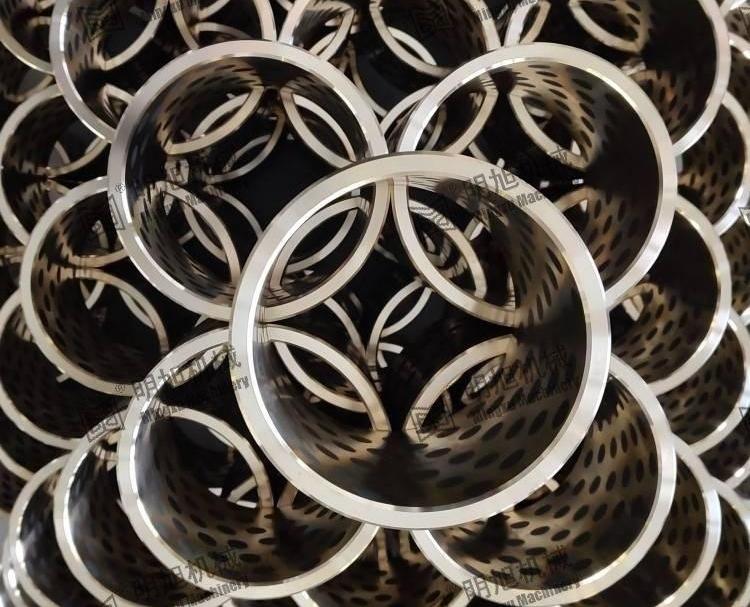
Wear resistance is one of the most critical factors of the copper sleeve. The better the wear resistance, the longer the life of the copper sleeve, the lower the maintenance cost, and the more reliable the operation of the mechanical parts. Therefore, most customers will consider the wear resistance of the copper sleeve when purchasing it. Although hardness has a certain relationship with wear resistance, the higher the hardness of the copper sleeve, the better the wear resistance.
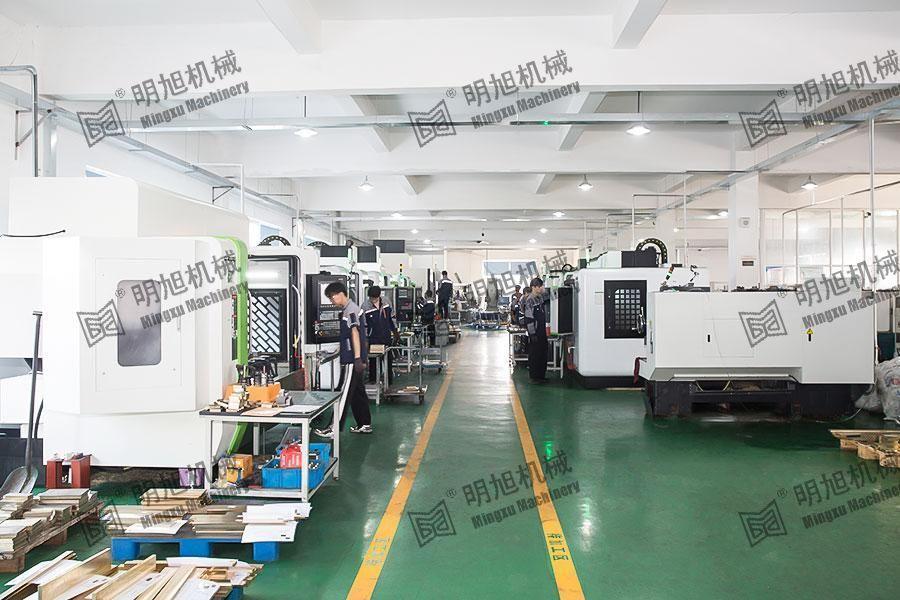
As a professional copper sleeve manufacturer that has been deeply involved in the industry for more than ten years, Mingxu Machinery summarizes the following points to provide ideas for you:
1. Balance between hardness and toughness
Excessive hardness is prone to brittle cracking:
- When the hardness of the copper sleeve is very high, the material tends to become very brittle. In actual use, the copper sleeve will be subjected to various dynamic loads and impacts. If the material is too brittle, it is easy to crack or even break.
- For example: In some heavy machinery and equipment, the vibration and impact during the working process are large. If the copper sleeve is too hard and lacks toughness, it is likely to suddenly break during use, causing equipment failure.
Moderate toughness can buffer:
- Copper sleeves with a certain toughness can better absorb and buffer external shocks and vibrations. This can reduce the wear and damage caused by instantaneous impact force.
- For example, in some mechanical devices with frequent start-stop actions, the copper sleeve needs to withstand large instantaneous forces when starting and stopping. Moderate toughness can make the copper sleeve better adapt to changes in these situations and reduce wear.
2. Matching of friction pairs
Matching with shafts:
- The copper sleeve is usually used in conjunction with the shaft, and the two form a friction pair. If the hardness of the copper sleeve is too high, it may cause excessive wear on the shaft.
- For example, in some precision transmission systems, the material of the shaft usually also has certain hardness requirements. If the hardness of the copper sleeve is too high, the wear of the shaft will increase, thereby affecting the accuracy and life of the entire transmission system.
Stability of the overall system:
- The matching of friction pairs needs to comprehensively consider multiple factors such as hardness and roughness. If the hardness of the copper sleeve is too high and does not match the hardness of the shaft, the friction coefficient will be unstable, which will in turn affect the operating stability of the entire system.
- For example, in some high-speed rotating machinery, a slight change in the friction coefficient may cause large vibration and noise, and even affect the normal operation of the equipment.
3. The influence of lubrication conditions
The influence of hardness on lubrication:
- Too high hardness may affect the adhesion and retention of lubricants on the surface of copper sleeves. Surfaces with higher hardness are usually smoother, which is not conducive to the storage of lubricants and the formation of a stable lubricating film.
- For example, in some occasions that require good lubrication conditions, such as the bearings inside the engine, if the hardness of the copper sleeve is too high, the lubricant may not be able to effectively adhere to its surface, thereby reducing the lubrication effect and increasing wear.
The effect of lubrication on wear resistance:
- Good lubrication can greatly reduce the friction coefficient and reduce wear. Even if the hardness of the copper sleeve is not very high, it can also show good wear resistance under sufficient lubrication conditions.
For example, in some mechanical systems that use oil lubrication or grease lubrication, a reasonable lubrication scheme can effectively extend the service life of the copper sleeve, rather than simply relying on increasing the hardness of the copper sleeve.
4. Cost and processing difficulty
Cost factors:
- Increasing the hardness of the copper sleeve usually requires special alloy composition and heat treatment process, which will increase production costs.
- For example, some high-performance copper alloy materials are more expensive and the processing process is more complicated, which will significantly increase the overall cost of the copper sleeve. For some cost-sensitive applications, too high a hardness may not be economical and practical.
Processing difficulty:
- Copper sleeves with too high a hardness will place higher requirements on tools and processing equipment during processing, increasing processing difficulty and cost.
- For example, copper sleeves with high hardness may require the use of harder tools and higher-power processing equipment, and the processing speed will also be limited, which will extend the production cycle and reduce production efficiency.
Zhejiang Mingxu Machinery Manufacturing Co., Ltd. has been engaged in the research and development and production of copper alloy components and self-lubricating bearings for more than ten years, and has rich production experience and technical accumulation. Please feel free to contact us at [email protected] for any product and technical questions.
Contact Us