Self-lubricating bearings utilize solid lubricants as the lubricating medium, adapting to a broad temperature range for effective performance in both high and low temperature environments. The solid lubricants remain fully filled throughout the entire operating life cycle, with intermittent release forming and repairing a solid lubricating film between friction surfaces. This results in low wear and anti-seizure properties, effectively protecting the shaft surface and ensuring long-life operation. The bearings exhibit significant advantages in various environments, including high temperature, vacuum, low speed, heavy load, swing, dust, water, impact, vibration, and more. They find wide applications in port machinery, engineering machinery, water conservancy, hydraulic engineering, mining machinery, metallurgy, petroleum, chemical industry, food, textile, papermaking, printing and dyeing, sea and air, wind power, ships, and other mechanical equipment's rolling and sliding bearing parts.
For instance, in the aluminum industry, the liquid byproduct from the aluminum electrolyzer is extracted using a vacuum bag and directed to a mixing furnace. After proportioning and slag removal, it flows into the aluminum ingot casting machine for molding. The resulting aluminum ingots are stacked using stackers. To enhance production efficiency, the aluminum ingots undergo substantial cooling with water before forming, releasing heat energy into the cooling water and generating hot water vapor. However, conventional casting machine bearings face challenges in high-temperature and water-intensive environments. Many bearings rely on grease lubrication, which poses maintenance difficulties due to grease melting and overflowing in high temperatures. Additionally, steel structure bearings are prone to corrosion and rust in hot and humid conditions, leading to high failure rates and maintenance costs.
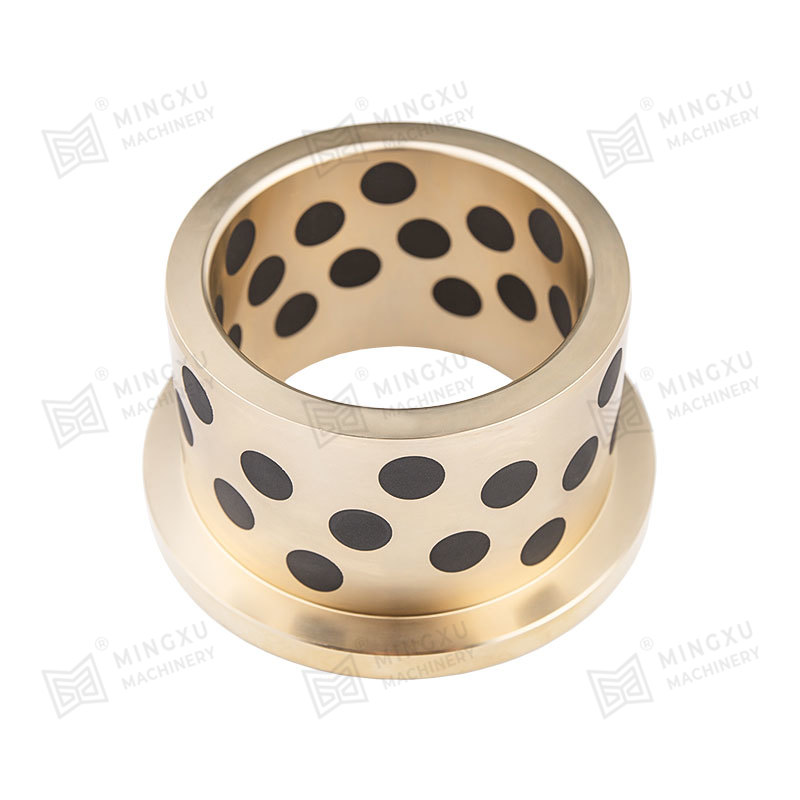
Addressing these challenges, the article emphasizes the importance of using self-lubricating bearings in such demanding conditions. The traditional approach of lubricating with grease becomes impractical in high-temperature environments, as demonstrated in the case of aluminum ingot casting machines. The use of molybdenum disulfide grease, believed to withstand high temperatures, falls short when operating temperatures surpass its limit. Under extreme conditions, the grease breaks down, hindering lubrication and causing rapid wear of rolling bearings. This often necessitates a lengthy shutdown of the machine for bearing removal, cleaning, and replacement with new grease.
Wear conditions in aluminum equipment bearings are exacerbated by inadequate lubrication methods. In the case of an aluminum company's ingot pulling mechanism, the bearings experience severe wear, with an average service life of only 2 months. Uneven wear occurs due to the inability to implement the original designed oil supply method, resulting in the pouring of thin oil on the outside of running bearings. This limited lubrication leads to strong adhesive wear, increasing clearance between the shaft and sleeve and facilitating dust entry, creating a detrimental cycle of wear and tear.
Contact Us