1. Reduction in Lubricant Usage and Waste
Less Lubricant Consumption: Self-lubricating bushings do not require external lubricants, such as oils or greases, which are typically used in traditional bushings. This reduces the overall demand for lubricating fluids and minimizes the environmental footprint of their production and disposal.
Minimized Waste Disposal: Traditional lubrication systems often lead to the disposal of used or contaminated oils and greases, which can have harmful environmental effects if not properly managed. By eliminating this waste stream, self-lubricating bushings contribute to cleaner, more sustainable operations.
2. Lower Risk of Contamination
No Leakage of Lubricants: With traditional bushings, there is always the risk of lubricant leakage, which can contaminate surrounding environments, soil, and water sources. Since self-lubricating bushings do not rely on external lubricants, this risk is completely eliminated, leading to fewer chances of environmental contamination.
Improved Hygiene: In industries such as food processing, pharmaceuticals, or clean rooms, where contamination is a concern, self-lubricating bushings help maintain a cleaner, more sterile environment by avoiding lubricant spills and contamination.
3. Reduced Carbon Footprint
Energy Savings: By reducing friction and wear, self-lubricating bushings help improve the energy efficiency of machinery. Less energy consumption translates directly to lower greenhouse gas emissions and a reduced carbon footprint for industrial operations.
Fewer Transportation and Manufacturing Resources: Since self-lubricating bushings do not require regular delivery of lubricants, there is a reduction in the transportation and manufacturing activities associated with producing and distributing lubricating oils and greases, further decreasing the carbon footprint.
4. Longer Lifespan and Reduced Waste
Extended Service Life: Self-lubricating bushings are designed for extended wear and often have a longer lifespan than conventional bushings. This leads to fewer replacements, less waste generated from used components, and lower consumption of raw materials for manufacturing new bushings.
Reduced Resource Consumption: Since fewer replacements are needed, the overall demand for raw materials (e.g., metals, plastics) used in producing bushings is reduced, contributing to more sustainable resource management.
5. Sustainable Material Options
Eco-Friendly Materials: Many self-lubricating bushings are made from advanced materials that are designed to be more environmentally friendly. Some of these materials can be made from recycled or sustainable sources, further contributing to their overall environmental benefits.
Recyclability: Some self-lubricating bushings are designed for recyclability, which ensures that when they reach the end of their useful life, they can be properly processed and reused, reducing waste sent to landfills.
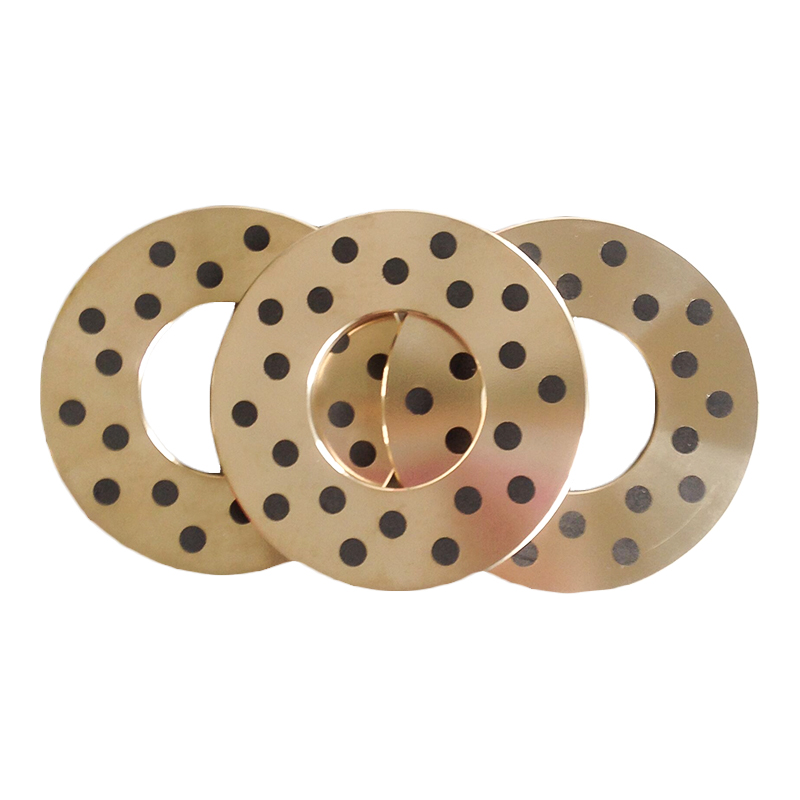
6. Elimination of Chemical Additives
No Chemical Additives Required: Conventional lubrication systems often use chemical additives to enhance performance, reduce wear, or extend lubricant life. These chemicals can be toxic or harmful to the environment if not disposed of properly. Self-lubricating bushings, which often use solid lubricants or composite materials, do not require such additives, reducing the need for potentially harmful chemicals in the system.
7. Reduced Environmental Impact in Harsh Environments
Adaptability to Extreme Conditions: Self-lubricating bushings can function in extreme environments—such as high temperatures, dusty conditions, or corrosive atmospheres—where traditional lubrication might fail or require frequent reapplication. This can help minimize the need for additional resources or energy-intensive maintenance to maintain machinery, reducing the overall environmental impact in these settings.
8. Contribution to Green Manufacturing Practices
Supporting Circular Economy: By reducing the need for external lubricants and decreasing the frequency of part replacements, self-lubricating bushings support a more circular approach to manufacturing. This approach prioritizes resource efficiency, reduces waste, and encourages the reuse of materials, which aligns with sustainability goals and green manufacturing practices.
9. Lowered Environmental Risk in Remote Areas
Reduced Dependency on External Lubrication Systems: In remote or hard-to-reach locations where maintaining traditional lubrication systems can be challenging, self-lubricating bushings provide a sustainable alternative. Their reduced maintenance and lubrication needs make them ideal for operations in areas with limited access to resources and environmental concerns.
10. Promotion of Sustainable Industrial Practices
Cleaner Operations: Industries are increasingly focused on sustainability. By integrating self-lubricating bushings into their machinery, companies can enhance their environmental credentials, reduce their ecological impact, and align with green initiatives that appeal to customers, regulators, and investors who prioritize sustainable practices.
Contact Us