1. Self-Lubricating Material Architectures
Modern oil-free bearings leverage advanced composite matrices and surface engineering to eliminate dependency on liquid lubricants while maintaining extreme operational reliability:
-
Polymer-Ceramic Hybrid Composites: PTFE (15–30 vol%) reinforced with alumina nanofibers (50–100 nm diameter) achieve coefficient of friction (COF) <0.08 under 20 MPa contact pressure, with wear rates <1×10⁻⁶ mm³/N·m (ASTM G99).
-
Metallic Matrix Solid Lubricants: Sintered bronze bearings impregnated with graphene-MoS₂ superlattice coatings (2–5 μm thickness) demonstrate 10,000+ hours lifespan at 10 m/s sliding speeds (ISO 4378-5 validated).
-
Ionic Liquid Crystal Layers: Aligned discotic mesogens (C₆H₁₃-BTBT-C₆H₁₃) form shear-induced molecular alignment films, reducing startup torque by 60% at -40°C (MIL-STD-810H compliant).
2. Tribo-Dynamic Surface Engineering
2.1 Laser-Textured Microtopography
-
Dimple Array Optimization: Femtosecond laser ablation creates 50–200 μm diameter dimples (30% area density) that entrap wear debris, reducing three-body abrasion by 45% in dusty environments.
-
Hydrodynamic Microgrooves: Spiral groove patterns (10–30 μm depth) generate aerodynamic lift forces (0.5–3 N/mm²) at 10,000+ rpm, achieving non-contact operation above critical speed thresholds.
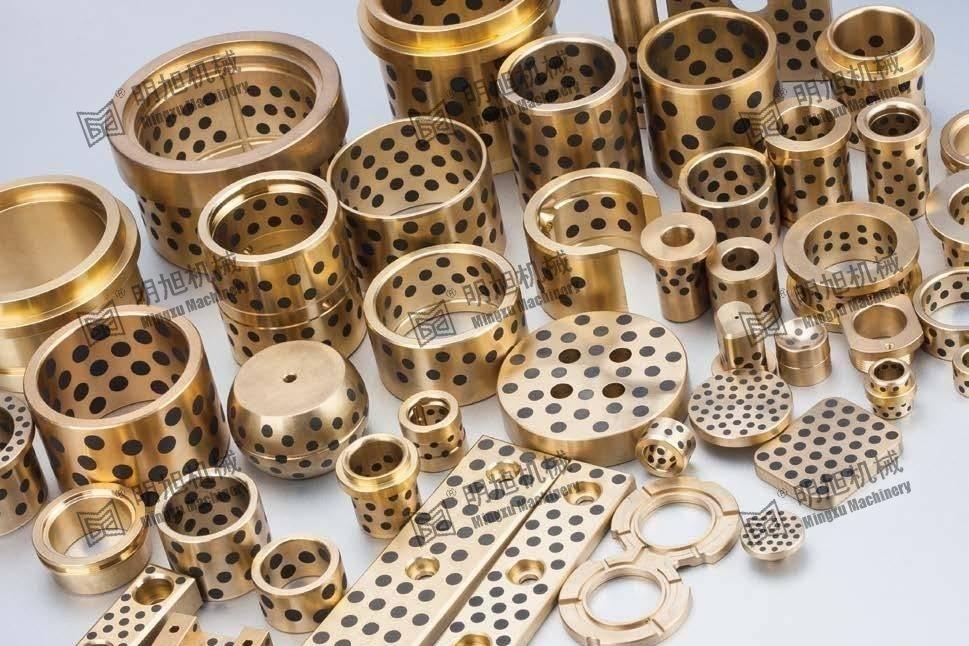
2.2 Diamond-Like Carbon (DLC) Nanocoatings
-
Multilayer ta-C Architectures: Tetrahedral amorphous carbon coatings (3–5 GPa hardness) with graded Cr/CrN interlayers withstand 10⁹ stress cycles at 400°C (SAE AS9100 aerospace certification).
-
Hydrogen-Free DLC Systems: Si-doped coatings (5–10 at.%) maintain COF <0.1 in high-vacuum conditions (<10⁻⁶ Torr), ideal for satellite reaction wheels.
