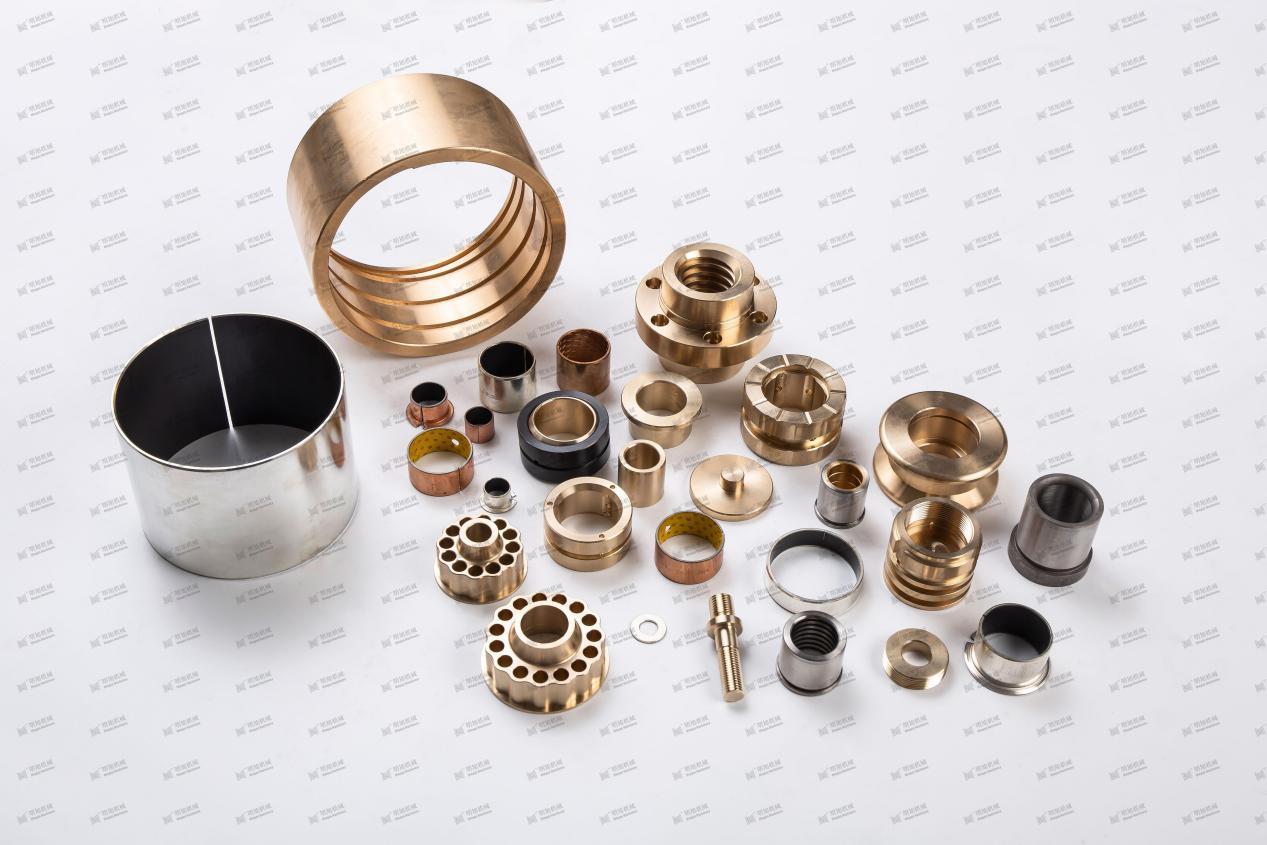
When discussing the wear resistance of steel sleeve and copper sleeve, multiple factors need to be considered, including the specific application environment, load conditions and lubrication conditions. Here are some key points to help you understand the difference in wear resistance between steel sleeve and copper sleeve:
Steel sleeve
Advantages:
- High hardness: Steel is usually harder than copper, so it has better wear resistance in some cases.
- High strength: Steel has higher strength and can withstand greater loads.
- Corrosion resistance: After proper treatment (such as plating, quenching, etc.), steel sleeves can have good corrosion resistance.
Disadvantages:
- Easy to wear shaft: When the steel sleeve contacts the shaft, it is easy to cause shaft wear due to its high hardness.
Requires lubrication: Steel sleeves usually require good lubrication conditions, otherwise they will accelerate wear.
Copper sleeve
Advantages:
- Self-lubricating performance: Copper sleeves have certain self-lubricating properties, which can reduce wear even in the absence of external lubrication.
- Not easy to wear shaft: Copper has a lower hardness and will not wear the shaft as easily as steel.
- Good thermal conductivity: Copper has good thermal conductivity, which helps to dissipate heat and reduce wear caused by high temperature.
- Corrosion resistance: Copper has good corrosion resistance, especially in certain specific environments (such as seawater and acidic environments).
Disadvantages:
- Low hardness: Copper has lower hardness than steel, so under high load and high wear conditions, the wear resistance of copper sleeves is relatively poor.
- Low strength: Copper has low strength and is not suitable for bearing very large loads.
Comprehensive comparison
- Wear resistance: Steel sleeves have better wear resistance under high hardness and high load conditions, but are easy to wear the shaft.
- Copper sleeves have better wear resistance under low load and self-lubrication conditions, and are not easy to wear the shaft.
- Application environment: Steel sleeves are suitable for environments with high loads, high hardness and good lubrication.
Copper sleeves are suitable for low loads, environments that require self-lubrication and corrosion resistance.
Comprehensive comparison
- Wear resistance: Steel sleeves have better wear resistance under high hardness and high load conditions, but are easy to wear the shaft.
- Copper sleeves have better wear resistance under low load and self-lubrication conditions, and are not easy to wear the shaft.
- Application environment: Steel sleeves are suitable for environments with high loads, high hardness and good lubrication.
- Copper sleeves are suitable for low loads, environments that require self-lubrication and corrosion resistance.
Specific application examples
Steel sleeves:
Suitable for heavy machinery, high-load transmission systems, high-precision equipment, etc.
For example: automobile engines, industrial gearboxes, high-load bearings, etc.
Copper sleeves:
Suitable for light loads, environments with high self-lubrication requirements, and environments with high corrosion resistance requirements.
For example: precision instruments, ship equipment, chemical equipment, etc.
Conclusion
Steel sleeves have better wear resistance under high hardness and high load conditions, but attention should be paid to lubrication and shaft protection.
Copper sleeves have better wear resistance under low load and self-lubrication conditions, and are not easy to wear the shaft, suitable for corrosion-resistant environments.
The choice of sleeve material depends on the specific application requirements, including load, speed, lubrication conditions and environmental factors.
If you need more detailed technical parameters or have specific application requirements, please refer to the relevant technical information or consult Mingxu Machinery:[email protected].
Contact Us