(1) It must have low shear strength in the sliding direction and high yield point in the loading direction.
(2) The adhesion to the substrate must exceed the tangential force that occurs during sliding to prevent the lubricant from being brushed off the substrate.
(3) There must be sufficient cohesion between particles to establish a thick enough film to prevent surface peaks from penetrating and to store lubricant.
(4) The size of the particles should be largest in the direction of low shear strength, so as to ensure that the particles can be well oriented between sliding surfaces.
(5) Moderate compatibility with relative sliding surfaces.
(6) Sufficient chemical stability over a wide temperature range.
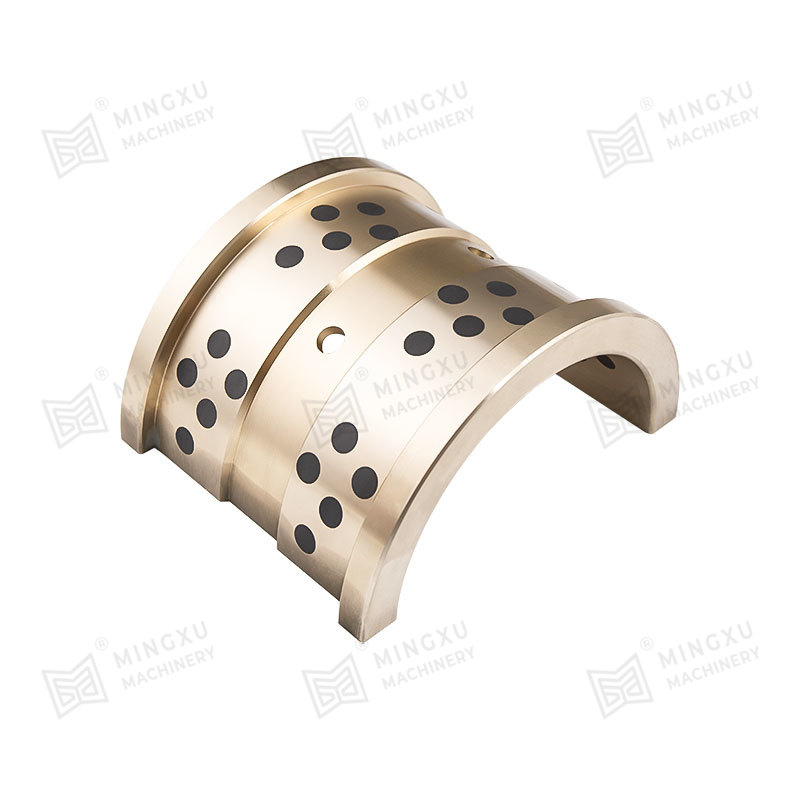
Currently commonly used solid lubricants include graphite, MoS2, Wse2, NbSe2, fluorinated graphite, graphite nitride, boron nitride, polyimide and polytetrafluoroethylene. In fact, graphite and MoS2 are widely used solid lubricants. However, in the presence of water vapor and other gas adsorption layers, MoS2 will lose its lubrication effect due to a significant increase in friction coefficient. Graphite has a hexagonal crystal system layered structure, which is in the form of scales. The inner atomic bonding force is strong, the interlayer atomic bonding force is weak, and the specific gravity is small. It can be used for short-term use at 540°C in the atmosphere and for long-term use at 426°C. It is chemically stable. Good, it has certain radiation resistance. The solubility of graphite in nickel and copper is very small. The solid solution formed by nickel and a small amount of carbon can improve the hardness and strength of the material. The remaining carbon exists in the material in the form of graphite to ensure the lubrication effect.
Contact Us