Determining the appropriate type of self-lubricating bearing for a specific application involves several critical considerations. Here’s a detailed guide for end-users to make informed decisions:
Understand the Application Requirements
Load Conditions: Assess the types and magnitudes of loads that the bearing will need to support. Determine if the loads are static, dynamic, or if there are shock loads involved.
Speed Requirements: Identify the operating speed of the application. Different self-lubricating bearings are designed for varying speed ranges, so it’s essential to match the bearing’s speed rating with the application’s requirements.
Environmental Conditions: Consider the operating environment, including temperature ranges, humidity, dust, chemicals, or potential exposure to corrosive elements. Some self-lubricating materials are better suited for harsh conditions than others.
Choose the Right Material
Material Properties: Evaluate the specific materials used in self-lubricating bearings (e.g., polymers, composites, metals) and their properties, such as wear resistance, thermal stability, and chemical resistance.
Compatibility: Ensure the bearing material is compatible with other materials in the assembly. For example, if the bearing is in contact with certain chemicals or other materials, it’s crucial to verify that the self-lubricating material will not degrade or react adversely.
Evaluate Friction and Wear Characteristics
Friction Coefficient: Review the friction characteristics of different self-lubricating bearings. Lower friction coefficients are generally desirable, especially in high-speed applications.
Wear Rates: Assess the expected wear rates of various self-lubricating materials under the application’s specific conditions. This information can often be found in manufacturer specifications or performance data.
Consider the Design and Size
Dimensional Requirements: Ensure that the self-lubricating bearing fits within the design constraints of the application, including its size and shape.
Design Features: Some self-lubricating bearings have specific design features that enhance their performance, such as special geometries for better load distribution or additional features for assembly.
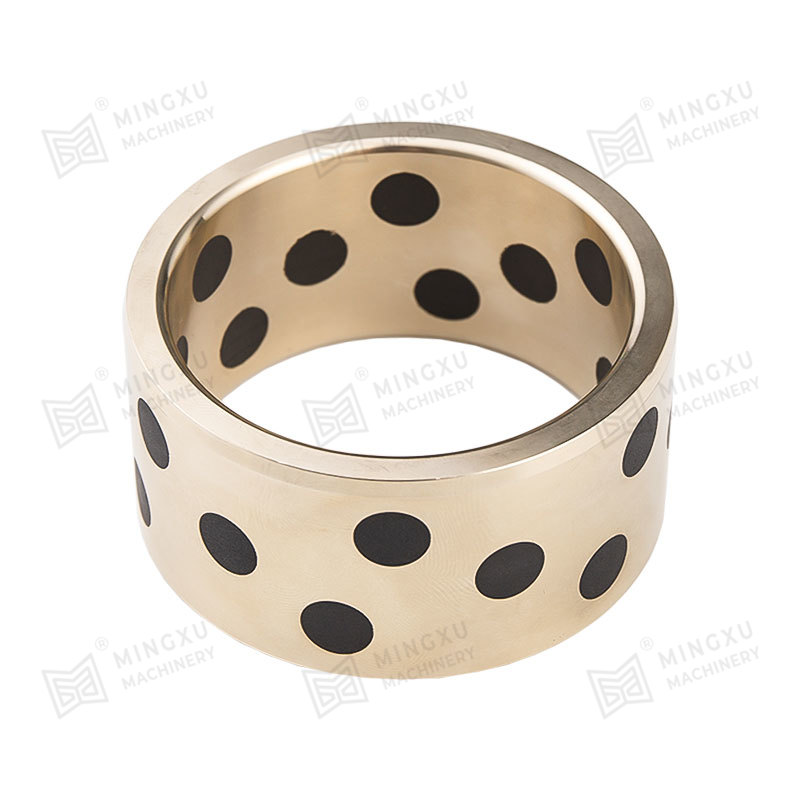
Analyze Cost and Availability
Budget Constraints: Determine the budget for the bearings. Self-lubricating bearings can vary significantly in cost depending on the materials and manufacturing processes.
Supply Chain Considerations: Evaluate the availability of the selected bearing type. Ensure that the chosen bearings can be sourced reliably and within the required timeframe.
Consult Manufacturer Specifications and Data Sheets
Performance Data: Review technical datasheets from manufacturers that provide detailed information on load ratings, speed capabilities, and wear performance under different conditions.
Technical Support: Utilize manufacturer resources, including technical support and application engineering, to help choose the right bearing for specific needs.
Prototype Testing and Evaluation
Prototyping: If possible, consider prototyping with different types of self-lubricating bearings in the application. This allows for real-world testing and performance evaluation before full-scale implementation.
Performance Monitoring: Monitor the performance of the chosen bearing during initial use to ensure it meets the application’s requirements. Look for signs of wear or failure early on to make adjustments if necessary.
Seek Expert Advice
Consult with Engineers: Engaging with engineers or specialists who have experience with self-lubricating bearings can provide insights into the best options for specific applications.
Industry Standards: Familiarize yourself with industry standards and best practices for bearing selection that might be relevant to your application.
Contact Us