Bearing service life
When designing a bearing, it may be necessary to estimate its service life. We talk about their service life in general, but it is very difficult to accurately estimate it in terms of wear and tear under various forms of wear and conditions of use.
Usually, the estimated wear amount is calculated using the specific wear amount actually obtained in the experiment. Service life can be easily calculated using this specific amount of wear, but care should be taken when taking its value.
Even with the same P and V values, the specific wear amount can fluctuate significantly due to differences in speed, operating frequency (difference in calorific value between continuous and intermittent), type and amount of lubricant. There are many factors such as the shaft clearance (cooling effect), material (hardness) and surface roughness, the degree of foreign matter mixing, etc. Moreover, it often changes based on the passage of operating time. Therefore, the specific wear amount is used as a constant under limiting conditions. In general, it should be considered a guide for comparison.
Calculation of bearing service life
Estimates of sliding bearing service life have not been theoretically established. Therefore, in practical design, emphasis is placed on an experimental approach that allows the service conditions to be defined as far as possible and determined based on analogical reasoning by applying examples and similar examples, as well as the results of similar experiments, model experiments, or actual experiments . A very effective method is to accumulate as experience engineering, such as organizing the results of maintenance and inspection during operation and feeding them back to the next design.
As an experimental approach regarding wear, using the above numerical values for specific wear amounts allows you to calculate not only the estimated wear amount per wear time, but the wear time up to the boundary wear amount (permissible value for each device, permissible value in terms of bearing performance).
The wear calculation formula obtained from experiments is as follows.
W = k・p・v・t
W: Estimated wear size (mm)
K: Specific wear amount (mm/(N/mm2・m/s・hr) {mm/(kgf/cm2・m/min・hr)})
P: Bearing surface pressure (N/mm2 {kgf/cm2})
V: Bearing sliding speed (m/s {m/min})
T: taxiing hours (hr)
Time-based wear progression
The time-based progression of wear cannot be discussed indiscriminately either, but a typical example is shown in below figure.
Types A, B and C have been discussed differently in terms of the mechanical aspects of wear. Type A is a typical example of when the initial break-in is not done correctly without lubrication or the bearing material is not selected correctly, etc. It shows that the wear proceeds at a higher value, causing a large amount of wear debris to fall off. As a practical bearing it is not enough.
Types B and C are widely used in actual bearings. There is an initial wear part of b1 or c1 and a stable wear part of b2 or c2. The slope of the line and the location of the inflection point vary depending on the material and friction conditions. Most of the initial wear on b1 or c1 occurs during what is called the running-in period. During this period, surface roughness and uneven contact become b2 or c2 due to running-in or the adhesion of fine wear debris.
In condition b2 or c2 there is little or sometimes little wear. This condition can be maintained for long periods of time unless there is a change in the atmosphere or the friction surface. However, in many cases, due to continuous friction, viscosity changes or lubricant consumption, a mixture of foreign matter, the bearing temperature is higher, and this situation will develop to a C3 state, thereby subjecting to more wear. Wear debris behavior and material fatigue. The higher gradient of this process tends to cause sudden abnormal wear or seizure during the actual use of the bearing, causing major problems.
When estimating the service life of the bearing, it is necessary to discuss the stable wear value of b2 or c2, and perform maintenance and inspection to prevent the occurrence of c3 state.
From the perspective of stable wear, type A can be identified by b2 and c2 in addition to a higher wear rate. When the wear time is completely avoided, the value of the specific wear amount is obtained by connecting between the origin and end point of b2 or c2 and ignoring b1 and c1. Our formula for estimating wear is based on this concept.
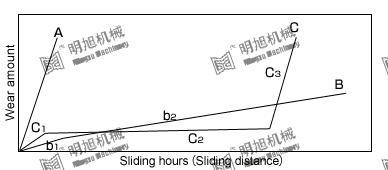
Wear estimation from actual design specifications
As mentioned above, the wear (service life) of bearings varies depending on various factors. It's very difficult to estimate wear (service life) with simple calculations at your desk.
One method currently applied defines the actual equipment usage conditions as closely as possible and performs the calculations using a wear calculation formula, using the specific wear amount from our test data that is closest to those usage conditions.
The specific wear rate depends on the lubrication conditions
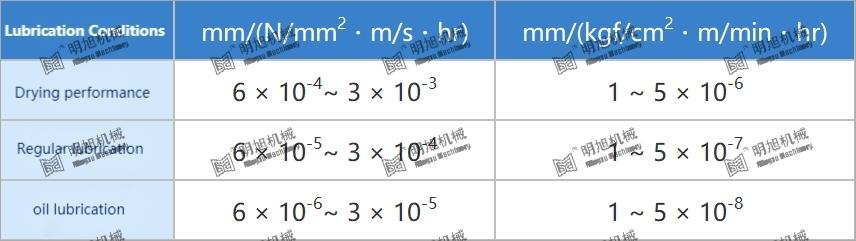
Contact Us