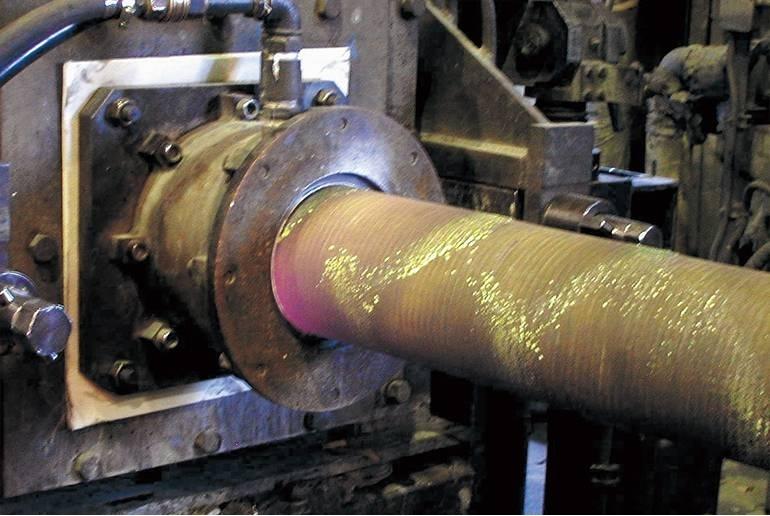
2.Continuous casting
It is an efficient production method that uses a rapidly cooling crystallizer to cast tubes and ingots under the conditions of continuous pouring, solidification, and cooling. Continuous casting is particularly suitable for the mass production of pipes, rods, plates, and profiles. The disadvantage is that it generally cannot manufacture extra-large components. Continuous casting products have the advantages of good mechanical properties, dense structure, and few casting defects. The continuous casting process also has the advantages of high material utilization, low casting cost, low labor intensity, high degree of automation, and high production efficiency. Continuous casting is the main casting method used by Mingxu to produce small and medium-sized batch products.
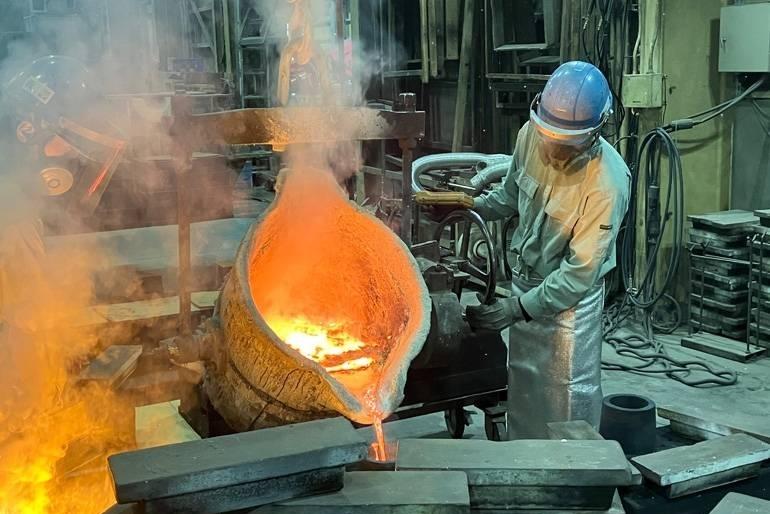
3.Sand casting
It is the most commonly used method in the production of copper sleeves. It has the advantages of wide adaptability and relatively simple production preparation. However, the dimensional accuracy, surface quality and internal quality of castings produced by this method are far from meeting the requirements of mechanical parts. Moreover, the production process is more complicated, and the investment in mechanized and automated production is huge. In the production of some special parts and special technical requirements When casting, the technical and economic indicators are low. Therefore, the application of sand casting in foundry production is subject to certain restrictions. Sand casting is the main casting method used by Mingxu to produce special-shaped and non-standard copper alloy products, such as
oilless bushs.
Contact Us