In the vast realm of the chemical industry, the safe and stable operation of equipment is of paramount importance. Faced with complex and ever-changing chemical corrosion environments, traditional lubrication methods often struggle to meet the high demands for durability and reliability of equipment. Self-lubricating bearings, with their unique corrosion resistance and stable lubrication characteristics, have demonstrated significant application value in the chemical industry.
Chemical Corrosion Scenarios in the Chemical Industry
In the chemical industry, equipment is often exposed to extremely harsh environments, whether it's high temperatures reaching hundreds of degrees Celsius or high pressures of tens of megapascals, all posing severe challenges to equipment performance. More complexly, equipment must also withstand the erosion of various corrosive media, such as sulfuric acid with a concentration of up to 98%, sodium hydroxide at 50%, as well as organic solvents like methanol and ethanol, and harmful chemicals such as chlorides and sulfides. Under specific conditions, these media can cause severe corrosion to equipment, leading to performance degradation or even failures, seriously impacting production efficiency and safety.
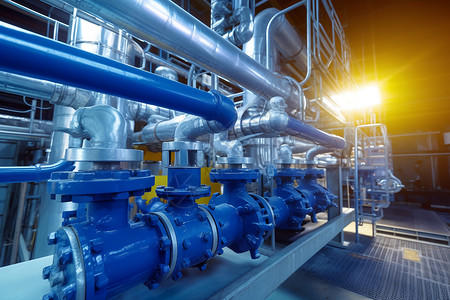
Corrosion Resistance of Self-Lubricating Bearings
Material Selection:
PEEK Self-Lubricating Bearings: PEEK material stands out for its excellent corrosion resistance, capable of withstanding the erosion of various strong acids, strong bases, organic solvents, and chlorides. Experimental data shows that PEEK exhibits an extremely low corrosion rate in a 20% sulfuric acid solution, at just below 0.1mm/year, and performs equally well in a 50% sodium hydroxide solution. Furthermore, with a melting point of 340°C, PEEK ensures stable performance in high-temperature environments.
JDB Copper-Based Embedded Self-Lubricating Bearings: The copper base material itself possesses certain corrosion resistance, particularly in neutral or weakly acidic environments. The built-in solid lubricants (such as graphite and molybdenum disulfide) provide continuous lubrication during friction, effectively reducing direct contact with corrosive media and thereby extending the service life of the bearings. Data indicates that JDB bearings exhibit a corrosion rate significantly lower than that of ordinary steel in a 3% hydrochloric acid solution, demonstrating good corrosion resistance.
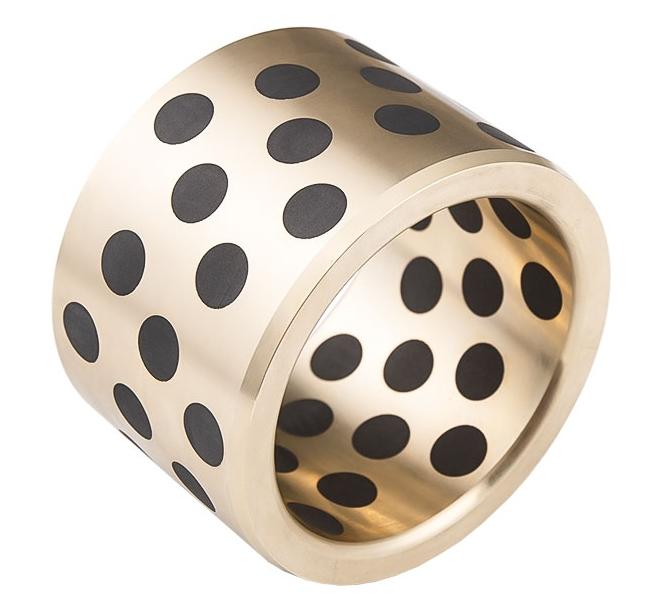
Lubrication Performance:
Another major advantage of self-lubricating bearings is that they do not require external lubrication and have an extremely low friction coefficient (typically between 0.02 and 0.1), enabling stable operation under oil-free or low-oil conditions. This characteristic not only reduces the use and leakage risk of lubricating oil but also lowers environmental pollution and maintenance costs, providing strong support for the green development of the chemical industry.
Application Examples
Reactors: Self-lubricating bearings are widely used in key components such as agitators and shaft seals in chemical reactors. Taking PEEK self-lubricating bearings as an example, after one year of use in a reactor, their wear is only one-tenth that of conventional bearings, significantly extending the service life of the equipment and improving production efficiency.
Heat Exchangers: Self-lubricating bearings also perform well in heat exchangers, commonly used in pumps, valves, and other components. JDB copper-based embedded self-lubricating bearings demonstrate good corrosion and wear resistance in heat exchangers, maintaining stable operation even under the effects of high temperature, high pressure, and corrosive media, ensuring long-term stable operation of the equipment.
Storage Tanks: In chemical storage tanks, self-lubricating bearings are often used in agitators, level gauges, and other components. PEEK self-lubricating bearings, with their excellent corrosion resistance, can operate stably for a long time in storage tanks, effectively reducing failures and maintenance costs due to corrosion, providing strong safety guarantees for the production of chemical enterprises.
