The distribution pattern of solid lubricant inserts like graphite or molybdenum disulfide (MoS₂) plays a crucial role in the performance of self-lubricating wear plates. The way these lubricants are distributed within the material directly influences their efficiency, longevity, and ability to reduce friction and wear. Here's how the distribution pattern can affect the performance:
Lubricant Coverage and Load Distribution
Even Distribution: When solid lubricants are evenly dispersed across the wear plate, it ensures consistent lubrication across the contact surface. This results in a uniform reduction in friction and wear, preventing localized hotspots or wear patterns.
Localized Distribution: If the lubricant is concentrated in specific areas, those regions will experience more consistent lubrication, but the other parts of the wear plate may be exposed to higher friction, leading to uneven wear. This could lead to premature failure in some areas, while others may show minimal wear.
Lubricant Release and Performance
Gradual Release: In a well-distributed system, the lubricants tend to wear out evenly over time, ensuring a consistent release of lubrication. This helps maintain stable performance throughout the life of the wear plate.
Excessive or Insufficient Release: If too much lubricant is placed in a single region, it may wear out too quickly, leaving parts of the plate dry and more susceptible to friction damage. On the other hand, insufficient lubricant in critical areas could lead to higher wear rates.
Friction Reduction
Optimal Distribution: A uniform pattern of lubricant inserts reduces friction across the entire surface, which is critical in preventing excessive heat generation and maintaining smooth operation. This uniform friction reduction ensures optimal performance in applications involving high-speed motion or sliding.
Uneven Friction: If the lubricant is distributed unevenly, certain sections of the wear plate may have higher friction, leading to more wear and possibly overheating in those areas. This can affect the overall efficiency and lifespan of the components in contact with the wear plate.
Wear Resistance and Durability
Better Durability with Uniform Distribution: A uniform distribution of lubricants like graphite or MoS₂ leads to better wear resistance, as the lubricant is more likely to be present where it’s needed most, ensuring the material remains protected throughout its life cycle.
Localized Wear Issues: If the lubricant is concentrated in specific zones, those areas may resist wear well but may lead to higher wear in regions with little to no lubrication. This can result in premature failure or reduced overall lifespan of the wear plate.
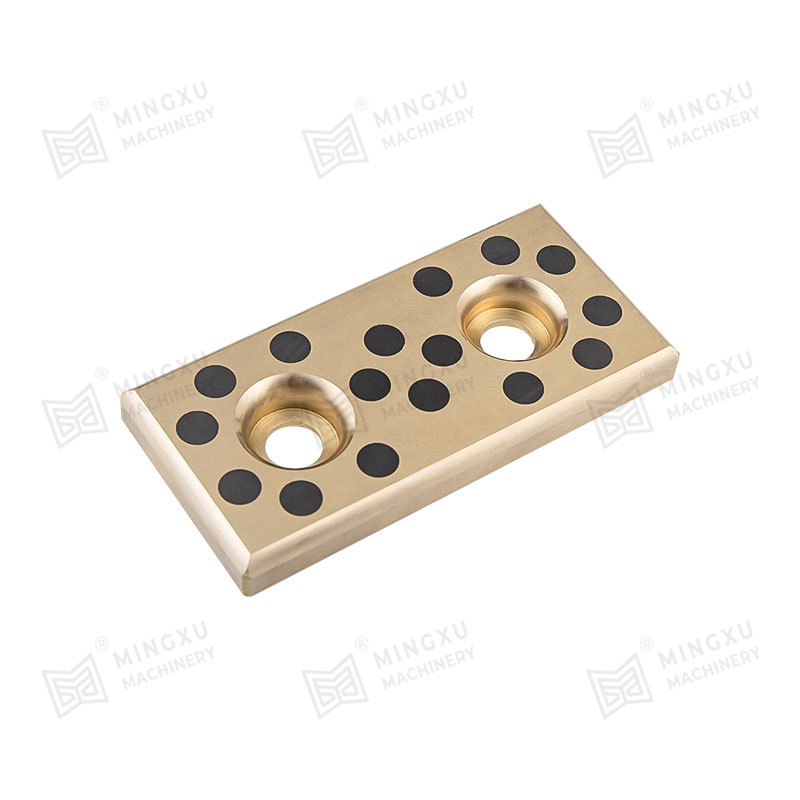
Temperature Management
Heat Dissipation: Graphite and MoS₂ are both effective at high temperatures. If the lubricant is evenly distributed, it can help dissipate heat across the wear plate more evenly, preventing hotspots that could cause thermal damage or excessive material degradation.
Localized Heating: Areas with insufficient lubricant will experience more friction, leading to heat buildup and potential thermal damage to both the wear plate and the mating components.
Customized Performance
Tailored Distribution for Specific Applications: In some cases, manufacturers might opt for a non-uniform distribution to optimize performance in specific zones where higher friction or higher loads are expected. For example, more lubricant may be applied to sections of the wear plate subject to higher contact pressures, while less lubricant is used in lower-stress areas.
Lubricant Lifespan
Longer Lifespan with Controlled Distribution: Properly controlled lubricant distribution ensures that the lubricant lasts longer and provides effective performance throughout the wear plate’s life. Uneven patterns can cause the lubricant to deplete faster in certain areas, reducing the overall lifespan of the wear plate.
Manufacturing Considerations
Injection or Impregnation Techniques: The method used to embed the solid lubricants, such as powder impregnation, resin infusion, or machining inserts, also affects the distribution. Manufacturing processes that allow for better control of the pattern—such as precision insertion or uniform powder mixing—can enhance the effectiveness of the lubrication.
Key Takeaways:
Uniform Distribution of solid lubricants provides consistent wear resistance, lower friction, and longer service life.
Localized or Uneven Distribution can lead to uneven wear, overheating, and faster degradation of the wear plate.
The choice of distribution pattern should be aligned with the specific application needs, load-bearing requirements, and environmental conditions.
Contact Us