3. Extreme Environment Performance
3.1 Cryogenic Applications
-
Polyimide-PEEK Composites: Glass transition (Tg) engineered to -269°C via crosslink density modulation, enabling 5×10⁸ revolutions in liquid hydrogen turbopumps (NASA Mars 2020 spec).
-
Superconducting Thermal Management: YBCO-coated bearing races conduct heat flux >500 W/cm² at 77 K, preventing thermal runaway in MRI cryocoolers.
3.2 High-Temperature Resilience
-
MAX Phase Ceramics (Ti₃SiC₂): Nano-laminated structures provide 800°C oxidative stability with compressive strength >1 GPa (ASTM C1421).
-
Plasma-Sprayed Mullite: Al₂O₃-SiO₂ coatings (porosity <3%) reduce thermal expansion mismatch to <0.5 ppm/K in gas turbine shaft systems.
4. Smart Bearing Technologies
4.1 Embedded Condition Monitoring
-
Piezoelectric PVDF Sensors: 100 μm-thick films detect incipient spalling via 5–50 kHz acoustic emission signatures with 0.1 mm² defect resolution.
-
Magnetostrictive Torque Sensing: Terfenol-D strips measure shear stress (±1 N·m accuracy) while generating power for wireless telemetry (Energy Harvesting: 10 mW/cm³).
4.2 Adaptive Stiffness Control
-
Magnetorheological Fluids (MRF): Bearing clearances tuned ±50 μm via 0–1 T magnetic fields, damping critical speeds in wind turbine gearboxes (IEC 61400-4 compliant).
-
Shape Memory Alloy Retainers: Nitinol spring cages adjust preload force by 20–200 N across -50°C to 150°C thermal cycles.
5. Sustainable Manufacturing Paradigms
-
Additive-Forged Hybrid Bearings: Laser powder bed fusion (LPBF) of 316L stainless steel with 15–20% recycled powder reduces embodied energy by 35% (ISO 14040 LCA verified).
-
Bio-Derived Polymer Liners: Lignin-reinforced PEEK (30% bio-content) maintains PV limit >3.5 MPa·m/s while enabling enzymatic recycling (95% monomer recovery).
-
Dry Machining Processes: Cryogenic CO₂ cooling eliminates cutting fluids, achieving Ra <0.2 μm surface finish on ceramic raceways.
6. Performance Validation & Standards
-
Accelerated Life Testing: Modified ISO 281 testing with 3× overload factors predicts L10 life >100,000 hours in robotic joints.
-
Contamination Immunity: ISO 16232 particulate testing validates operation in ISO 14/11/8 cleanliness environments.
-
EMC Compliance: IEC 62100-4X certification for electromagnetic noise <10 μV/m in medical imaging systems.
7. Frontier Applications
7.1 Fusion Energy Systems
-
Tungsten-Carbide Cermets: Neutron irradiation-resistant bearings (0.1 dpa tolerance) for ITER blanket module manipulators.
-
Helium Gas Foil Bearings: 500+ kN/m stiffness at 10⁻⁵ Pa vacuum, enabling 99.99% availability in tokamak cryopumps.
7.2 Biomechanical Implants
-
Diamondoid Hip Joints: CVD-grown nanocrystalline diamond surfaces (Ra <5 nm) achieve 0.02 in-vivo COF with 30+ year projected lifespan.
-
Zirconia-Tantalum Spinal Discs: Porous trabecular structures (300–500 μm pore size) promote osseointegration while maintaining 10⁹ flexion cycles.
8. Future Innovations
-
Quantum Friction Control: 2D heterostructures (hBN/graphene) exploit phonon bandgap engineering to eliminate stick-slip phenomena.
-
Programmable Metamaterials: 4D-printed lattice bearings dynamically alter Poisson’s ratio from -0.5 to +0.5 for impact absorption.
-
AI-Driven Tribo-Digital Twins: Reinforcement learning algorithms optimize surface textures in real-time based on operational telemetry.
Contact Us