Self-lubricating technology is a technology that uses special materials to reduce friction and wear, so that mechanical parts do not need external lubrication or reduce the need for lubrication during operation. By using solid lubricating materials, films or solid powders, these materials can form a lubricating layer on the force-bearing surface, thereby reducing the friction coefficient, extending the service life of the equipment, and improving operating efficiency. Self-lubricating technology is widely used in bearings, gears, tools, mechanical seals and other fields, and is one of the indispensable key technologies in modern manufacturing and industry.
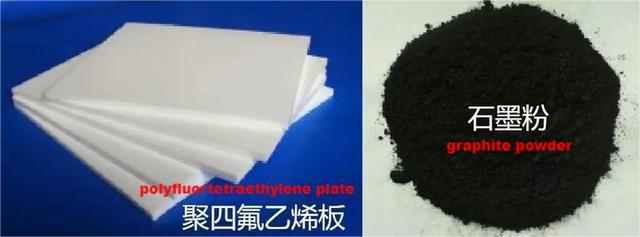
Working principle of self-lubricating technology
Self-lubricating technology relies on the physical and chemical reaction between solid lubricants and friction surfaces to form a lubricating film to reduce the friction between contact surfaces. For example, materials such as graphite, molybdenum disulfide and polytetrafluoroethylene (PTFE) are often used as solid lubricants. Through the introduction of these lubricating materials, the smooth operation of mechanical parts can be maintained without liquid lubrication.
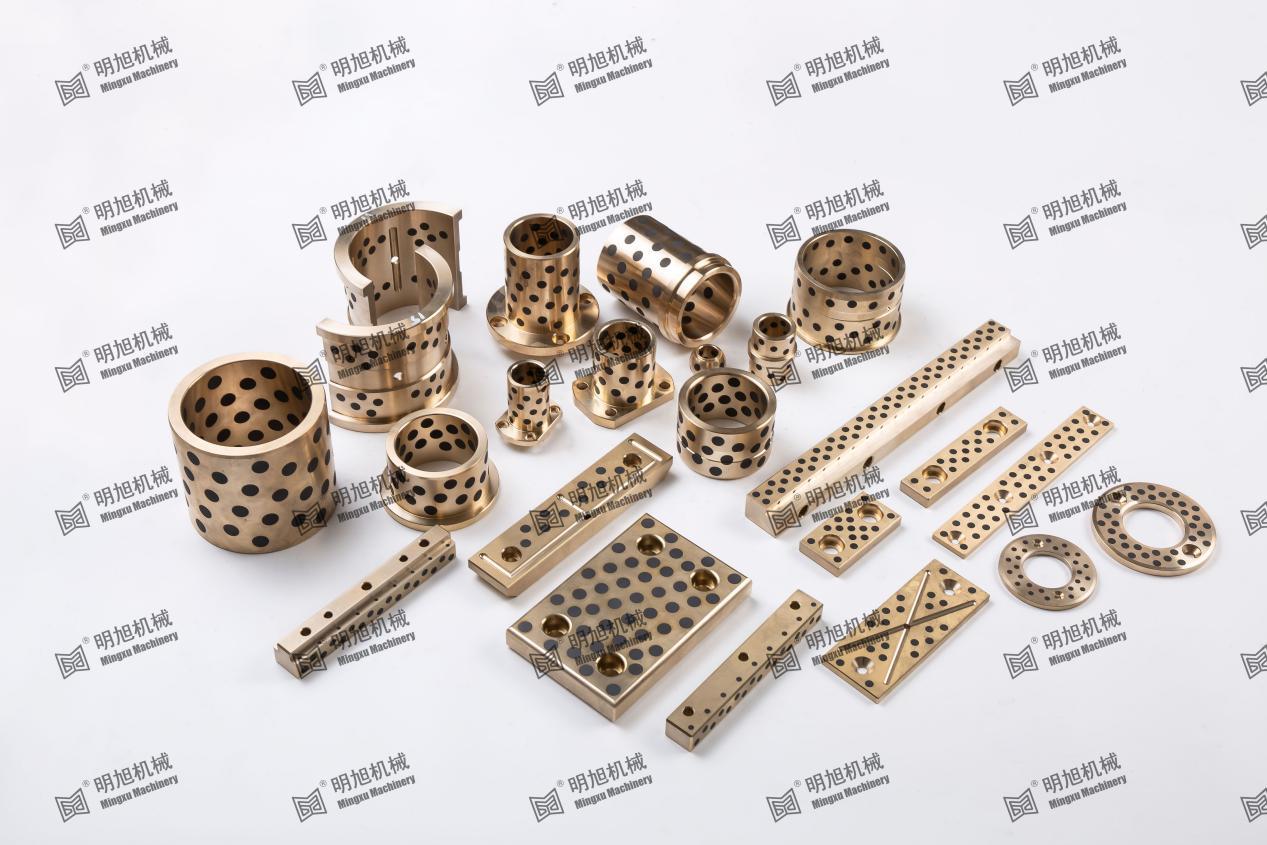
Common self-lubricating materials
· Metal-based self-lubricating materials: such as copper-based self-lubricating materials, which are often used in applications with high loads and high temperatures.
· Polymer-based self-lubricating materials: such as polytetrafluoroethylene (PTFE), polyamide, etc., are suitable for environments with high requirements for low friction and chemical stability.
· Inorganic non-metallic self-lubricating materials: such as graphite, molybdenum disulfide (MoS₂), etc., which can provide good lubrication performance under extreme conditions.
Application of self-lubricating technology
· Self-lubricating bearings: Self-lubricating bearings use solid lubricating materials embedded in the metal matrix, without the need for additional lubricating oil or grease, and are suitable for occasions requiring high load capacity and low maintenance.
· Self-lubricating tools: Coating solid lubricants on the surface of the tool or forming a lubricating film through surface treatment can greatly reduce the friction generated during the cutting process and extend the service life of the tool.
· Self-lubricating seals and mechanical seals: In high-pressure and high-sealing working environments, self-lubricating seals can reduce wear, improve sealing effects, and reduce maintenance costs.
· Self-lubricating gears and reducers: These devices will generate a lot of heat due to friction during the transmission process. The use of self-lubricating technology can effectively reduce wear and heat accumulation and ensure the long-term operation of the equipment.
Advantages of self-lubricating technology
· Reduce maintenance costs: Since they do not rely on traditional liquid lubricants, self-lubricating materials can significantly reduce the lubrication and maintenance costs of equipment.
· Improve efficiency and reliability: Reduce friction and wear to enable equipment to operate under more efficient and stable conditions, especially in extreme environments such as high temperature and high load.
· Extend equipment life: Self-lubricating technology extends the service life of mechanical parts and reduces the failure rate caused by wear through effective friction control.
· Environmental protection: Since the use of liquid lubricants is reduced, self-lubricating materials help reduce pollution and meet modern environmental protection requirements.
Self-lubricating technology provides an efficient, economical and environmentally friendly solution by reducing or eliminating the use of liquid lubricants. With the continuous development of materials science, self-lubricating technology will play an important role in more fields, improve the reliability and life of industrial equipment, and promote technological innovation and sustainable development.
Zhejiang Mingxu Machinery Manufacturing Co., Ltd. has been deeply involved in the self-lubricating bearing industry for more than ten years and is a professional manufacturer of self-lubricating bushings and wear-resistant plates. If you have any product or technical questions, you can always communicate with us: [email protected].
Contact Us