Imagine that if the axle of a car had no lubricant, it would smoke and break down after driving for a few kilometers; or if the hinges of a door at home were rusty and squeaked every time it was opened and closed - this is the "arthritis" of the machine world. In factories, thousands of equipment bearings are like the "joints" of machines. Once they are not lubricated properly, the efficiency will be reduced at best, and even production stoppage accidents will occur at worst.
In the past decade, the industry has relied on traditional lubricants to maintain these "joints", but problems have emerged one after another: oil filling maintenance causes frequent equipment shutdowns, oil leakage pollution makes the workshop floor like an overturned oil bottle, and lubricants will become ineffective under high temperature and high pressure. What's more troublesome is that in extreme environments such as space and the deep sea, lubricants are of no use at all.
The emergence of self-lubricating bearings is equivalent to installing "permanently lubricated joints" on machines. It embeds solid lubricants into metal like "energy capsules" to free equipment from dependence on external lubrication. This article will use real cases to reveal what kind of predicament the factory would fall into without this technology - from burning tens of billions of yuan worth of lubricants every year to premature "aging" and scrapping of equipment, and even causing the country to miss the development opportunity of high-end manufacturing.
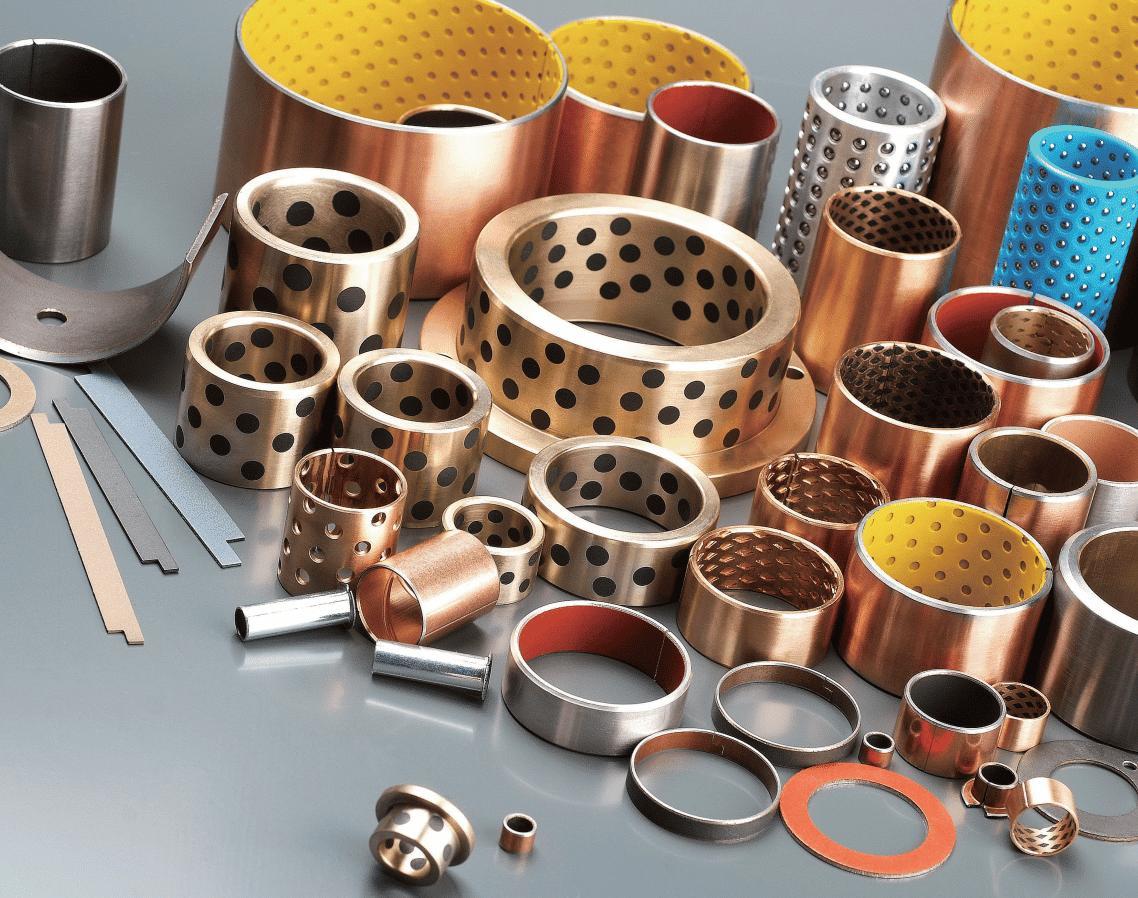
1. Surge in operation and maintenance costs: chain reaction caused by lubrication failure
Manual maintenance frequency doubled
l Case: A certain automobile stamping line uses traditional copper sleeve bearings, which need to be stopped for oiling twice per shift (8 hours), each time taking 35 minutes, resulting in a daily production capacity loss of 18%. If self-lubricating bearings are used instead, it can run continuously for 72 hours without maintenance.
l Data: Statistics from the International Maintenance Association show that the maintenance cost of traditional bearings accounts for 23% of the total equipment cost, which is 4.7 times that of the self-lubricating solution.
