The geometry of a self-lubricating bushing plays a critical role in its performance, as it affects how the bushing interacts with the surrounding surfaces, the distribution of lubrication, and the efficiency of friction reduction. Here's a detailed look at how different aspects of bushing geometry influence performance in various mechanical systems:
Surface Area and Lubricant Distribution
Larger Contact Area: Bushings with a larger surface contact area can distribute the load over a greater surface, potentially reducing wear and improving the load capacity. A larger contact area also allows for better lubrication retention, as there’s more material to store and release lubricant.
Smaller Contact Area: A smaller contact area may result in higher localized pressure, which could increase wear if the lubrication isn’t sufficient. However, such designs may work better for lower load, high-speed applications where less friction is required.
Radial vs. Thrust Load Bearing
Radial Bushings: For radial applications (e.g., in shafts), the geometry of the bushing, including its inner and outer diameters, determines the amount of lubricant that can be retained and how it is distributed. If the bushing has a smooth surface or spiral grooves, it can enhance the movement of lubricant, improving wear resistance and lowering friction.
Thrust Bushings: These bushings are designed to handle axial loads (forces parallel to the shaft). The geometry, particularly the face area, determines how well the bushing can resist axial loads while maintaining a low coefficient of friction. The material's porosity and thickness are important in ensuring lubrication under thrust conditions.
Pore Structure and Lubricant Release
Porous Geometry: In self-lubricating bushings with porous metals or composite materials, the size, shape, and distribution of the pores directly influence how lubricant is stored and released. Larger pores may hold more lubricant but could leak it out too quickly, whereas smaller pores may retain the lubricant longer, offering better performance in low-velocity or low-load applications.
Sintered vs. Non-Sintered Designs: Sintered bushings, where the pores are formed during manufacturing, have a more uniform lubricant distribution, which leads to more consistent lubrication. Non-sintered designs may have more irregular pore structures that can impact lubricant release efficiency.
Internal and External Profiles
Internal Geometry (Bore Shape): The internal shape of the bushing (whether it's cylindrical, conical, or stepped) affects how evenly the bushing fits around a shaft or other components. A precise fit ensures minimal gap between the bushing and the shaft, improving the distribution of lubrication and reducing the chance of frictional wear.
External Geometry: The external geometry of the bushing, such as flanges or external ribs, can influence its ability to withstand external forces, like radial or axial load. Additionally, external features can help in aligning the bushing properly within its housing, ensuring uniform lubricant distribution and more even wear across the bushing.
Groove Patterns and Lubricant Flow
Grooved or Slotted Bushings: Some self-lubricating bushings incorporate grooves or slots along their surface to facilitate lubricant movement. These grooves help channel lubricant from the internal structure to the surface, improving lubrication at critical points, reducing friction, and extending the life of the bushing.
Helical Grooves: In certain designs, helical or spiral grooves are incorporated to promote the movement of lubricant in a consistent, controlled manner during rotation, helping to maintain a steady lubricant supply even during dynamic operation.
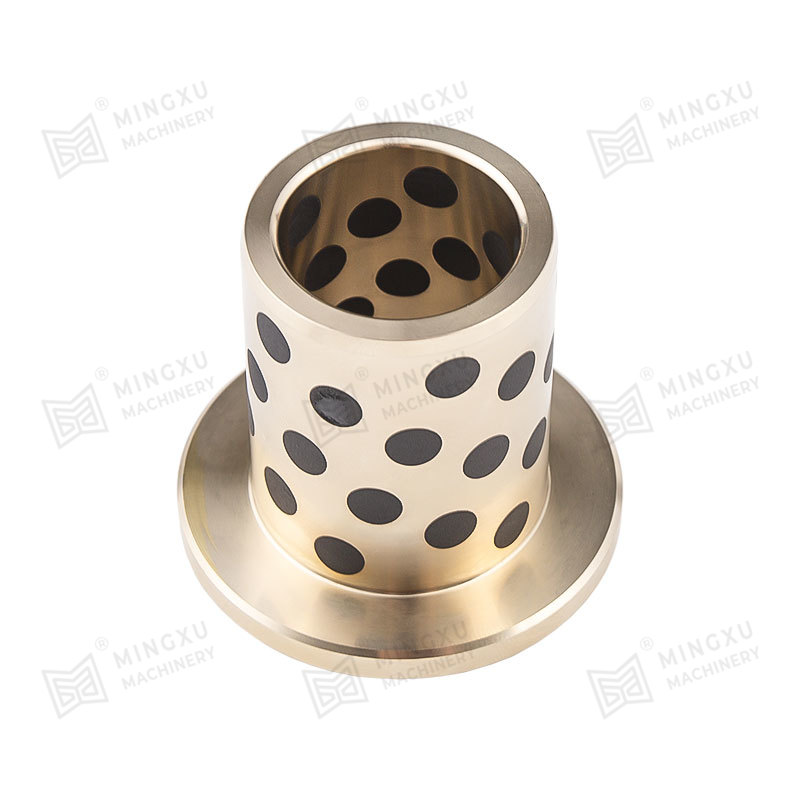
Material Thickness and Lubricant Storage
Thicker Materials: Thicker bushings, especially those with embedded lubrication systems, can store more lubricant, making them ideal for high-load or high-demand applications where lubrication is crucial. These designs allow for longer operational life since the lubricant is more abundant and can be replenished over time.
Thinner Materials: Thinner bushings may have reduced lubricant storage capacity but are lighter and more suitable for low-load or low-speed applications where minimal lubrication is required.
Load Distribution and Deformation
Load Distribution Geometry: The shape and profile of the bushing determine how forces are distributed across the bearing surface. For instance, a bushing with a tapered design might concentrate force at one point, leading to higher localized stress and faster wear. A more uniform geometry, such as a cylindrical bushing, distributes forces more evenly, which can lead to more even wear and longer service life.
Deformation Under Load: The geometry also affects how the bushing deforms under load. A bushing with the correct fit and design will deform in a controlled manner, maintaining proper lubrication coverage. Incorrectly sized bushings, or those with poorly optimized geometry, may deform excessively and lose lubrication effectiveness.
Tolerance and Clearance
Precision Fit: The tolerance between the inner and outer surfaces of the bushing influences the amount of clearance. Too tight a fit can lead to excessive friction, while too much clearance can result in instability and inefficient lubrication distribution. Optimal clearance allows for the necessary lubricant flow and ensures the bushing operates smoothly.
Clearance for Lubricant Flow: The geometry should allow enough clearance for the lubricant to flow between the bushing and the mating surface, but not too much that the lubricant is forced out prematurely. This clearance depends on the material’s ability to store and release lubrication efficiently.
Application-Specific Design
Heavy-Duty Systems: For systems that undergo extreme loads, such as automotive suspension or construction equipment, the geometry of the bushing often includes features to handle higher stress, such as thicker walls, reinforced materials, or external flanges to increase surface area and improve lubrication storage.
Precision Applications: In highly accurate systems like robotics or aerospace, bushings often have highly precise geometries, with very tight tolerances and smooth surfaces to ensure exacting performance and minimal friction.
Temperature and Speed Effects
Thermal Expansion: The geometry of the bushing will change with temperature fluctuations. Self-lubricating bushings with geometry that accommodates thermal expansion will maintain their performance under varying temperatures by maintaining proper fit and lubricant distribution.
Speed Considerations: At higher speeds, the geometry of the bushing might need to be adjusted to prevent excess heat buildup, which could cause lubricant breakdown. Grooves or larger surface areas help dissipate heat and maintain lubricant film integrity.
Contact Us