Oilless bearings, also known as self-lubricating bearings, are designed to operate without the need for external lubrication. They rely on materials with inherent lubricating properties to reduce friction and wear. Here are the key materials and manufacturing techniques used in their production:
Metallic Alloys: Many oilless bearings are made from metallic alloys with embedded solid lubricants, such as bronze, aluminum, or stainless steel. These alloys are often porous, allowing the lubricating particles to be distributed evenly throughout the material.
Sintered Bronze: Sintered bronze bearings are commonly used in oilless bearing applications. They are produced by compacting and sintering bronze powder under high pressure and temperature. The resulting porous structure holds lubricant particles, providing continuous lubrication during operation.
Polymer Composites: Self-lubricating polymer composites, such as PTFE (polytetrafluoroethylene) or nylon reinforced with solid lubricants like graphite or molybdenum disulfide, are used in oilless bearings. These materials offer low friction coefficients, high wear resistance, and resistance to chemicals and moisture.
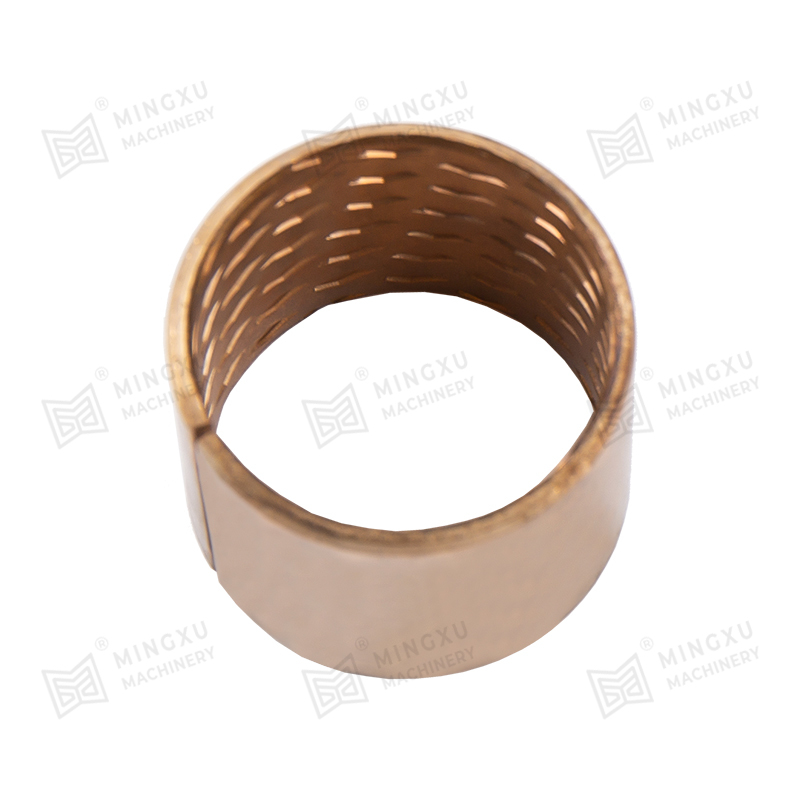
Powder Metallurgy: Powder metallurgy techniques, including pressing, sintering, and impregnation, are commonly used to manufacture oilless bearings. Metal powders and lubricant additives are blended, compacted into the desired shape, and sintered to form a porous structure with lubricant-filled voids.
Injection Molding: Injection molding processes can be used to produce oilless bearings from polymer composites. The polymer matrix is mixed with solid lubricants and injected into molds to form the desired shape. This method allows for complex geometries and precise control over material composition.
Graphite Coatings: Some oilless bearings feature a graphite coating applied to the bearing surface. Graphite provides a low-friction interface and acts as a solid lubricant, reducing wear and extending the bearing's service life. The coating can be applied using techniques such as thermal spraying or electroplating.
Solid Lubricant Impregnation: In this technique, solid lubricants such as graphite or PTFE are impregnated into the pores of the bearing material using vacuum or pressure infiltration methods. This ensures a consistent distribution of lubricant throughout the bearing structure.
These materials and manufacturing techniques are chosen based on the specific requirements of the application, including load capacity, operating temperature, speed, and environmental conditions, to ensure optimal performance and longevity of oilless bearings.
Contact Us