Lubricant consumption is out of control
l Consumption: A single heavy mining equipment consumes 3.5 tons of lubricating oil per year (worth $12,000), while self-lubricating bearings can reduce the amount by 90%.
l Associated costs: The cost of treating ground pollution caused by lubricant leakage is as high as $85/m² (data from the European Environmental Protection Agency).
2. Equipment reliability collapse: Failure mode from quantitative change to qualitative change
The tolerance to extreme working conditions drops sharply
l High temperature failure: When the connecting rod bearing of an internal combustion engine is at 200°C, the viscosity of traditional lubricating oil drops by 80%, and the wear rate increases to 7 times that of the self-lubricating solution.
l Low temperature embrittlement: When polar scientific research equipment is at -50°C, the solidification of traditional grease causes a 300% surge in starting torque, while the MoS₂-based self-lubricating bearing still maintains a friction coefficient of 0.08.
Sudden failure rate soars
l Data comparison: When the traditional solution is used for wind turbine main shaft bearings, the average annual sudden failure is 2.3 times; after switching to solid lubrication, it drops to 0.2 times (DNV GL report).
l Failure cost: Sudden jamming of rolling mill bearings in steel mills can cause the entire production line to shut down for 48 hours, with direct losses exceeding $1.5 million.
3. The ceiling of production process is solidified: technology upgrade is hindered
High-speed processing capability is limited
l Speed bottleneck: The maximum speed of traditional steel rolling bearings is 45,000rpm, while silicon nitride ceramic self-lubricating bearings can reach 120,000rpm, which increases the efficiency of micro-hole drilling by 400%.
l Precision degradation: When a CNC machine tool spindle does not have self-lubricating technology, the temperature rise causes the axial runout to increase from 2μm to 8μm, and the processing accuracy drops by 3 levels.
New material processing dilemma
l Case: When stamping carbon fiber composite materials, the residual traditional lubricant causes the interlaminar shear strength to drop by 27%, while solid lubricating bearings achieve zero pollution forming.
l Data: The life of aluminum alloy die-casting molds plummeted from 150,000 molds to 40,000 molds due to poor lubrication (Tesla production data).
4. Environmental and safety risks are rising exponentially
Industrial pollution is increasing
l VOC emissions: When the injection molding machine uses mineral oil lubrication, a single unit emits 1.2kg of benzene per year, while the self-lubricating solution achieves zero emissions (EPA test data).
l Heavy metal pollution: The lead precipitation of lead-based babbitt alloy bearings reaches 0.15mg/L, which is 300 times higher than the drinking water standard.
Fire and explosion hazards
l Case: A chemical plant exploded due to ignition of lubricating oil vapor, resulting in a loss of $23 million. Self-lubricating bearings can eliminate such risks.
l Data: Among fires in oil refining equipment, 31% are caused by lubrication systems (NFPA statistics).
5. Structural decline in industrial competitiveness
Dimensions
|
Non-self-lubricating bearing performance constraints
|
Typical consequences
|
Equipment export
|
Unable to meet environmental standards such as the EU ELV Directive
|
A Chinese machine tool company lost $260 million in orders per year
|
Product innovation
|
Electric vehicle range increases by 8% due to transmission loss
|
Battery packs need to increase weight by 15kg to maintain the same range
|
Smart manufacturing
|
The predictive maintenance system lacks data collection nodes
|
The equipment OEE (overall efficiency) has been below 65% for a long time
|
Green transformation
|
Carbon emission intensity is 42% higher than that of advanced enterprises
|
12% of net profit was eroded by carbon tariffs
|
Comparative analysis of alternative technologies
Traditional oil-lubricated bearings
l Disadvantages: Failure under vacuum/high temperature (>200℃), maintenance costs account for 35% of the equipment life cycle cost
l Case: Due to the evaporation of lubricating oil, the original design life of the robotic arm of the International Space Station was only 2 years, but it was extended to 15 years after the self-lubricating bearing was used
Grease lubrication solution
l Limitations: Centrifugal grease removal occurs when the speed exceeds 500,000 dn value (shaft diameter mm×speed rpm), while self-lubricating bearings can withstand 3 million dn value
l Data: After the high-speed rail traction motor bearing was switched to solid lubrication, the maximum operating speed increased from 250km/h to 380km/h
Historical lessons and future warnings
l Fukushima nuclear accident in Japan: failure of lubrication system caused by tsunami is one of the key causes of core meltdown. If water-resistant self-lubricating bearings are used, more cooling time can be gained
l Boeing 787 battery fire: investigation shows that accumulation of grease volatiles in confined spaces is a factor that supports combustion. After switching to solid lubrication, the failure rate of the same type is reduced to zero
Conclusion: Irreversible technological generation gap
The industrial system without self-lubricating bearings will fall into "lubrication dependence" - consuming 280 million tons of standard coal per year (IEA data), permanently losing 15-25 percentage points in overall equipment efficiency (OEE), and losing the entry ticket to high-end manufacturing fields such as new energy and aerospace. This is not only a question of technical route selection, but also a core capability division that determines whether a country can participate in the fourth industrial revolution.
Contact Us