Precautions
When selecting self-lubricating bearings, it is necessary to comprehensively consider the bearing material and model based on specific chemical corrosion media, temperature, pressure, and other conditions. For example, in strong acid or base environments, PEEK self-lubricating bearings are undoubtedly the first choice; while in neutral or weakly acidic environments, JDB copper-based embedded self-lubricating bearings also perform well.
Additionally, attention should be paid to the installation and maintenance of the bearings. During installation, the bearings should be protected from excessive impact and vibration; during maintenance, the wear condition and lubrication status of the bearings should be regularly checked, and damaged bearings should be replaced in a timely manner to ensure stable operation and optimal corrosion resistance.
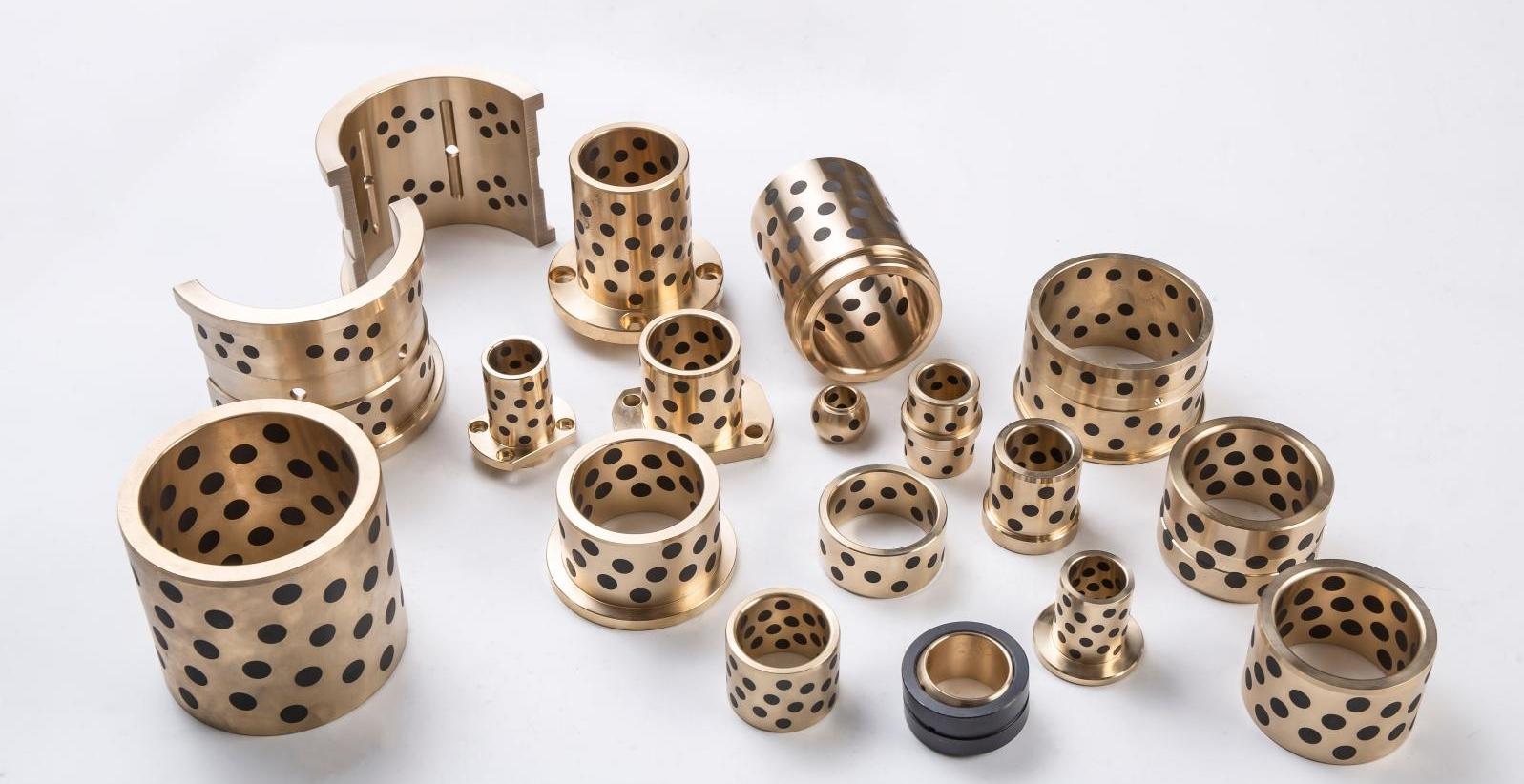
Zhejiang Mingxu Machinery Manufacturing Co., Ltd. has developed self-lubricating bearing products with chemical corrosion resistance using high-quality raw materials to meet the application needs of the chemical industry, effectively improving the energy efficiency of chemical industry equipment and saving equipment and maintenance costs for enterprises. If you have such needs, feel free to discuss and exchange ideas with us at: [email protected].
Contact Us